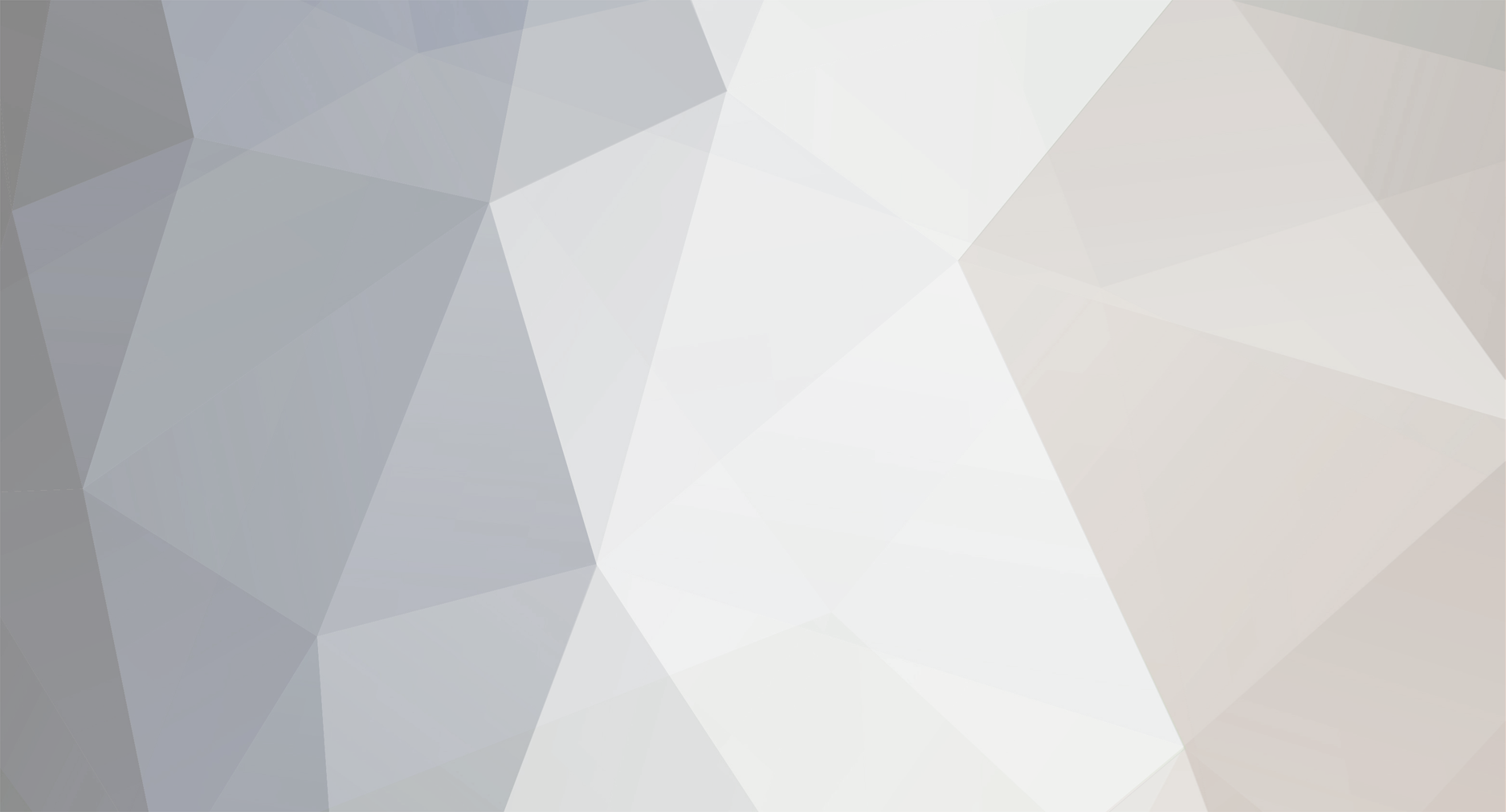
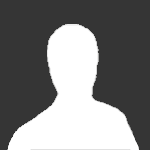
davidg
Patron-
Posts
364 -
Joined
-
Last visited
About davidg

Profile Information
-
Gender
Male
-
Location
Napton
-
Occupation
Boatbuilder
-
Boat Name
Barrow
-
Boat Location
Midlands
Recent Profile Visitors
6,141 profile views
davidg's Achievements
-
davidg started following Swan Necks - Why? , The most reddest of red paints? , When was she built? and 7 others
-
The most reddest of red paints?
davidg replied to pedroinlondon's topic in Boat Building & Maintenance
Yes. If you knew Phil Speight, who developed Craftmaster paint, you would know he has a strange delusion that Alfa Romeo make good cars despite having owned many down the years with varying degrees of reliability. -
-
Mea Culpa. When Ron Hough was signwriting that he asked me whether the second L should be capitalised. Reasoning that double L is treated as one letter I said yes. A native Welsh speaker pointed out the error later but by then it was too late. My knowledge of Welsh has improved since then๐
-
If it hasn't been out since we built the boat (at WFBCo) thirty(?) years ago it will not give up without a fight. Expect to have to hammer all manner of long thin things - chisels, screwdrivers(!) - between the collar and the middle pipe to free it, or if you're lucky unbolt the collar and the collar lifts off with the middle pipe attached. Worst case is having to take an angle grinder with a cutting disk to cut the middle pipe in half. Messy and unpleasant. I think high temperature silicone wasn't invented back then, or we hadn't come across it.
-
Where to source spare parts for a Vanette 7000 Oven and Grill
davidg replied to geehils's topic in Boat Equipment
You should have used cock grease David. Alright, it's really called gas cock grease (Molykote 1102 Gas Cock Grease 50g Tube 10395) but where's the schoolboy snigger in that.๐ -
It still is.
-
Having walked between 15E and Slaithwaite on Friday & yesterday the pound below 15E is 2ft off with not much feeding down, I think it was the short pound between 18 & 19 that was 4ft off, one of the longer pounds is a foot off and there's not a lot of water coming down the bywashes. I don't think there's any feed from Hill Top or Sparth reservoirs, it's a while since I walked over the Hill Top embankment and Tunnel End is silted up/dewatered.
-
'Tis on the book of face: (10) Facebook and I've seen Chris & Phil on Thursday so definitely for sale.
-
Sure you've got the right Trevor there? Morley?
-
Depends on how the stern tube is arranged but Iโve done this on a Grand Union boat. Remove rudder Make a piece of plywood drilled to take the stuffing box studs. Undo tail shaft coupling, remove any keys, pins etc. from shaft Tie a rope round the shaft inboard of the blade Grease one face of the plywood Push the shaft back with someone holding the rope but not all the way out When the inboard end of the tail shaft is clear of the inboard end of the stern tube remove the stuffing box packer Put the plywood on the studs greased face towards the stern tube and hold it on with the stuffing box nuts Pull the shaft the rest of the way out Very little water comes in To reassemble reverse the removal procedure. ๐ With a weed hatch getting the end of the shaft back in is easy, without a weed hatch less so.
-
You're forgetting that back in the day coal was king. At peak steam coal (1913) Cardiff shipped 13 million tons. In 10t capacity wagons (the 16t mineral was a long way off) and a six day week (the Welsh would all be in chapel on a Sunday๐) that's about 180 wagons an hour going through the Marquess of Bute's docks and making them rather a lot of money in the process. Likewise the Taff Vale Railway which moved a lot of it. Other ports and railways wanted a slice of this action and the coal owners wanted to break Cardiff's monopoly, the Vale of Neath line from Pontypool to Neath gave the GWR access to pits in the Taff & Cynon valleys and the docks at Newport at one end and in the Swansea area at the other end. For another example look at the Barry Railway and it's ruinously expensive line to link the port of Barry to the Rhymney valley on which stood Llanbradach viaduct, opened 1905, dead in the water twenty years later.
-
Not trying to be picky but.... The agents/suppliers are Kuranda, not Karunda and the stove will be a Kabola.
-
Didn't I look young, and haven't changed a bit (in my dreams). I'm surprised Nick's bike recovered from that trip, I seem to remember a lot of cleaning was involved before handing it back. Yes I think I know where they were taken but we'll leave it open for people to speculate.
-
No probably about it Ray, that is Gort. Having worked on it I can testify to what a PITA* the gearwheel is. It does come off fairly easily as the nut securing it is usually only finger tight but that leaves the end of the shaft sticking out to catch yourself on; rock & a hard place... Getting through the door between the engine room and front cabin is a challenge too. Fortunately I haven't eaten too many pies but it would be amusing to watch someone who had try it.๐ Gort now has a new owner so hopefully the boat's future is secure. *Actually head, back & shoulders but you get the idea.
-
That's what I did and similarly ran out of ideas๐