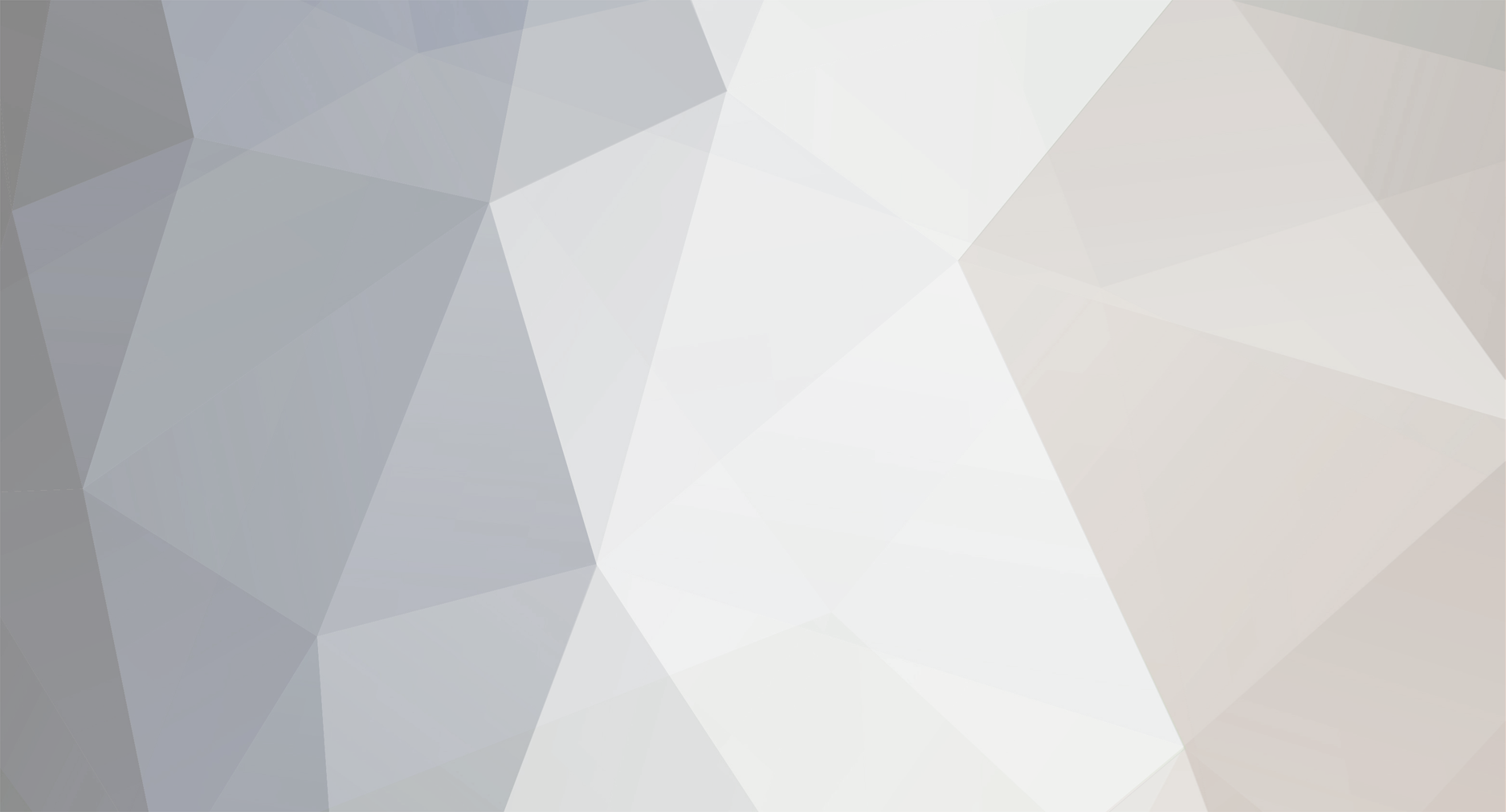
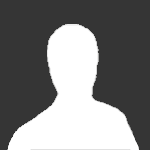
Split Pin
Member-
Posts
235 -
Joined
-
Last visited
Content Type
Profiles
Forums
Events
Gallery
Blogs
Store
Everything posted by Split Pin
-
A photograph of an X craft used during the war years, The photograph looks to be a lock on the Aire and Calder but which one?
-
Your primary filter is on the suction side of the pump so you wont get any fuel to bleed out of the filter. Up to a point the system will self bleed as there is a return to tank from the on engine secondary filter. To manually bleed out the system there are 2 bleed points on the injection pump. one either end facing out at 45 deg just below the top of the pump where the sprayer pipes are attached. The one in the video is on the delivery side of the lift pump
-
I had the same problem with a 750 fitted to a Gardner 3LW, although my tick over is 300rpm the engagement was very fierce, this is the root of the problem, when engagement either forward or reverse is selected the clutch engages rapidly without slipping, the propeller is accelerated up to speed, because there is virtually no load at this point the propeller continues to accelerate and reverses the backlash in the drive train before everything settles down hence the engagement noise. Like others I had spoken to PRM,s technical man who was very helpful suggesting that the twin accumulator modification should sort the problem, at this time the idea was very new and had been developed by a Dutch Company, another suggestion was to fit a Trolling Valve typically used in fishing boats, this allows the engine to be run at higher rpm for running ancillaries but allows the drive to be set at a lower level, the trolling valve is a proportional hydraulic valve which in its basic form switches on and off rapidly so engaging and disengaging the clutch. A soft start valve is probably the same thing now sold under a different title. I didn't like the price of either of the options at that time so set of to develop my own version , After a few experiments I found that engagement was quiet if the initial pressure was reduced to 80-100 psi. So I built a valve block that integrated a 100psi relief valve and a 2 position electrically operated valve which I fitted it into the oil pump circuit, In neutral the valve is held open. So the oil pressure is restricted to 80/100psi on engagement. The valve closes after a time delay once ahead or astern is engaged when full pressure is then applied. When the gearbox oil is cold engagement is silent. When the oil gets hotter it will on occasions knock but nowhere as heavily as without the modification. It has been on now for around 20 years without any problems.
-
When setting the tickover follow the instructions in the manual very carefully. It is set by the flanged nut on the end of the governor housing, not the screws on the throttle lever. The rack buffer (the hex screw as seen in the pic above from Chris) needs to be carefully set as well particularly when the tickover is set to 320 rpm as per the manual.. The spring that is fitted looks like it was for a 6LW where it has to do much more work, I assume that you have ordered this one https://gardnerspares.com/product/spring-rack-bar-2-point/ Where is your boat moored? I may be able to help.
-
If it’s a South African repatriation then it will have been fully overhauled by someone, unless it sounds like it’s falling apart and burning oil when running there is little to be bothered about. Minor oil leaks from the block to crankcase and block to cylinder head are the most common issue , there are plenty of pipe connections that can leak but once sorted are usually ok. There are quite a few 70 footers with 2LW’s fitted, at 28bhp they are more than up to the job on rivers. Like any old engine there can be issues with corrosion, The water rails are common areas where corrosion can cause failure.
-
Don't really know why it had failed, given the level of bodging, it was probably due to being very poorly assembled, maybe even bad regrinding, when I checked the bearings and crankshaft there was more taper in the grinding than the specified clearances for the bearing!
-
It sure did, it was from a South African rebuild, it had done very little running after a rebuild before the big end failed, there were bits of shell bearing lying around the sump.
-
In true Blue Peter style "One I prepared earlier"
-
Ferrous has a 24" X 20" prop. Edwin made a mould from an older Bolinder Blade which was probably ex Claytons of Oldbury. Then Cast his own propeller. Its driven by a 3LW and 1.5:1 gearbox so plenty of oomf!
-
When it was possible to have it as a tender Edwin took it all over the system, once the licensing changed it was put into storage at the family home. If my memory is correct it was originally fitted with an LE Velocete engine. It is now fitted with a 2cl Kubota, Don't know how the licencing system updates but it probably has a one month licence to cover the BCN challenge.
-
What size nut fits this spanner?
Split Pin replied to BlueStringPudding's topic in Boat Building & Maintenance
That is an enots fitting and if you had the correct spanner it would have 3/16" or 1/4 whitworth stamped on it depending on the pipe size -
Planning to Visit The Chesterfield Canal? Make Haste!
Split Pin replied to cheshire~rose's topic in General Boating
-
It maybe that the easy one was already towards the end of the fuel element travel in which case it wouldnt be in a position to let more fuel in so nothing to pump. If the engine is running correctly there is probably nothing to be concerned about. You might try it again now that the engine has been running and see if it is the same or if it is now about the same as the other one.
-
Slow idle speed engine with hydraulic PRM gearbox
Split Pin replied to Gédeau's topic in Boat Building & Maintenance
When Gardner reintroduced the 2LW they supplied them with a PRM260. The official tickover is set at 410rpm but can be reduced to 330rpm I have not heard of anyone having a problem with the clutches slipping. I have a PRM750 on a 3LW with the tickover set at 310 rpm it has been installed for around 20 years without any problem, we also have a PRM500 attached to a 3LW which has done over 12,000 hrs, it was stripped a couple of years ago for inspection, the clutch plates showed hardly any sign of wear. You only need full clutch pressure to deliver max power so any shortfall of pressure at lower rpm is generally inconsequential. I have also had a PRM 160 fitted to a 3LW that was transfered to a Perkins 3 Cly and is now on a 2LW, it is now comming up to 37 years old and is still on its original (sintered bronze) clutch plates. The more common problem with slow tickover is gearbox rattle, this can be overcome by fitting an R&D high deflection drive plate. Steven -
The Stourbridge Canal was never a part of the BCN. The propreiters were the Stourbridge Navigation Company. At one time there was a BCN boundry marker next to the road bridge at the bottom of the Delph Locks
-
CAV manual says 12cc of oil, it soaks into a felt pad. It should ideally be done a couple of times a year
-
I get about 4000 kWh per year from 4 kW instalation in the West Midlands and four of my panel face South East rather than directly south.
-
Most domestic calorifiers are of the indirect vented type, the cold water feed is from a seperate stoarage tank, and they have a vent pipe back to the header tank, these are typically rated at 10 mt head of water which equates to 1Bar or 15 PSI. It is possible to use a vented type in a marine situation, but the system need to work at the appropriate pressure. Steven
-
I was answering your question about LW's
-
LW'S were available in handed pairs if required so it all depends on where it originated from. Normal roation is clockwise when viewed from the non flywheel end
-
My family has two boats with 3LW's and 2:1 gearboxes one is is 50 ft the other 58ft both are fitted with the same prop as in the picture. They are 23" X 23" and as can be seen are are of a large blade area. Normal cruising revs are 500, max revs are 1000, Almost never use anything over 750rpm. Boat stops within its own lengh in deep water. Although you cannot fit 23" dia the nearer you can get will give you a good result. Steven
-
-
-
Oil change gearbox newage prm 402D2
Split Pin replied to Paul canal's topic in Boat Building & Maintenance
The knurled silver knob doesnt look like an original part, that is where the breather is usually located. The dipstick should be attached to the square headed plug as shown in photograph 1, it is part of the plug and can only be found when the plug is removed, the drain plug is not visible on either of your photographs it is in the centre underneath nearest the flywheel. The plug shown with the blue arrow is on the hydraulic pressure circuit and is normally used with a trolling valve. The large Hex plug on the side in pic 2 may have a filter behind it on the suction pipe inlet, dont know when they started to fit them but my 750 has one