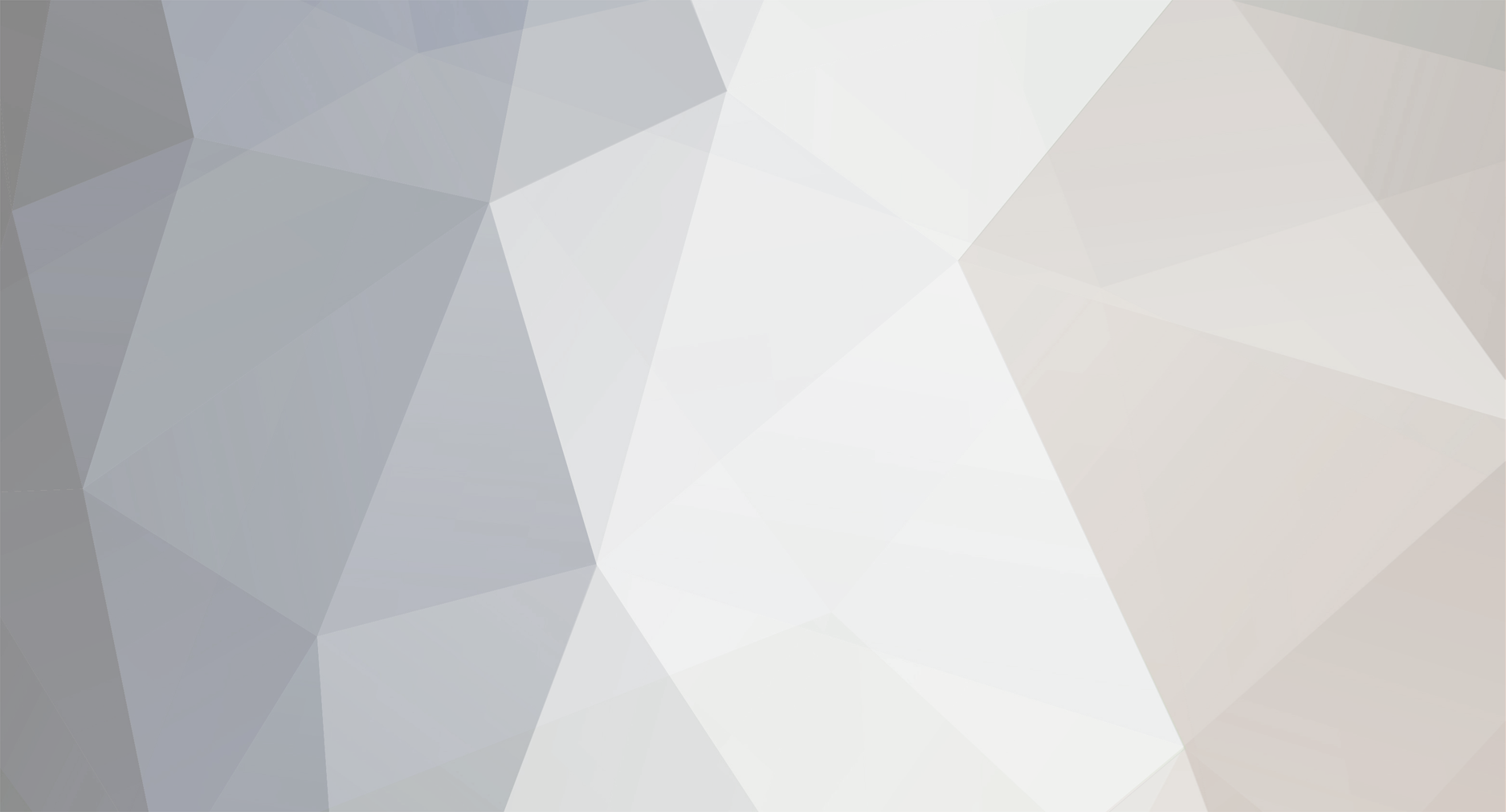
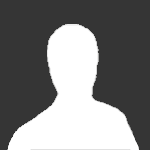
MarkH2159
Patron-
Posts
166 -
Joined
-
Last visited
Content Type
Profiles
Forums
Events
Gallery
Blogs
Store
Everything posted by MarkH2159
-
Ah well, the safety is in the BMS settings and knowing how to read and adjust them. I know I am not 100% in any single cell because the BMS is constantly monitoring and has an individual Cell High Voltage Disconnect. It also has a Cell Low Voltage Disconnect, as well as a Pack Sum Voltage High/Low, Cell Differential Voltage Disconnect etc. The only time I did take it all to 100% is when I was performing the initial Top Balancing. So to remind you how I am able to avoid overcharging or any other 'dangerous' situations is by using a decent BMS with the correct settings which has safety features that cannot be exceeded. Thanks for the insult that I 'blindly tell the world that they are safe and happy in that regime' The fact is I am neither blind nor living dangerously. I am just one of many who have self built Lithium Batteries quite successfully and we are all quite happy about them. Now if that somehow scares you, then carry on and be scared, but do not try to tell others how wrong we are because the proof is in the pudding.
-
LiFePO4 Lithium Batteries - the lazy way
MarkH2159 replied to TheBiscuits's topic in General Boating
Yes and yes. All voltages are user configurable. Cell High/Low Voltage disconnect, Pack Sum High/Low voltage disconnect, Balance start voltage, Cell differential Balance start etc etc. -
Obviously you missed my post where I said I set the BMS is set to cut the charge at a Pack Voltage of 14v and the discharge at 12v, This keeps the LiFePOs in the safe zone (90% high - 10% low) and that along with regular cycling is all they need.
-
Spot On !!! And at 0.006 ohms the extra heat created would be........Not Discernable
-
I have no need to calculate the power dissipation. You seem to think the unused alternator power is being somehow redirected to create heat, but that is not the way it works at all. I do know that the load on my alternator is reduced, therefore the heat it produces is less and life of unit and belt is increased. I also know that B2B units cost a lot of money and often generate a lot of heat and are another complicated electronic gizmo prone to failure. I also know that at a cost of around £4 I have put in a simple and safe method of achieving the necessary. Changing the alternator or its regulator is definitely not necessary and I am not the only one who has proved it.
-
?? The reason for the 14v Charge cut off is so that the Lithiums do not actually reach their full 100% charge capacity. Unlike lead Acids the LiFePO4s do not fair well being fully charged all the time. Similarly the low voltage discharge cut off is set to 12v so they never get to being totally flat either. Using the range 14v to 12v keeps the Lithium cells running at between 90 and 10% charge, a range in which they are both happy and safe and gives me a usable 80% of the 280AH total. Do not confuse LiFePO4 with Lithium Ion batteries. LiFePO4s are perfectly safe and happy at under 100% charge state.
-
LiFePO4 Lithium Batteries - the lazy way
MarkH2159 replied to TheBiscuits's topic in General Boating
I bought on eBay but the seller is Sterling. https://www.ebay.co.uk/itm/Daly-12V-100A-BMS-4s-lithium-w-balance-leads-NTC-bluetooth-bundle-UK-stock-/324695653537?mkcid=16&mkevt=1&_trksid=p2349624.m46890.l49286&mkrid=710-127635-2958-0 -
LiFePO4 Lithium Batteries - the lazy way
MarkH2159 replied to TheBiscuits's topic in General Boating
My 100A Daly BMS purchased from Mr Sterling does indeed have a Low Temperature charge disconnect. It actually has programmable Charge High Temp Disconnect Charge LowTemp Disconnect Discharge High Temp Disconnect Discharge Low Temp Disconnect Differential Temp Protect MOS Temp Protect -
ah yes, apologies, my bad, I spent a lot of time in the southern hemisphere where things do happen the other way round.
-
You speak from experience..? There is no discernable extra heat produced as the increased resistance is actually minimal. It is basically just enough to cause the regulator to drop the output of the alternator. I repeat, no heat, no insulation melting, no sign of any such issues. It is in a single coil, held by small zip ties, in an enclosed engine compartment. Nothing is going to happen because 10mm2 cable can easily handle the total output of the alternator which is 70 amps.
-
Alternator is direct to AGM via 10mm2 cable 2m long. No fancy B2B or DC to DC, no switches etc. The long wire method proves them all to be totally unnecessary and a waste of money. Keep it simple is always the best way.
-
I refer to the 'media hype' of today along with of course all previous recent weather hype such as 'snow bomb to blanket the whole of the country' etc etc. It is quite obvious that the media are now exaggerating all weather related phenomena, possibly under instruction from those in control who want us all to stay home.
-
Similar track..???? 35 years ago the depression tracked down the North Sea moving in a south westerly direction. I think you will find that the predicted track of Fridays depression is exactly the opposite.
-
The Alternator is connected to the AGM which is connected to the Inverter which is connected to the Lithium. Basically all three units are in parallel. The reason for this is threefold... As Lithiums do not like temperature change and can be damaged if attempts are made to charge at very low temperatures, the BMS is programmed to cut off the Lithium at 5C. By putting the Lithium inside, in the same locker as the Inverter, it overcomes the possibility of it ever suffering freezing temperatures. Secondly it extends the amount of wiring between the alternator and the Lithium thereby introducing a resistance which artificially reduces the lithium ability to suck too much charge from the alternator. Thirdly as the Lithium is providing most of the power demand of the inverter, having it close by on short cables reduces any cabling losses. By using the 'long wire' and 10mm2 cable I am still connecting the alternator with a wire of sufficient size to handle its total rated output of 70 amps but the resistance induced automatically cuts the amperage. This means that there is no need for any kind of ballast resistance or other add in that could complicate things and produce heat, thereby wasting energy.
-
Yes you can. Filter it first- a pair of old tights over a drum works well. Mix it with a decent amount of regular diesel and it will do no harm. I ran a Fiesta 1800 diesel on a similar 50:50 mixture for years when my son worked in a chip shop.
-
Have a look on YouTube at Narrowboat Pirate who recently coated her hull with epoxy and proved the shot blaster theory wrong. I was drydocking and coating ships for over 40 years and there was never any need to shot blast before applying epoxy coatings. The costs were 100s of times more than a narrowboat and paint manufacturers such as Jotun, Sigma, Hempel etc were all happy to give a warranty. Its all in the preparation.
-
Just done Leamington to Napton in the 'raging' not so strong winds with no problem at all. We did stop at 3 pm just as it became a bit blustery and I was fed up with doing locks. If I had believed the media hype I might have been scared to death or gone to the pub instead.
-
I have recently installed a LiFePO4 battery using the 'fudge' method and can report excellent results. Basically I have thrown out my ageing but still good Lead Acids ( 8 x 110 AH) and put in a self built 280AH LiFePO4 in parallel with an Alphahouse Batteries 100AH Deep Cycle AGM. The AGM is in the engine bay battery box, with all the connections running to/from it. Input from Alternator and Solar, Output to Boat services and 2 Kw Inverter/Charger. The new 280AH LiFePO4 with Daly 100A BMS is inside, connected directly to the inverter via an isolator. Having an ageing Beta 35 with a 70 amp domestic alternator I had to be mindful of the charge routine and the potential for the LiFePO4 to suck the alternator to death. instead of going the expensive DC to DC charger route, I chose the 'long wire' method to limit the output of my alternator to a maximum of 45 amps which it is happy to produce all day long with no overheating issues. So... Alternator to AGM via 2m x 10mm2 cable. AGM to Inverter via 2m x 70 mm2 cable - The ones that were originally in place. LiFePO4 to Inverter via 0.5m x 35 mm2 Cable and Isolator. I use a Shunt based Battery Monitor on the AGM and the Daly BMS to monitor the voltages and amps in/out of each battery. I have nothing but positives to report.... Amount of available power with no worries about low voltages or Lead Acid 'damage' Inverter can be on 24/7 with no issues. No need to run engine or generator to charge batteries every day, instead I can easily go 3 days between charges. Run time of engine or generator is around 1/4 of previous to achieve 100% full batteries. Ability to use the washing machine or microwave anytime without worrying about 'killing' batteries. When running the engine I see around 45 amps output from the Alternator at 1500 rpm due to the 'long wire' set up reducing the ability of the LiFePO4 to suck charge. When the LiFePO4 is charging I can see it taking around 40 amps while the AGM takes from 5 amps down to 0.5 as it reaches 100%. The Daly BMS is set to cut off at a pack total voltage of 14v which keeps the LiFePO4 slightly under 100% full and quite happy. When the BMS cuts off charge there is no noticeable change as the alternator simply continues charging the AGM as it would normally. Solar quite happily charges both batteries at full rate with no noticeable difference. Genny bangs 60 amps into LiFePO4 all the time it is running so takes less time. My system sits between 13.8 and 13.2 volts all day every day no matter what I do. The AGM sits at near 100% charge most of the time, only when the LiFePO4 is down to 30% does the AGM start to drop to around 95%. Best part is being able to achieve all of the above for less than the price of 4 new Lead Acids, enough to make anyone smile. Basically I built 2 LiFePO4s and sold one as well as flogging the old LAs.
-
A sobering tale about not trusting surveyors.
MarkH2159 replied to doratheexplorer's topic in General Boating
Spot on as ever 🙂 I surveyed my own boat whilst it was in the water. Most of the time was spent going through the extensive history and meticulous documentation that the owner had kept so well. Seeing the maintenance records and a quick look under the floor was basically enough. Also the fact that it is a Peter Nicholls build told me quite a lot about it. Of course with a different boat, possibly poorly maintained and lacking history, I probably wouldnt have bothered. Some of had good results with surveys throwing up issues which the seller has fixed before the money has been handed over, but many have not. Caveat Emptor and all that. -
I have an old Beta 35, the mechanical fuel pump was ditched years ago and an electric one fitted. Dead simple to connect the pipework and have a feed run from the ignition switch. When changing fuel filters the pump makes life a lot easier bleeding the system.
-
We lived as a family of 4 in a permanent caravan for years, 32 ft Bluebird as I recall. It had a brilliant 'Murphy type' fold down double bed that simply went up into the wall, still made up. Then a dining table folded out from the bed base. It was so simple to fold the table and lower the bed down, all ready for use. If I was remodelling my boat I would definitely be incorporating something similar.
-
Finding an overnight mooring on the western K&A
MarkH2159 replied to Grassman's topic in General Boating
I can concur with your concerns regarding finding a mooring on that stretch, having done the trip myself last May/June. The river is difficult to find decent places to stop, having more "NO MOORING" signs than the Thames, as well as the usual continuous moorers occupying every available slot. At Hanham lock the 48 hr moorings were full but I was lucky to find a spot on the very nice pontoon at Bitton just before bridge 211. In Bath after Bridge 202 there were plenty of mootings on the river. Continuing east I had no further issues finding spots to moor and stopped just after Dundas services on rings. From then onwards Avoncliffe to the other side of BoA was very difficult to find anywhere half decent. Moulton Drive was ok but the bank is very soft and passing boats continually pulled the pins out. Next stop at Seend was good and I got lucky grabbing a spot just as a hire boat left. Further east the 48 hr moorings at Bishop Cannings were all occupied, as was Pewsey and Gt Bedwyn. I stopped one night on a lock landing, arriving late and leaving early so as not to cause inconvenience. From there onwards I had no real issues finding decent mooring spots, but noted that anywhere with any decent access to a road was always occupied. -
I recall seeing something about the redevelopment of Marple Wharf years ago but it seems planning permission was denied. Well things may be changing fairly soon from my observations of the past few days. There has been a CaRT Team measuring up and looking to move things around and it would appear the original plan is now a go ahead deal. This is what I managed to 'overhear' them discussing. The old Wharf building will have a new role. The New Horizons PWD Boat will be moving to be moored closer to the Wharf building - saw them measuring up and assessing the arrangements 2 days ago. It will go partially under the wharf building. The old building in the wharf yard will become the Toilet/Elsan point but access will be limited because of the New Horizons boat. The water point will likely be moved to the lock landing around the corner because of access limitation as above. Wait for it.... The existing New Horizons yard, CaRT yard and toilet block etc will be gone and 6 new houses built on the site.
-
This post cannot be displayed because it is in a forum which requires at least 10 posts to view.