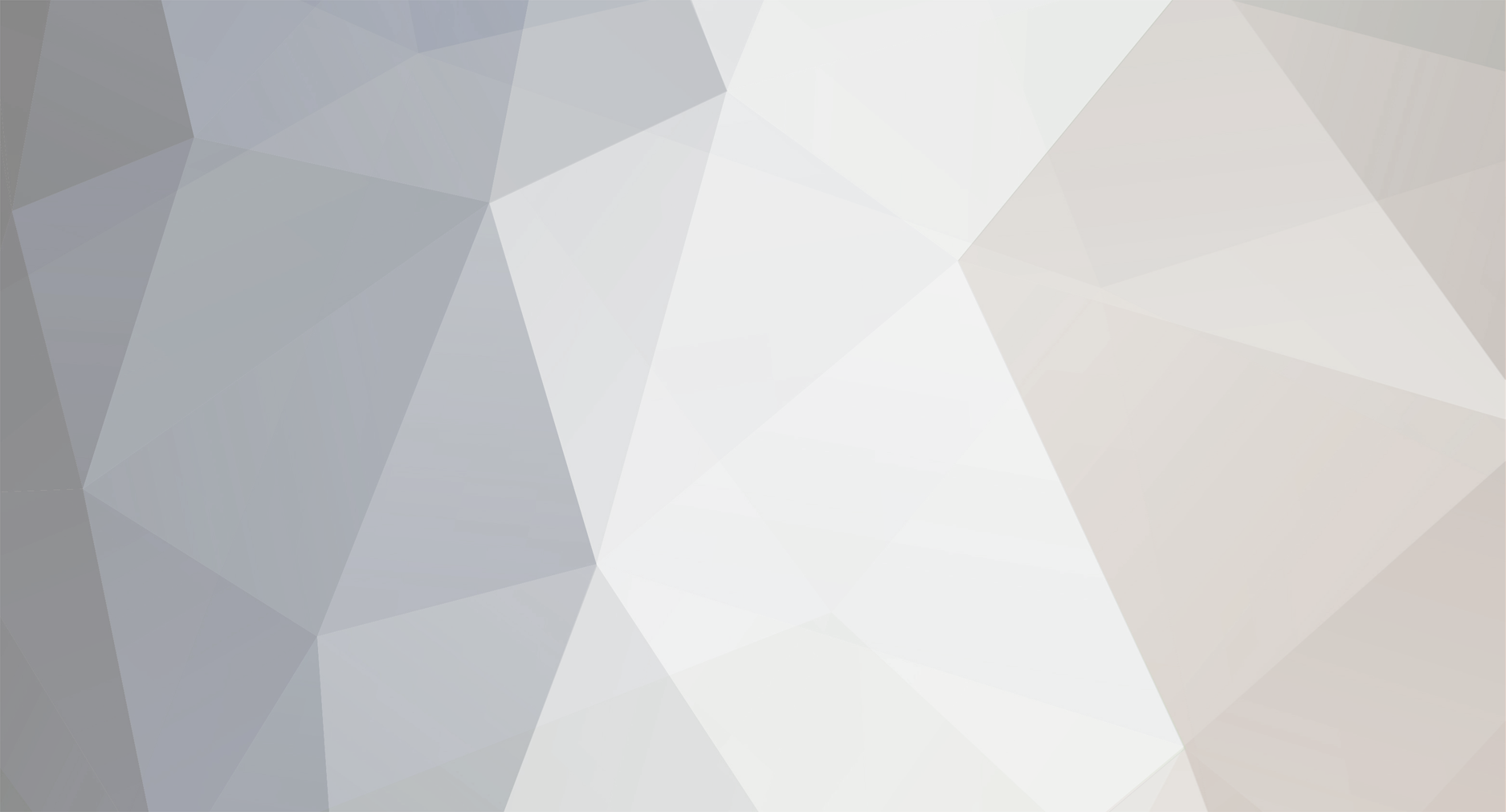
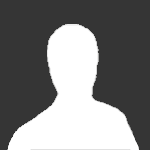
cheesegas
Member-
Posts
1,073 -
Joined
-
Last visited
Content Type
Profiles
Forums
Events
Gallery
Blogs
Store
Everything posted by cheesegas
-
They’re good for simple stuff and get you home fixes but they’re never to be trusted with anything major like engine or gearbox works. Their sister company Key Diesels have a habit of supplying poorly refurbished engines and gearboxes with only a paint job and cursory servicing, and the installs are very very poorly done. They’re very keen to suggest a new engine/gearbox when the original is repairable. Met lots of people who have been stung by them, and it’s nigh on impossible to get them to return to sort out their bodges. Stuff like engine mounts bodged from undersized steel and bolts (welding is expensive…), unsupported fuel lines with heavy filters which soon snap them, engine alignment not done at all, that sort of thing.
-
Generally speaking, most engines are similar levels of difficulty to service. The exception are those with a timing belt to change which are thankfully few and far between - the Ford XLD and Lombardinis are the most common. Air cooled engines like some Listers don't have any coolant to change, and some may not even have a disposable oil filter, just a gauze to clean. Some engine installations can be difficult to bleed after changing the fuel filters though, and sometimes a coolant hose goes through the domestic alternator belt so the cooling system has to be drained to get a new belt on. Best to thread on a couple of spares at the same time and cable tie them out the way so you don't need to drain it on the next service. As mentioned above, the space around it makes a huge difference; some are butted hard up against the bulkhead which makes belt changes difficult, others have a calorifier in the engine room which can block access to filters. Modern semi trad boats are often the worst as some builders cram in a Webasto, calorifier and a big battery bank, all the while only having access directly down on top of the engine.
-
The operating mode of the thieves of running generators appears to be two up on a quad bike - by the time you've noticed you can't hear your generator and stuck your head outside, they're long gone.
-
These are really good, I do some work for a TV lighting company who have a whole ton of these. They replaced a fleet of the Hondas slowly as so many were getting stolen on site, the Champions are stolen a bit less frequently but it's less of a hit if they get robbed. They're serviced regularly but are used hard with nasty inductive loads and thrown into trucks day in day out and they do very well. Only issue seems to be the fold out handle.
-
One of the things I do is temporary power for events which includes a lot of festivals etc paid for by the council. Generator and PA noise levels are usually set by the very scientific method of the council person standing next to the person's house who is known for complaining and seeing if they can hear the generators...
-
Yep, this is what I was saying earlier - sound levels are only half the story, it's about the content of it too, as to how we perceive a loud or annoying sound. I was moored behind a boat with a vintage engine who ran it for a couple hours a day - this probably had a low dbA reading, but it had enough low frequency energy to cause things in my kitchen to rattle and vibrate which was very annoying.
-
Annoyingly there’s no standard way of measuring sound levels with generators - A, C or no dB scale weighting also plays a massive role in perceived sound pressure levels. Because of your ear’s loudness curve (it’s nonlinear across the frequencies), a generator which appears quieter on paper might be louder in person and vice versa due to the ear being more sensitive to certain frequencies. Also, positioning of the generator matters as the exhaust end is usually louder. ‘A’ weighting on the dB scale aims to match the loudness curve issue, and there’s an EC directive in which includes measuring sound levels for outdoor equipment but not every manufacturer follows it. Anyway, Champion rate it at 56dbA at 7m at idle. The Honda 22i is 72dbA at 1m so direct comparison is difficult. Theres a few YouTubers who have set up both generators in the same environment (outside, on a lawn etc) with a SPL meter the same distance away with the same load on the generator which is a good way to get a direct comparison. I think the Champion is definitely louder when heavily loaded having heard both though. However, the Hondas are more expensive and are a theft magnet - I know a few people on the Stort/top of the Lea who have had theirs nicked…whilst running! I’d rather lose a £600 Champion than a Honda at almost double that. Storing it outside on the boat is difficult too, it needs to be locked up whilst being hidden. Even still, a minute with a grinder will free it. It’s a balance between price, reliability and noise levels and also theft potential!
-
If it's the Champion you've ordered, it's a dead good little generator. It's a rebranded Lifan with better UK based support, there's Lifan stickers are all over the case inside. They make a lot of engines under their own name and also under contract for Honda (I think!), I put one into a road legal mini bike and did many thousands of miles on it with no issues. It's worth noting though that as Tony said, it'll rev up and be noticeably louder when under load. As lithium batteries have a very low internal resistance right up until they're almost full, it'll be running hard for the whole charge cycle, unlike lead where the generator gets quieter pretty soon into the cycle. It however doesn't come with an engine hour meter - I fitted a vibration activated one from Amazon for about £10 so I can keep track of servicing, especially important with lithium as it runs at higher power levels.
-
Alternator connection to battery
cheesegas replied to Jen-in-Wellies's topic in Boat Building & Maintenance
Did an experiment on a generic ebay special A127 with a fecked casing...storage scope on the output, outputting 30a ish into a battery and load, disconnected the alternator and only saw a transient of 15v. This will obviously vary from alternator to alternator but I did expect more. -
Alternator connection to battery
cheesegas replied to Jen-in-Wellies's topic in Boat Building & Maintenance
It's a very very good idea to fuse your alternator despite it not being a requirement. I'll try and find the photo but I saw a boat where the alternator bolt had worked loose and it had dropped onto the oil filter, melting a hole in the filter (positive stud contacted it first) and spraying hot oil over the place which somehow didn't catch fire. Another incident was a 175a domestic alternator positive which rubbed through to copper on a bracket and shorted but the lithium's BMS stopped a fire happening by disconnecting. It's worth noting that the 400a main battery fuse did not blow. A thick, unfused cable often running near a hot exhaust manifold and over a vibrating thing connected to negative has got potential issues all over it. The cable should be sized for volt drop, not maximum current capacity and fused appropriately so the chances of the fuse randomly blowing and frying your alternator is very slim. In my experience, disconnecting the batteries with the engine running rarely does any damage as most have built in protection anyway. Never have I seen it happen, not even blowing one diode. Wouldn't advise doing it routinely as the avalanche diodes have a finite lifespan though. -
BS7909 covers temporary electrics, and under that it should be rubber H07. Arctic has no place any more… However, if it’s always in place, it’s debatable if it’s temporary or permanent. Also, armoured cabling doesn’t cope with repeated flexing.
-
40m is a pretty long cable. Check it's 2.5mm2 flex - if it's 1.5mm2, the earth loop impedance might be pretty high. You need a Megger/multifunctional tester to check it, but generally speaking, if it's 2.5mm2 and there's not a massive amount of cabling on either end you should be ok. If there's a dead short from live to earth or live to neutral in the cable or at the boat before the consumer unit, the circuit breaker on the generator won't trip. The cable will simply get hotter and hotter and hotter until something melts, usually one of the plugs on either end.
-
What Pi is this? It sounds high. My system's base load with a Cerbo, Teltonika router, 80mm toilet fan, cheap Aliexpress modbus relay board, MPPT and Zeus alternator regulator only draws 12-13w. VRM is free and works very well with minimal setup.
-
That's Matt Miller who runs it. Good guy, glad you've got in contact. Interesting fact: there's no pumps in the dry dock, it was an old BW maintainence depot. It fills from the canal as you'd expect, but there's a 1' culvert which empties the dock into a largely unmapped underground river which passes under the canal. No one knows where it ends up, but it has got blocked in the past apparently.
-
Yep, I've heard similar things about the customer service but I don't have any first hand experience.
-
The Sterling is rated on input current, not output which is deceiving. In reality, the output throttles when it gets warm, and the efficiency appears to be much less than the Victron. The 12v-48v in particular is especially bad. Should be consigned to the bin along with most Sterling kit. Not had much experience with the Renogys but they appear to be good, albeit not many options to configure them.
-
An external alternator regulator monitors the temperature of the alternator and reduces the field current if it goes above a set threshold, it won't cook itself. I have a 560ah lithium bank charged directly by a single 90a rated alternator and a Zeus regulator. Keeping the stator at 70 degrees, I get between 50-70a from it depending on ambient temps and how hard the engine's working as this heats the engine bay. By ducting in air I could probably get this figure up a bit more. If the external regulator were to fail and give full field to the alternator, the BMS would shut off the charging FET and the batteries would be safe. However, this is extremely unlikely to happen as the regulator will shut down if the voltage goes above a set threshold. With an external regulator, I get the most power possible from the alternator without it overheating, and no losses in a B2B passing high currents.
-
Of course, that's why I said with an alternator regulator although I should have been more clear and said 'external lithium compatible alternator regulator'. I agree it is cheaper to use a B2B though. The BMS in a drop in battery should never switch off in a properly designed system - it's there as a last resort to disconnect the cells from the load/charge source and protect it from over-voltage etc. However, there is still a chance it may happen 'randomly' in case of a cell imbalance for example, which may damage the alternator but in my experience, most brand-name alternators will not be damaged.
-
It's more efficient to do it the other way around - single alternator charges the lifepo4 directly with an alternator regulator, then a small B2B keeps the starter battery topped up. That way the B2B isn't having to deal with high currents, and you're getting more power out of the alternator.
-
Not quite - that's probably the peak torque speed you're reading. Have a look at the spec sheet for the EU range of engines here: https://kuk.kubota-eu.com/wp-content/uploads/2024/05/Diesel-Engine-Guide_Apr-2024.pdf If you look at the torque vs RPM graphs for each individual engine, they start at 1300rpm. Take the Beta 38 for example, which uses the Kubota V1505 as the base engine. Beta's graph starts at around 900rpm(https://betamarine.co.uk/wp-content/uploads/2020/07/B38-KC-Power-Graph.pdf) , and Kubota's at 1300rpm (https://global.engine.kubota.co.jp/en/products/product_pdf/34_pdf_1.pdf) The reason most industrial engines are rated at a governed speed of 1500rpm, 1800rpm, 3000rpm or 3600rpm is because they're commonly used in generators; 1500 and 3000rpm is the speed needed to drive a 4 and 2 pole alternator respectively for a 50hz output, and 1800 and 3600rpm is for 60hz.
-
Be careful - there are a few versions of exhaust around, some genuine Webasto and some not which look very similar. Some of them aren't seam welded and are either spot welded or crimped together. This means that blocking the drain hole doesn't make it gas tight.
-
I'd also like to add that toilet emptying intervals is very very variable if there's two of you living on board but you both do a combination of working from home and from site/office. Sometimes a 12 litre urine container takes over a week to fill if we're both not working from home and the hours are long, other times it's a few days if both on the boat working/eating/drinking there. Likewise, the poopy bit of the toilet can go well over a month, or sometimes it's under a month.
-
It is possible to change the low voltage cutoff, but you need the Webasto software and box which is around £600 - an engineer will probably charge less than the cost of the box to reprogram it. The highest current draw is when the heater is starting up and shutting down when the glowplug is switched on, this is around 8-10a for most heaters. The battery voltage will sag under the load, and if it drops below a certain threshold for a certain amount of time then it shuts down. Lifepo4 nominal voltage will sag less than lead acid, and the voltage is higher so they do indeed tend to work better with Webastos.
-
Indeed. You need to allocate space and time to do the composting bit of it, but for some boat usage patterns this is much easier and more convenient than a pump out.
-
I have one with a fan. It draws 300ma which is noticeable (~7ah per 24hrs which equates to 6 mins engine runtime) but hardly a deal breaker. Doesn't smell outside at all, unless you stick your nose right up against the vent, and it smells inside less than a regular water toilet in a house. My friend in a marina has one with a fan and internal carbon filter, which I thought would smell but it doesn't. After the marina's pump out boat broke for a month, making everyone walk 5 min back and forth to the marina toilets in the middle of winter, a lot of people switched to compost. I'd recommend owning one for a while before making assumptions. 😉