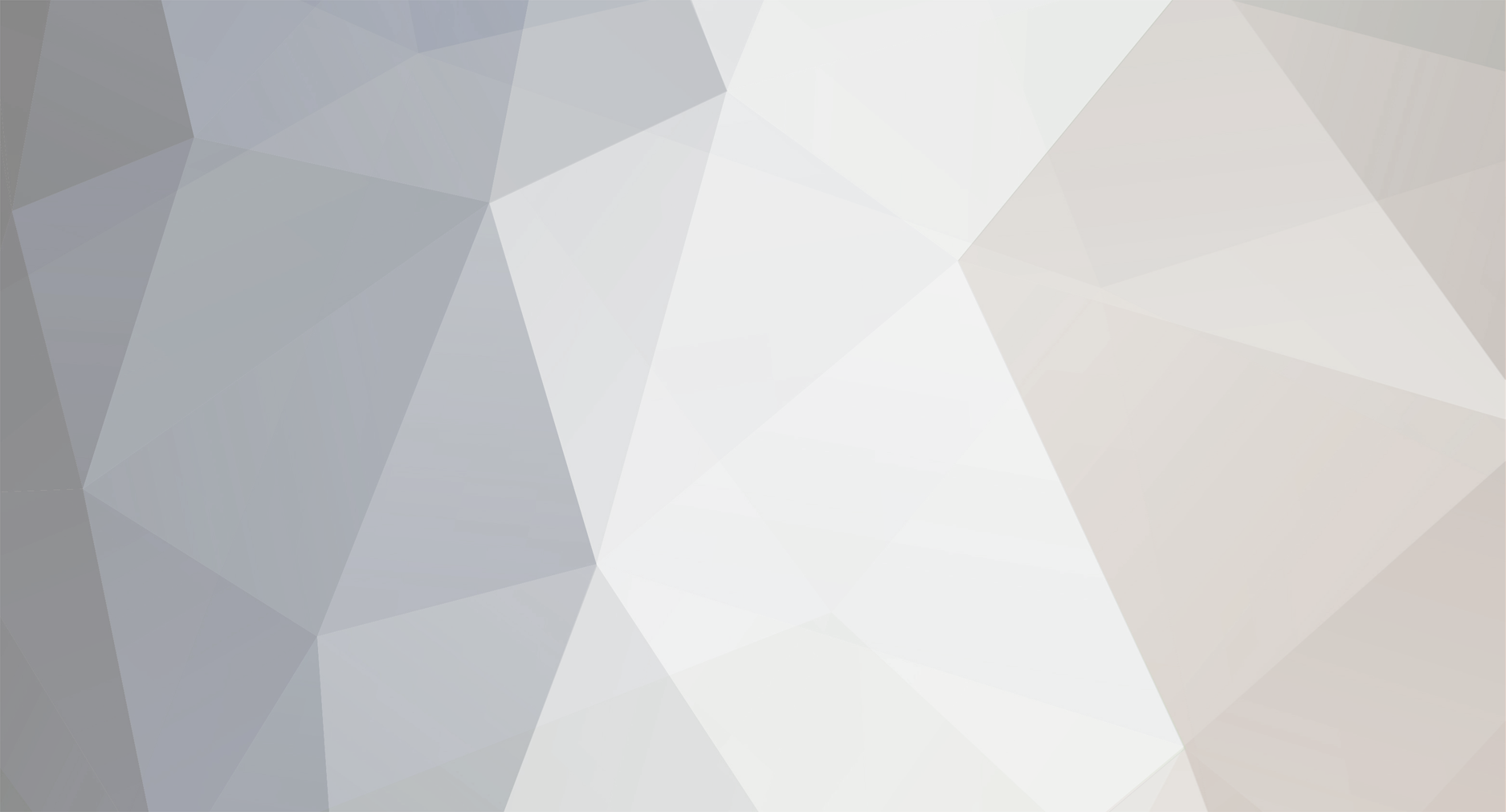
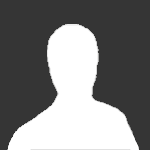
cheesegas
Member-
Posts
1,073 -
Joined
-
Last visited
Content Type
Profiles
Forums
Events
Gallery
Blogs
Store
Everything posted by cheesegas
-
Can you grab the firmware revision from the XiaoxangBMS app? I'm intrigued - it seems to be mostly with the lower firmware numbers under 30 which have the issue. I wonder if yours somehow has an old stock BMS in it! And yep, I'm fully aware of the low current sensing issue; again, this seems to be solved with the newer firmware. I suspect there's a lot of old stock BMSs around, hence keeping the warning up.
-
I think I'm going a little mad saying this... The newer Fogstars (as of 2-3 years ago) ship with the JBD BMS with a firmware version that's much improved. The SOC is only up to 5% off compared to a Victron Smartshunt/BMV, even with small discharge currents and not syncing to 100% for months. If you don't need Victron integration and you only have one battery in a simple system, the Fogstar's SOC is perfectly accurate.
-
A lot of fridges nowadays have the condenser coils under the side panels, rather than at the back. This means you need to leave at least 5cm of space on each side for air to circulate, something not many people do. If you don't, the efficiency takes a big hit. It's a bit of a waste of space on boats as you often have ample room behind, but you lose either cabinet space or fridge space depending how you look at it. This includes 12v fridges converted from 240v ones. Waeco and Dometic build 12v fridges from the ground up and tend not to do this - the condenser is exposed on the back at the top, sometimes with a fan. I'm guessing this is to reduce the chances of the condenser being damaged in transit... My 2kva Victron Multiplus happily runs a 240v fridge, as does a smaller 800w Victron Phoenix. Both are low frequency inverters though, which probably helps with the inrush current of starting the compressor. It's a lot cheaper to build a high frequency inverter so I expect your Sunshine ones are built that way. I need to replace my 12v Indel/Isotherm soon as the door seals are cracking, and I'd like a proper freezer compartment. I'll probably be going the route of a 240v fridge with freezer box (more choice than 12v!) and a 800w Victron inverter mounted in the cupboard next to it, with the remote terminals wired to the fridge's thermostat. When the thermostat closes, the inverter switches on and the fridge's compressor runs, avoiding losses from having the inverter on standby or in search mode 24/7. Yes, there's more to go wrong but if the inverter dies I can temporarily run the fridge off the main 2kva Multiplus. Doing this permanently isn't an option as the inverter is next to my bed, and it makes just enough noise to wake me up when running a 240v fridge.
-
Colour rendering index - it's basically a measure of how many frequencies of light a white bulb emits. Some only output a very narrow band of colours to approximate white, so things look a bit odd and it strains your eyes but you can't quite work out why. Here's a better explanation - https://www.waveformlighting.com/tech/what-is-cri-color-rendering-index Some manufacturers simply list the CRI as 'high', whereas better ones measure it. Here's a commonly used LED panel light in the filming/events industry, which shows the CRI: https://www.litepanels.com/en/product/astra-6x-bi-color-led-panel/ LED tape is a bit more difficult to get a high CRI - this one's just listed as above 90. https://www.ultraleds.co.uk/24v-professional-smd-series-led-tape-9-6w-p-m-128-leds-p-m-cri-90-3000k-5-metre-reel.html
-
What type of roof do you have? Gutters or bars? I've put the bottom half of a pallet across the roof bars so it doesn't contact the roof, and stapled a sheet of heavy polythene under it. 8 coal bags go on the half pallet, covered by a square tarp with a piece of elastic through the eyes, looped over hooks screwed into the pallet. The polythene catches all the coal dust so it doesn't end up on the roof, and the tarp hides the bags and also stops rain building up in the polythene. Every spring I take it off my roof and shake out the coal dust.
-
Cold welding isn't something to believe in, it's a thing - plenty of stuff on it, here's a paper from the IEEE, albeit with different metal than we use for lugs (tin plated copper) and cable (copper) on boats. https://ieeexplore.ieee.org/document/482867 It is however very possible to end up with a poor crimp if you use a cheap tool with poor tolerances, and/or a lug which hasn't been annealed or is a weird size. Soldering isn't practical for a lot of repairs on boats as you need sufficient space around the cable to avoid toasting what's behind it. This might mean undoing a cable loom, removing conduit or other time consuming and often impractical things. Given the state of most engine bays with lots of oil soaked rags around and how boats are fitted out with lots of non-fireproofed wood, I'd like to minimise the time I spend with a naked flame in my hand! The reasoning behind not soldering lugs on boats and cars is because the solder can wick down the cable past the lug, causing it to become liable to fracture with vibration. It's hard to tell how much it wicks down - much easier to get a good, reliable crimp.
-
Yep - but remember eBay are just a marketplace, it depends on the seller. I've bought some great quality branded connectors via eBay, but as you say, there's also a lot of crap on there. I can't remember which outlet it was but one of the major Bimble-ish suppliers seemed to go through a phase of crap crimp lugs, probably sourced from the same place as many of the cheaper eBay ones!
-
You need to go to a component supplier - as you say, distributors like 12v Planet will change suppliers as and when is best for them. You're right though, some seem to use a thinner walled copper tube which doesn't crimp as well. Farnell used to sell MTA ones, but they seem to not carry them any more so my next go to is Wurth. Gone off the ones with a hole in the end of the tube (to check proper insertion) as I suspect once water gets in, it wicks up the cable. You can get a nice watertight seal with glue lined heat shrink on the cable otherwise. https://uk.farnell.com/wurth-elektronik/5580516/terminal-compression-lug-m5/dp/2827747
-
Ok, that's cleared up some things...I was indeed misreading that quote. However, I'm still convinced something is wrong with either the fuse or fuse holder. I am perfectly aware of the issue with the OD, for the third time, thank you. I am trying to help here. I actually got out my electrical bits to have a look and do a little test to prove my point. Here's a photo of a Littelfuse holder and fuse, with an MTA branded 10mm2 M5 lug on one side and a 25mm2 lug on the other. Neither foul the plastic part at all. I'm confused as to how you've managed to install it in a fashion that does. Maybe I've misunderstood the issue? An M5 lug on a branded fuse holder with a branded fuse does not hit the insulation. Just the like the other 100 of these I've installed, this one does not. Perhaps you have a weird off-brand lug, where they've used the same lug for many different hole sizes so the flat bit is bigger? The reason hole sizes were of concern was that an M6 lug sometimes has bigger external dimensions than an M5, depending on the brand.
-
I know what your issue is - the lug hitting the plastic insulation of the fuse. I also know that an M6 lug will hit the insulation, but an M5 lug will not. You said below that an M5 ID lug don't fit (the stud?), so I assumed you're using an M6 lug to fit the stud. However, as mentioned above, this will hit the plastic bit of the fuse.
-
You said here that M5 ID lugs didn't fit though? Unless I misunderstood your post. That's why I assumed you're using M6 ones, which foul the plastic part of the fuse as you describe. I've fitted a lot of midi fuse holders and can say that I've never had an M5 lug not fit a Littelfuse, Durite MTA fuse holder with a standard Littelfuse fuse. I don't know what ones you're using.
-
M5 should need an 8mm socket , but given the random assortment of metric and imperial nuts used on electrical things, it wouldn't surprise me if the studs were actually imperial...UNF 10-16, which has a diameter of about 4.8mm, and the nuts are something like 9.5mm across the flats, which would mean a 10mm socket kind of fits! I do understand the issue - see below. It sounds like you're using an M6 lug with a fuse designed for an M5 stud, so the OD is an issue. If the M5 lugs don't fit, then you may have a weird fuse holder with M6 studs, in which case the fuses will be a very tight fit but they'll sort of squish onto it. Can you post a link to your fuse holder and fuse? A photo of yours would help too. This is the issue. You need an M5 lug to work with your fuse. Sounds like the fuse holder is the problem. Putting washes between the lug and fuse (or anything for that matter) is generally bad practice; with midi-fuse level of currents you'll get away with it, but you'd be surprised at the voltage drop over a washer due to the extra contact surface. Best to have the lug contacting the thing directly.
-
Midi fuses have 5.5mm holes in them, here's the specs of a Littelfuse branded one. Fuse holders therefore usually have an M5 stud, which has a nominal 5mm diameter. Here's some examples that mention M5: https://www.12voltplanet.co.uk/midi-strip-link-fuse-holder-stackable.html https://www.12voltplanet.co.uk/midi-strip-link-fuse-holder.html https://cms-pim.durite.co.uk/durite-shop/quality-core-components/wiring-accessories/fuses-fuse-holders-and-circuit/fuse-holders/midi-fuse-holder-side-stackabl/037885-fuseholder-for-midi-typ.html Lugs with an M5/5mm hole are easily available from the usual outlets, here's one on the 12v Planet site: https://www.12voltplanet.co.uk/copper-tube-terminal-6mm-max-cable.html edit: If the studs were M6, the fuse wouldn't fit. However, there is a chance that you somehow have a weird off-brand Amazon etc fuse holder with M6 studs which came with non-standard fuses with a 6mm hole in them, there is some odd stuff floating around!
-
Most midi fuse holders have terminals to fit M5 lugs, are you sure your lugs are 5mm? M6 lugs will hit the fuse as you describe. Check the product page for your fuse holder or measure the stud diameter.
-
Great! Glad we managed to help. Nothing better than a fix that costs £0.00. Ribbon cables and the IDC connectors on the Multipluses are definitely a weak point, especially if installed in an engine bay or near a door - humid, changing temperatures, lots of vibration. Boards themselves are coated in conformal goo so they’re water resistant.
-
In ve.config, do you see sensible readings for power? If so, then it'll be a comms issue between MP and GX device. Current sensor on the Multiplus Compact and older small microprocessor Multis is soldered to the vertically mounted power PCB on the right of the unit. This is connected to the main control PCB with a grey ribbon cable - @Alway Swilby if you are comfortable poking around inside, it's worth reseating it. The ribbon cable on the Compacts can get trapped between the front cover and the horizontal brace, causing it to rub through and throw up all kinds of weird errors, check for this too.
-
Testing kit arrived yesterday evening (Amazon are evil but oh so convenient!), as I'm not moored near anyone I ran the engine up this morning, then put the little demi-john airlock looking thing on the neck of the tank with the special fluid inside. A key bit of info I forgot to add was that the coolant rises a little on a cold start, and then under load it rises further. Did it twice, showed positive for combustion gases, I'll get a leakdown test done too however just to be sure. Looks like Engines Plus might be making me a little bit poorer with the most expensive head gasket possible! Thanks @Tony Brooks for the recommendation of the combustion gas test kit!
-
Check the policy docs carefully when you get them, there's a cooling-off period of 14 days (I think!) where you can make changes. I recently renewed my insurance with a new broker, and I asked them for contents insurance - they gave me a price in an email. However, when I agreed to the price and they sent through the documentation after I'd paid, it turned out they'd forgotten to add it on after all... If I'd had a break in or fire etc, contents wouldn't have been covered! I also asked them about the issue of accidentally double-insuring my tools, as they had a non-contribution escape clause for this. My public liability insurance for work (self employed) covers tool and laptop theft from on site, in transit to/from site and from a hotel room. However, this policy also covers theft from home, ie. a fixed address...I made sure to check that the PLI policy excluded my boat from cover as it wasn't a fixed address. Another insurance fun thing is that I'm covered by two separate insurers - one for temporary electrics and video installations on temporary events, and another for marine electrics. I recently did a job which involved a couple of 40kva sets craned on to a massive yacht to supply power for a birthday party. Involved a bit of boat work to bond the earths, but it was a temporary event! Again, phone call to check... I think this is a bit of a silly comment. You would be very surprised as to how many people of the 50-60 year old generation also have no idea how to sort themselves out; in my opinion, it's a universal thing, perhaps influenced by upbringing, rather than generational. As someone who looks a bit younger than I actually am, I frequently get patronised by older gents who assume I don't know what I'm doing around practical things which is rather annoying. This unfortunately extends to work too, where I often have people of varying ages working under me as a team. Rarely is there a problem, but I occasionally get a guy 20 years older than me trying to take charge, telling me what to do and how I'm doing it is wrong...when it's the industry practice. This often ends very poorly for them as I pop in a quick phone call to my client who's hired me, recommending not to hire that person again.
-
That's a screenshot from VRM, the online portal. As it's showing the rest of the data fine, there's no reason why it would simply miss out a bit of the data going from boat to Victon's servers, and show the rest correctly. This sounds like a comms error between the Cerbo and the Multiplus. Has anything been changed in the system recently? On a laptop/phone connected to the boat's wifi, can you put in Venus.local into a web browser and get to the Cerbo's config page? From there, you can click Devices and then your Multiplus. If it's not there, that's your issue.
-
The pressure cap that's leaking is the one on the remote expansion bottle. The exhaust manifold is air cooled, there's no coolant tank around the stubs and the only cap on the system is on the expansion bottle. It's a pre-HMI-blue Isuzu so as far as I can tell, the only marinising that's been done to the industrial base engine is an oil change pump and a heavier flywheel, unlike the HMI Isuzus which have a water cooled exhaust manifold.
-
Will do. The only reason I was going to change the coolant is that I faintly remember rushing the filling process last time for some reason - the vent line from the T piece is only 6mm hose so it may have not have let the air out fast enough in hindsight. I think have a piece of clear hose so I'll put that in after doing the test. Thanks!
-
Ah that's my bad wording - there's no vent, manual or automatic on the skin tank, but at the highest point of the skin tank inlet (which is at the top of the tank) there's a T piece which vents into the expansion tank. This makes it self venting I guess. Yep, the highest hose on the skin tank goes up at a 20 degree ish angle with no bends, straight into the thermostat housing. Just before it gets into the thermostat housing, there's a T piece with the T facing up that vents into the expansion tank. There's no calorifier. The skin tank is large enough, it's the entire height and length of the swim plate, and I've run the engine at full power for a long time on the lower Thames quite a few times with no overheating issues. The pipework is exactly as it should be, perhaps with less bends in the skin tank top hose as it used to sag between the tank and engine. Alternator belt is tight and I've had the water pump out last year to change the seals and bearings, the impeller's not corroded. The temperature is the same as always. It doesn't have a temperature gauge, only a warning light, so I take it with an infrared thermometer aimed at the top hose - 85 degrees C. When running at lower revs, the thermostat cycles open and closed. I didn't know that was a test for exhaust in coolant, thanks! I'll do that, easier than a leak down test. First I'll change the coolant and fill it very slowly. I've always done it in the same way however, via the tank, making sure that the vent spigot on the tank is clear. The system takes around 40 litres of coolant so it's not cheap!