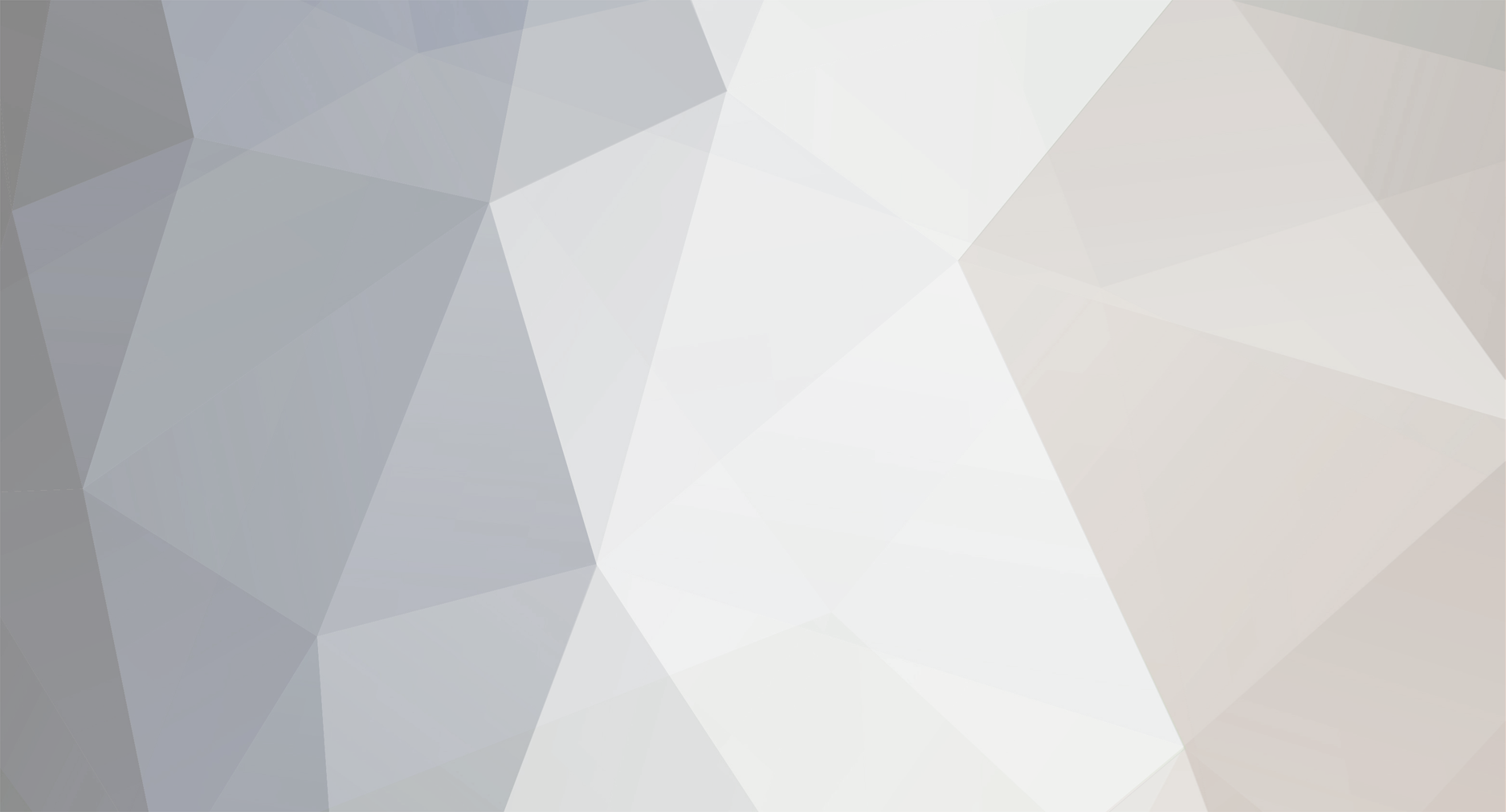
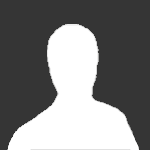
Mikexx
Member-
Posts
541 -
Joined
-
Last visited
Content Type
Profiles
Forums
Events
Gallery
Blogs
Store
Everything posted by Mikexx
-
The last one I undid was definitely a RH thread. I used a substantial 3/4" socket set to undo the nut and it wasn't too difficult. I'm wondering how much force you placed on the stilsons? Would this be your bodyweight as in standing or much less? How are you locking the crankshaft?
-
Hong Kong for £7.14 including postage http://www.ebay.co.uk/itm/High-Quality-Automatic-Digital-Laser-Photo-Tachometer-NonContact-RPM-Tach-Tester-/131320109646 or the item I've just purchased for £8.29 including postage: http://www.ebay.co.uk/itm/Digital-LCD-Laser-Photo-Tachometer-RPM-Tachometer-Non-Contact-Measuring-Tool-C3-/222078995586 Impressive value for money. Before I saw your post I was starting to wonder how I might glue a magnet to the flywheel as per: http://www.canalworld.net/forums/index.php?showtopic=6647
-
Thanks for the heads up to the source. Just bought one as I don't trust my current tacho. There are other sellers for the same item that are cheaper in the UK, or cheaper still if you don't mind waiting for delivery from China!
-
The plans for this development plans were drawn up in 2008. With Alvechurch Marina being so close and some housing on the doorstep, I suspect there were a number of objections to the project. Perhaps the council will know?
-
When the pump was fitted to the engine, was the anti-stall device adjusted? As Tony has said the combination of a maladjusted anti-stall device and the tickover stop set too low would cause erratic idling. The procedure I followed was to set the tickover by the "throttle" stop and adjust the anti-stall bolt until it affected tickover and unscrewed 2 flats. There is a more elaborate method as per: http://www.asap-supplies.com/media/faq/131000-bmc-1.5-manual.pdf on page 6 / M3
-
Without intending to appear anal, the SKF variety you have is Speedi Sleeve. I spent a while googling speed sleeve and got few hits. Just in case the photos disappear from this site, for reference, your part no. is SKF 99156. The idea of hammering this on, even with the tool, frightens me a little! I have a flypress and much prefer to apply pressure uniformly over the tool and perhaps slide the sleeve in one go.
-
Thanks for that bit of info. I'm sure at the time I had phoned Calcutt some years ago or similar establishment and they advised against mixing the two. I might have misunderstood the details I was told. I found your repair of the pulley interesting to follow. How much was the Speed Sleeve?
-
Starter motor pinion throw adjustment (and other issues)
Mikexx replied to David Mutch's topic in BMC
8V is far too much. You need to find where this voltage is being dropped. I would first check the voltage across the starter switch when operated. Then look between the switch and the terminal on the starter. Unless you have the flimsiest wire ever, I would expect the switch to be faulty or a bad connection. They can usually be found by touch, by burning you as soon as you have found that high resistance connection. -
There are a few MGB B series pulleys there, but are these the same as the BMC diesel? I was also told the 1.5 is different from the 1.8?
-
My apologies I should have considered that bleed screws would be hollow and cross-drilled. The problem I have is that the banjos of 8mm internal diameter won't fit over the thread of a M10, or 7/16" UNF thread?
-
It is a banjo bolt without any "banjos". https://www.dropbox.com/s/y3k3l1o485b1stu/2016-08-08-2080.jpg?dl=0 Sorry its so out of focus. Where do the leak-off pipes normally go? In an earlier post you said they should both be connected, by means of an extended [long] banjo bolt with a small centre drilling [to restrict bleed back volume] into the boss adjacent to the centre bolt on top of the filter head into which someone has fitted a blanking plug. The current bolt is M10 x 1.5mm, the thread in the CAV housing seems larger and possibly has a finer thread, and the leak-off banjos etc have an 8mm internal diameter. Sorry, but getting confused!
-
One bit at a time! Put the fuel pipes the right way round on the filter housing and changed the filter. After a week of being unused it started first time. Added throttle stops for tick-over and max revs. Slackened the anti-stall device as per book, two flats from when the tick-over is affected. However I don't have a means of measuring engine speed and I don't trust the tachometer as it reads very low. The engine now has a solid tick-over, doesn't race on idle and doesn't die when you put it into gear. In fact, apart from the gearbox, bearing and hint of water flowing over the propeller, you hardly hear the engine note drop . It feels so different! I haven't touched the leak-off and return pipework - yet. However in my exuberance I nipped up the banjo bolt (that should have the leak-off pipes etc) and stripped the thread. It was already very loose and I should have taken more care in anticipation. I've been looking at thread sizes, is it possible this thread in the filter body is a 7/16" - 20 UNF, which might be sufficient to catch the "4" threads of a M10 banjo bolt? The Banjo bolt is an M10 x 1.5mm with just 4 threads. I measured it's major diameter and got 9.8mm. The filter body is a CAV 5836B020 but apart from having 1/2" - 20 UNF unions I can't see any info in the banjo thread. However the (female) banjos in the leak-off and return pipes have an 8mm internal diameter whereas the banjo bolt on the CAV filter is larger! I presume I have the wrong filter housing? Many thanks for all your help.
-
I have a boat that needs work but no need to take out of the water. Can anyone suggest anywhere not far from the Worcester / Bromsgrove area where I could carry out this work. I would also need a longer term mooring but not intended for live-aboard, more a base to cruise from. Ideas anyone that are not too expensive? Many thanks.
-
Thanks for the info. Yes I had assumed it was to adjust the idle speed! The link I gave the OP is for the 1.5 and I can't find the adjustment process. However: http://www.asap-supplies.com/media/faq/132000-bmc-1.8-manual.pdf for the 1.8 which of course is similar does cover this procedure.
-
First of all do you mean this manual: https://www.asap-supplies.com/media/BMC_Manuals/131000-BMC-1.5-Manual.pdf There are a few different ones in circulation. What do you mean by "injection pump driving gear"? I would normally expect that to be embedded well inside the engine, in contact with the camshaft. I'm wondering if you actually mean the air intake. This is where a picture paints a 1,000 words. Can you post a photo or two. I use dropbox which can provide you with a handy link to share.
-
Hmm - yes it does have a ring to it! Trouble is I have 100 ltrs of fuel in the tank after "part" filling it up!
-
I've not seen a broken valve. The ones I have seen where pistons have hit valves have been bent and a big dent in the pistons. On a push-rodded-vave diesel engine where the valves are vertical I have only seen bent push rods and broken rockers. While a belt, and not chain, the only time I have suffered a failure is when trying to start the engine. I just hope you are lucky and the damaged localised to camshaft and valve-gear.
-
I wasn't aware those holes around the throttle spindle were designed for stops. I'll measure the thread size and get some bolts/nuts. Also rotate the lever as you've intimated. The cable might then also fit better. I thought idle was set by the bolt/locknut on top? Same for measuring the banjo bolt etc. There is no return to the tank and doesn't look as if there has ever been one. The bleed-off currently goes to the "sedimentary" filter which feeds the "paper" filter. I'm uncertain of the benefit, part from being currently wrong, of recirculating the fuel in just the paper fuel filter? I am also wondering if the current arrangement of feed/return points are at levels within the filter housing that encourage air to enter. Just read the "Still no joy" thread. Thanks for your invaluable help.
-
The boat has been used as a live-aboard by a member of the family for a number of years. I haven't been on the boat for a few years. I know they has used a generator for a while rather than using the engine to charge the batteries. They're also shot and the second alternator has bearing issues! One issue is where to get a banjo bolt from. I'm not at the boat for a few days and don't know the likely thread size etc. I assume imperial from the sizes of the nuts. It looks like someone has used a plain bolt on the filter body! Many thanks for all the help. I added the photo to confirm the fuel direction after your posts as I had assumed the connections were correct. I shall be at the boat this w/e and hope to be in a position to at least swap over the pipes.
-
Did the engine boil, if not then as you suggest the water pump belt was still intact. Being a 1.8 I'm assuming that the pump drive is independent of camshaft drive, forgive me if I'm wrong. Two things: 1) Lift the oil filler cap off. When cranking can you see valves moving? 2) If they are moving, I would crack open all the injectors to make sure you properly prime the HP side. Just opening one can give the impression all is well where air is still present.
-
I'm waiting for the spanner to turn up before dismantling the transfer pump innards. I can confirm that after standing for 2 weeks the engine started and despite maintaining full throttle died and had to be re-bled. For info: https://www.dropbox.com/s/7n2d67zhujudvv0/2016-07-25-2051.jpg?dl=0 Having little knowledge of these pumps, I wasn't initially aware of which filter input/output should be attached to which end of the pump. Something tells me these have been fitted the wrong way round. The injector leak-off pipe is routed back to the sedimentary "filter". A little diesel does leak out between the nut and bolt threads, perhaps expectedly. I have a domed nut than should solve that issue with a coper washer. I don't think ingress of air here would cause the symptoms I'm getting. I've felt around the pump end plate area and after the engine has been running for a while it stays dry which surprises me if air is getting in. Will advise again when I've undone the big "nut"!
-
Many thanks for the help. Two things, first that many of the union nuts have been rounded, such I was considering getting a 1/2" flare nut (hex) spanner. Second, the engine runs fine and I don't get any impression of fuel starvation. Is this really likely to be the culprit? I have now found some manuals for the pump, thanks.
-
When you say "transfer pump" I presume you mean the cam operated fuel pump? This pump is brand new, though the fuel level in the tank is such that this pump is near redundant. The engine runs well when going so don't have the impression of fuel starvation. The sedimentary filter body and fuel filters have both been cleaned / changed. Many thanks for your reply.
-
This has happened a couple of times, where the engine has started seemingly ok. If I move the throttle back to reduce revs the engine then dies. It won't then restart even with 20secs of glow-plug heat before trying. If I bleed the High Pressure side a few times it then start, with a lot of relief on my part! Any ideas? I'm wondering if air gets in somewhere into the pump after I've turned the fuel tap off as things cool down and contract as a consequence? Long shot I know!
-
I agree with all of this. If the engine sounds ok in other respects I would tend to leave alone. The only thing I might do would be to check compression if there is any difficulty in starting assuming glow plugs and fuel side are all good. Excessive blow-by is an indication but not an exhaustive one.