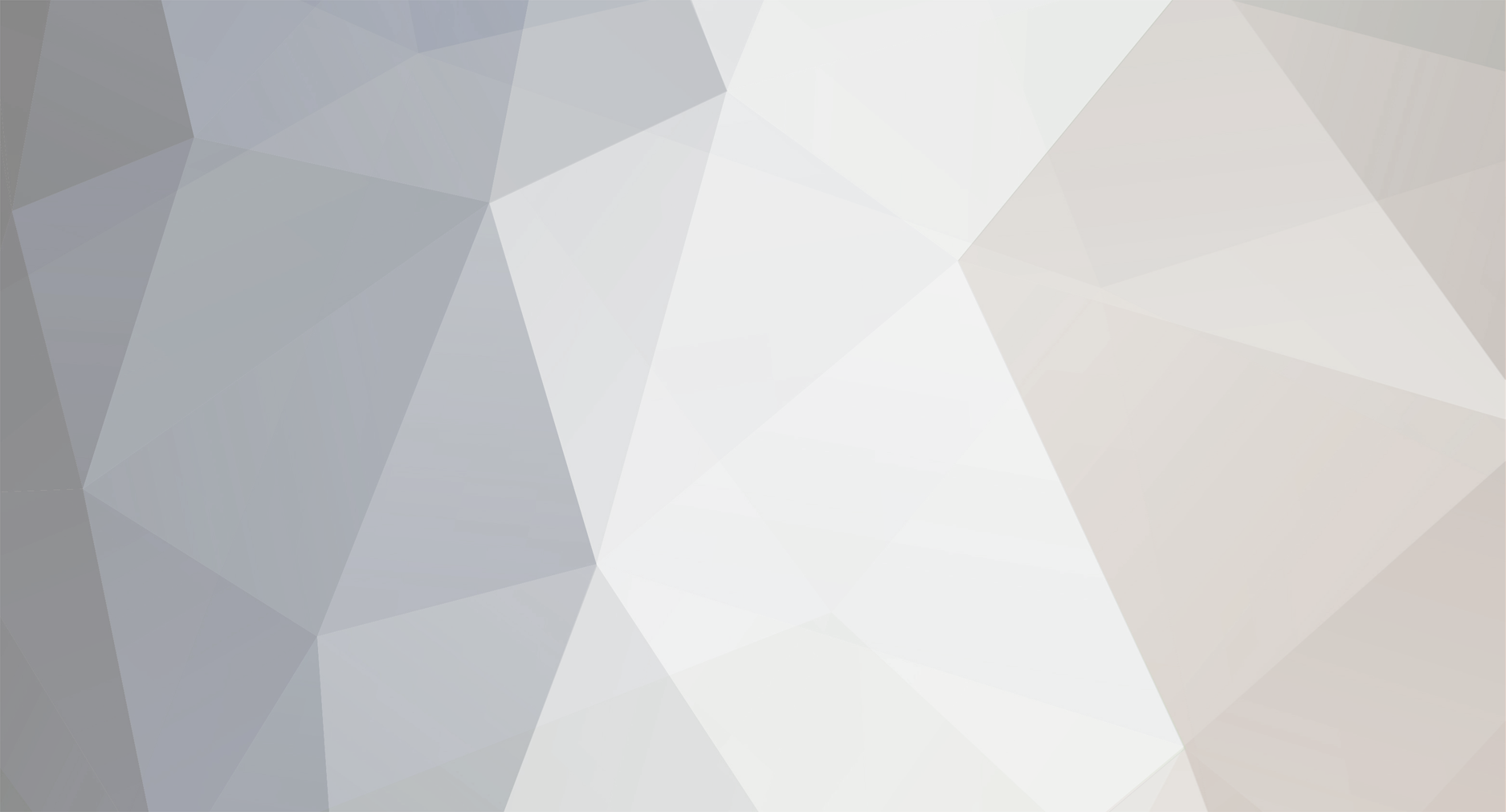
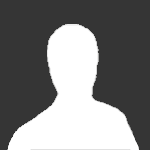
TandC
Member-
Posts
477 -
Joined
-
Last visited
Content Type
Profiles
Forums
Events
Gallery
Blogs
Store
Everything posted by TandC
-
Well, that's why we are getting a new boat built: https://www.oxfordmail.co.uk/news/21402667.devastated-couple-lost-everything-houseboat-trashed-weir-opened/
-
Exactly! That was the other consideration - is it going to be possible to remove it if and when it goes belly up!
-
Thanks - I was thinking about that as part of hte pros/cons. We live onboard all year so aside from holidays away we have a year-round requirement for hot water etc. We're also on the river with a high flow rate during the winter - so much so that we are stuck on the mooring for 5 months of the year. That water flow does help keep temperatures up - I've never seen the river freeze. We also have mains power, so I would in the worst case if we were away during winter I could just stick a heater in the engine bay to keep freeze risk off. As you say, that seems to be very much outweighed by the space saving in the cabin and also the ease of dealing with any leaks. That said - im now realising that installing the calorifier in the engine bay, and worst case having to replace it, will be a total bugger of a job working under a cruiser stern, alongside the engine etc....
-
I see thanks. I have always just had service valves at the pump and also at tank so I can isolate to allow me to remove the pump. But I do see there is a little more risk there with a bottom-mounted supply from the tank.
-
Thanks 4-50; is your second point referring to the water pump above the main water tank, take off in the top of the tank? When you say "deliberately" - why? I was imagining that the water tank would generate a degree of its own pressure - perhaps as Jen suggested use 22mm supply pipe to give a really positive flow rate into a pump which would be BELOW the tank level. I'm not sure I understand why you would have it above?
-
Thanks Tony, I was thinking more a vertical one, but you help reinforce the point that I need to speak to the boat builder about both the available space alongside the engine, and suitable fixing points being built in now. As the engine will have a sound enclosure, I shall need to check how much space is left and also the orientation/routing of any pipework out of that enclosure to inform the placement of the calorifier. I was thinking then that the battery bank could be located on the opposing side, which would help in balancing out the weight. Last question: Stainless steel calorifier..... is that a better option than copper? Any recommendations for high-quality suppliers? i prefer to get this right with good quality component not cut corners on price.
-
Thanks Jen, that's helpful. I can run the cold supply from the bow, through the bathroom at the rear, expansion vessel in the bathroom cupboard, through the bulkhead and into the calorifier. My priority is to work out our window placement - which means fixing the size of our layout - which means fixing the size of the bathroom - which means fixing does it need the space for a calorifier or not! annnnnd BREATHE.... I will try to work out now how much room there will be alongside the engine and whether there is room to fit a vertical calorifier, and how it is secured. There will be a Beta50 inside a sound-proofing enclosure, so I'm hoping there's room alongside that up against the bulkhead for fitting. For anyone with a calorifier in the engine bay - how is secured? Would I need some studs on the baseplate to bolt it down on? a dedicated plate fabricating in for it to stand on?
-
Great this is all helpful. On water heating options - currently we have a Morco which i love for its bomb-proof simplicity, but it's so weary trying to get anyone to ever service it safe etc. A boiler also takes up room and it doesn't help with heating. So i've made the decision that we take the plunge and do away with gas boiler now. Instead, we are planning on a Webasto/Eber for hot water and central heating, and then a Squirrel stove without a back boiler. We are also on mains hookup and for the majority of winter and so have the option of an immersion for hot water. I'm not sure what is more expensive now - a diesel heater or heating a large tank with an immersion.... I guess if the Webasto fails, we have the option of lighting the fire to keep warm and using the immersion to heat water. With regard the layout, having done our layout plan as best we can, the bathroom will be as Mr Smelly described - down the steps from rear deck, orientated to the left hand side. Immediately on the right will be the bathroom, and then beyond that the kitchen also orientated on the right so this puts all the hot water requirements as close as can be. On the calorifier - I would ideally like it in the engine bay because I really want to max out the space inside the cabin, it seems crazy to put a big water tank inside that precious area if it could go in the engine bay which will be large. I can see the pros of it being inside a cupboard in the bathroom - heat loss is coming inside, create an airing cupboard. But it feels outweighed by the cons of space taken up, and i am a bit nervous about the potential to have it leaking inside the cabin - is it not a little safer for it to be in the engine bay? @MrSmelly - is yours vertical or horizontal in the engine bay, and what size is it? I know that 55lts is currently not enough for two of us living onboard so want to go larger. If you don't mind I will PM you perhaps for a picture or two if you could? How is the calorifier fitted and secured in the engine bay? I'm thinking I need to speak to the builder about this now so that fitting points etc can be fabricated in as they construct, in the right places to allow for efficient plumbing runs off the engine etc. On the expansion vessel - how far away from the calorifier can it be? I could live with it coming inside into the bathroom cupboards.... maybe easier to get it secured, plumbed near to the main water pump and its accumalator. Another thought - the water tank is in the bow so the supply would run down the length of the boat. I would like to avoid having the pump in the bedroom, preferable to have it in the kitchen or even better the bathroom. I dont think that would be a problem would it, running that supply by just its own pressure down to the pump say some 35ish feet away? I;ll stop now! Thanks again for any thoughts
-
The first of what will be a barrage of questions associated with the fit of our new build 45 x 10. We need to make some rapid decisions on the layout options to inform window placement... and a key one is where the calorifier will be installed. Our current 55lt calorifier is just too small - so we were looking at 100lt and ideally, to fit in the engine bay (cruiser stern). I need to speak to the builder for their advice but was interested in other's views please. Even at 10ft wide, I am not sure if it will fit vertically alongside the engine with its enclosure - but then Im also not sure such a large calorifier would go horizontaly. Any thoughts? I really don't want it inside if it can be avoided - valuable space on a short boat, plus some concerns over if it leaks.
-
Yes! silly me... thanks
-
I've had to strip all the 12v out following a sinking and now replacing. Problem is that I've now lost the original wiring diagram and much of the original cabling/fuseholders have been binned in the clean up operation. I'm trying to work out the right approach / not sure what was previously done was correct, particularly with the fusing arrangements so grateful for any assistance. The alternator output is to the main isolator switch - there is a split charge relay (not VSR) - no fuse in this arrangement. Then three main power devices: Solar charger 40amp EP Tracer - 16mm2 cable output to the domestic bank - the manual states a fuse sized 1.25 to 2 times the rated output of the controller. As such, was going to use a 60amp blade fuse. ProDigital 50amp charger - two positive outlets - one to the domestic bank and one to the starter battery. Done in 25mm2 cable as recommended by the manual and the distance from charger to battery is around 1m - 1.5m. Each charger bank outlet went straight into a Megafuse holder with a 60amp mega fuse. Sterling ProPower Q 1000w inverter - the manual states a 200amp fuse to be used - it appears that the input from the battery bank to the inverter was first connected to a megafuse holder with a 200amp fuse, with the cabling on to the inverter unit in 16mm2 and less than 2m cable run. Does this seem about right? Grateful for any advice.
-
Fuel hose thread size - anyone able to confirm?
TandC replied to TandC's topic in Boat Building & Maintenance
Ah sorry - not sure why the pic isn't showing. I shall get back out there with the vernier gauge -
Hello all, I'm trying to identify the thread size of this fitting which is the diesel return from the engine, this fitting screws into a fitting brazed onto my diesel tank to return unused fuel. Is that a 1/2" BSP? I am ordering a replacement diesel tank to be constructed and need the corresponding fitting built in. Any wisdom? It's a Vetus fuel line, fitted on a Lister SR2 Thanks
-
Morning all, Im looking at installing diesel heating for domestic hot water and heating on a 45x10ft new build, but know little of the competing systems nor the considerations around system design. I've read various posts around their troublesome nature if not run for particular times, at particular capacities. Being totally in the dark, I was keen to have a conversation with both a supplier so that I can get an understanding of options and costs, but also some guidance on system design. What are the considerations for number radiators/heating capacity etc... etc If anyone has had good experience of firms who can provide that advice I'd be grateful for recommendations. Thanks Tim
-
Flexible plumbing connectors - a bodge waiting for accidents?
TandC replied to TandC's topic in Boat Building & Maintenance
Okay - this is reassuring (I mean, the braided that I had previously used were fine after best part of 15 years). I've no calorifier. I had originally used one 500mm braided flexy to come from the cold water tank outlet, running from the outlet on the top of the tank into a shut-off tap then down to the main supply line running at floor height. That I may try to redo in hard speedfit fittings if it's not too difficult. And then there is one other in the line running from the Morco hot feed to the shower, about half way along as it transitions the buklhead/floor and back up to the back of the shower. It's vaguely accessible to check in the future.... ish. I've used WRAS approved JG SPeedfit ones so would hope these will all be fine. -
I've previously used flexible plumbing connectors - the stainless steel braided tap connector types - and over 15 years have had no problems. Currently refitting some plumbing and I happened across advice online that these should be considered only to have a 5 year lifespan and in worst case were described as "an accident waiting to happen". What's the general consensus? I was thinking of using a fleixble to help negotiate a tricky transition between floor and wall to feed the shower - thinking it would minimise the number of elbow joints etc required, fewer points to leak. But is that considered a sub-standard approach and I should instead make the transition using multiple elbows/short sections of tube etc. Using JG Speedfit fittings, new JG pipe, JG superseal inserts, cutting pipe clean and square with new cutters etc etc etc - and was considering using the JG Speedfit flexible connector, which has their 15mm connector each end. Is this a bit of scaremongering or are these flexible fittings really not suitable for a long-term installation? This is the connector I was looking at: https://www.toolstation.com/jg-speedfit-flexi-tap-connector/p46645?utm_source=googleshopping&utm_medium=feed&utm_campaign=googleshoppingfeed&mkwid=_dc&pcrid=558023894541&pkw=&pmt=&gclid=CjwKCAjw2rmWBhB4EiwAiJ0mtX3BpbbKx-wN08eTFklgz9k53MDaUhik0I_JWQcWYV6KYdPhkjS3_BoCwjEQAvD_BwE&gclsrc=aw.ds
-
Anyone had recent good experiences with a sprayfoam installer? Looking for someone who can be mobile, travelling to Oxfordshire. Appreciate any recommendations.
-
Just wanted to make a public recommendation and huge thanks to the team at River Canal Rescue and Richard of Primrose Engineering who attended the sinking of our narrowboat/home this week. Incredible response saw Tom of RCR attend on the night of her sinking to help the fire service, then a team attend within 48hrs and had her up, minimising the damage. Meanwhile Richard of Primrose was there within 48hrs to first aid rescue the Lister SR2. Within just 3 hours of tender tinkering she was firing on all cylinders (well, two). More importantly was their advice and reassurance that we were doing the right things and that it wasnt as hopeless as it feels when you see everything you own and your home covered in sludge and soggy cat biscuits. I'll avoid discussing the detail as it's likely to become a legal matter, but our 43ft cruiser ended up on the bottom of a Thames stream here in Oxford, together with another boat. Some how the water levels dropped over 1.5m in an hour, tilting boats on their moorings and those unlucky to be over slanting river bed or air cooled vents like ours went down but didn't come up.... It's an horrendous situation but with a quality insurance policy in place and quality support companies such as RCR and Primrose at least these situations can be managed well. A huge thanks again, should they be on here. Tim
- 1 reply
-
- 12
-
-
Thanks - sort of, but not really - I tend to remove all the deck boards (x3, which sit on top of 4 channels running lengthways: One under far left edge, middle left, middle right, far right edge). With no deckboards, when doing maintenance etc - I do frequently step on the two in the middle sections and it isn't really doable to avoid that. I'm not 15 stone yet! But, still feels a bit "bouncy"... could swap the two at the edges as they don't get walked on directly without deckboards and just clean up and retain the two central steel ones. This saves a bit of work, saves a bit of unnecessary weight, and I can report back in 26 years on the corrosion!
-
Pleased to report that Lancashire Rotating Electricals LTD did a top job on my starter motor - refurbishment was £180 with postage, but replaced the solenoid, the pinion gear and gave it a general tidy up. All reinstalled and while I've not had time to really test it, she started up fine and dandy. Thanks for the suggestions and assistance, and a thumbs up to LRE for their service.
-
I need to remove and refurbish the steel channel sections which support my deckboards and which currently provide a less-than-ideal drainage arrangement. I have the option of some aluminium U-section channel which is the same dimension as the steel - measuring 3" (76mm) wide x 1.5" (38mm) deep 1/4" (6mm thick). I don't have any further detail on what sort of grade it is so let's assume it is nothing special (not architectural grade or wotnot) The deckboards sit on those four channels, each channel is 63" (1.6m) long, supported each end in steel sockets. They are supposed to drain rainwater, so are orientated with the open side to the channel upwards. There are two load scenarios - the first is with the deckboards down, spreading weight across those four channels (plus some support at the ends) The second is a simple standing weight on one of those channels when the deckboards are up, to access the engine. Potentially that could be my full weight on one foot in the centre (weakest unspported point) of the channel. I have found various deflection tables online but they are totally baffling so I was after any experience/common sense response around this as an idea.... too weak? strong enough? If i had the channel in hand I would be able to do my own engineering test (i.e. stick it on a couple of blocks at the right measurements and stand on it a bit) - but i don't and i wanted a sense of whether it would be strong enough before going to get it.... any ideas?
-
Ah well that requires a feat of considerable flexibility and three elbows🙃. I shall certainly have a go at it but it's so constrained what with the drainage / deck joist steels and battery boxes. I can work on some stretches while waiting for the motor!