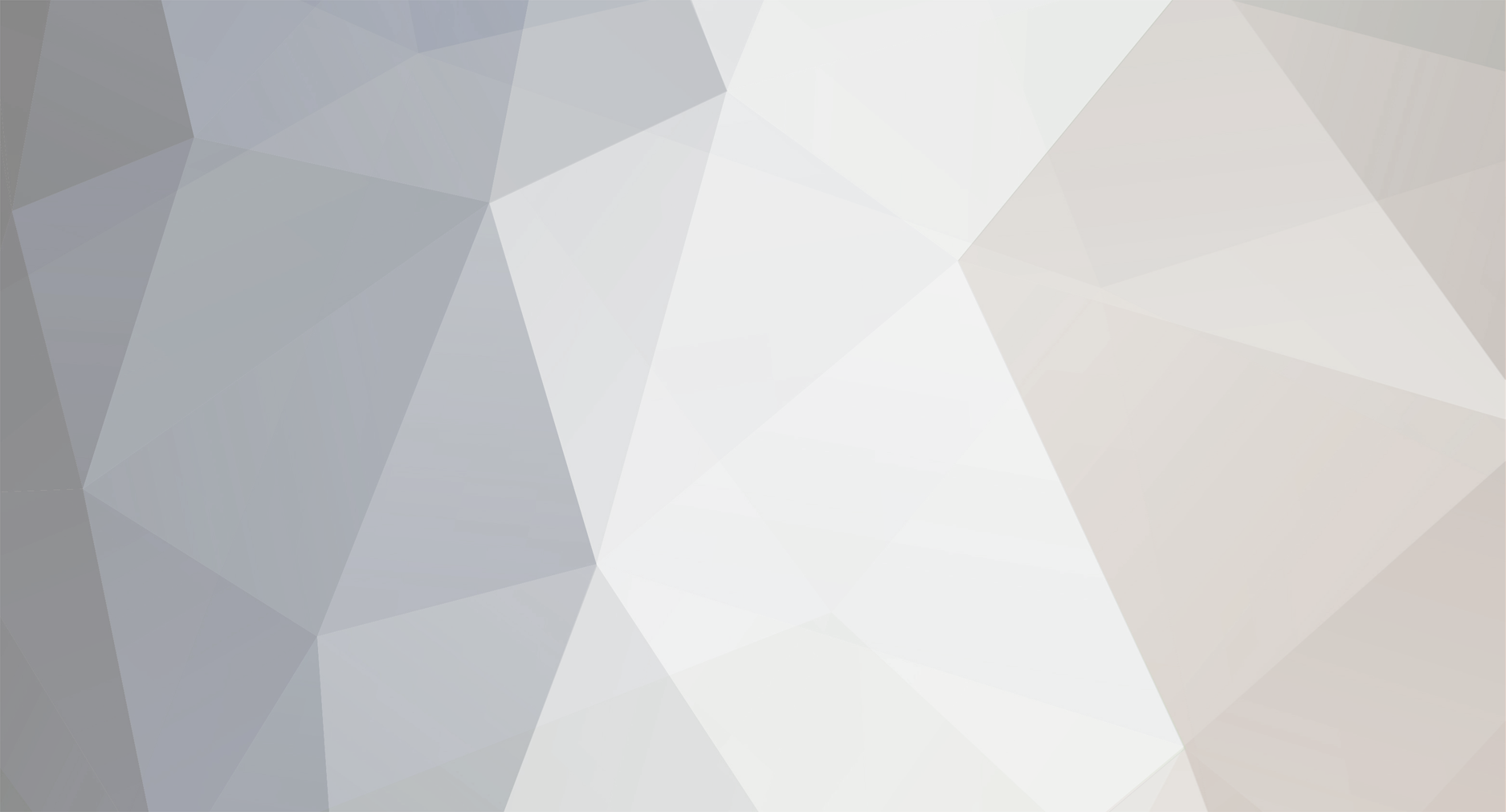
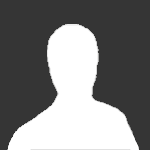
simonk
Member-
Posts
142 -
Joined
-
Last visited
Content Type
Profiles
Forums
Events
Gallery
Blogs
Store
Everything posted by simonk
-
You mean because you don't have to refill at awkward times or because it would run withoutout using any fuel ?
-
I very nearly considered getting a Honda EU20 with the lpg conversion already fitted, but it was about 200 pounds more expensive (about £1100) so I got a standard petrol one. I have to admit I am a bit scared of pouring petrol around so bottles of lpg do seem a bit safer to me. I suppose the good thing about petrol ones is that if you accidentally (or on purpose) leave it running it will stop when the fuel runs out at some point.
-
Just thinking aloud what would happen if the battery isolator was accidentally knocked or switched off in the middle of charging...? Or the power got cut off and you didn't want to overcharge the batteries by going through a full acceptance cycle again? I definitely do not intend running the petrol gen on the boat. It's going to stay on the bank (unless I go somwhere, when I suppose I could run it dry and then put it on the back deck). What do people realistically do about storing petrol? In the gas locker, on the bank, on the back deck?? I once saw someone having a BBQ on their front deck (it was a widebeam though ).
-
Thanks for that - according to the Centaur manual, the 24V 40 amp version takes a mavimum of 6 A from the mains input, which the Honda I would hope (for that price!) could handle easily. The next size up is the 60 amp which draws up to 9a, which is too much. For this reason, I'm guessing that the 40 amp would be better for me than the 30 amp, since the generator will then be working nearer maximum capacity (= more efficient, faster charging??). I think the absoption stage is fixed at 4 hours and not user-settable unlike the phoenix. The 40 amp is quite a bit larger and heavier than the 30 amp, but could probably squeeze it in where I want it with some work, as long as the cable exit is 'included' in the quoted size. Another thing is that I hope it works with the 'eco throttle' of the honda - I've heard that you need to use some software settings to make the phoenix chargers work properly, but no-one has mentioned anything about the centaur. Also, what if, at a later date, I connect it to a more restricted supply, say 5A in a marina. Will it just reduce the output or could it trip the shore supply? Hmm.... sorry for the verbal diarrhoea, my mind always works in overclocked mode when it come to these things. PS - Anyone heard anything good/bad about the Mastervolt Chargemaster chargers? What happens when you run a charger like this with the batteries disconnected - will it try to put 40 amps through all your appliances?!?
-
Aha, I was wondering why the brass grille below the vent over our bed had a load of kitchen towel sandwiched in it... Now I know why I should leave it where it is (for the moment, until someone has suggested the best answer on here)....
-
Aren't second-hand liveaboard boats fun? After a couple of months, we finally arrived at our mooring the other week. Until then, we'd been charging the batteries from the engine whilst cruising, which has been fine, but clearly, on a permanant mooring not really ideal (though good for backup) - highlighted by the engine faling to start earlier without half an hour of manual fuel-pumping persuasion... (though maybe it needs looking at properly). The boat is 24V with up to 440 Ah (8 batteries), though I may reduce this to 6 batteries (330 Ah at 24V) when the time comes to replace the whole lot. Either way, I am almost definitely getting a Honda EU20i for its quietness and reliability, but what charger? Sterling I don't like (unless anyone can persuade me otherwise) so it looks like the best option will be Victron Centaur 24/30 or 24/40 - the 40 amp version is about 570 quid as opposed to 420 for the 30 amp. Is it worth it for the 40 amp and will my EU20 cope (my calc is that it will (1600W cont. would provide the 6 amp input to the charger OK) but wondered if anyone has this setup going). Or should I go for the Victron Phoenix 24/25, it has a lower output obviously and I would have to buy the control panel too but are there ANY advantages at all over the Centaur or is it just marketing bullshit? I suspect it might be, especially since this adaptive 4 stage stuff probably isn't relevant to generator charging. What do you all think? Which one? Or convince me to go for a different make? Thanks, Simon.
-
I had another look at the thing today, this time being careful to limit the field current through an appropriately large resistor. Luckily, it appears that I haven't completely dicked the control box as it still produces a 230V output. I reckon there's a good chance of repairing it fairly easily if I can work out how the field control circuitry works (a job for tomorow...)
-
Apparently not, though there isn't anyone moored near there and it's not very accessible.
-
Was going to go from Bath to Hanham today but the plan was thwarted by a tree fallen across the lock cut just upstream of lock 6 in Bath. Should be cleared by monday or tuesday apparently...
-
Had a look at the dynawatt website, if only Sterling products came with instructions like that... I had a go at more diagnosis of the problem this evening, connected 12V across what I assumed to be the field rotor connections and ran the engine as suggested by Gibbo. This confirmed that the alternator itself was OK as I got about 300 VAC at about 350 Hz between any two phase outputs. Next I connected it up to the control box (wearing goggles and ear protecters!), ran the engine again and attempted to start the thing producing an output. All the correct lights went on so I though that was good. After that I set it up with a multimeter on the output to see if there was actually 230V there. On starting this time, there was a huge bang when a varistor across one of the bridge rectifiers exploded. I know it was pretty stupid actually connecting up the unit with full voltage in the field coil and high revs to start the engine, but it was going so well up until then! Anyway, apart from the new problem (which I really hope hasn't destroyed anything else like the diodes) I think I've deduced that the control box isn't producing a field output at all (interestingly, you get about 14V AC output without any field current, is this due to residual magnetism in the alternator shaft?). More investigation soon when I can be bothered again. Has anyone got a spare V275PA40A varistor?
-
I thought a picture might be useful, I'll try that this evening - it might turn out to be something that somebody has seen before after all. It is definitely true sinewave (well it says so on the case) - we use it to run the washing machine. The input from the alternator to the control box seems to be rectified by three high-power bridge rectifiers to give what is marked on the PCB as 400V DC, which then goes to the inverter stage of the circuit. The 9 wires are: 3 red, 3 yellow, orange, black and white. There seems to be 4.8 ohms between any two of the red wires and about 1.4 ohms between any two of the yellow wires (IIRC). I presume the white one is the field wire. Maybe all of this is irrelevant and it's just some simple control circuitry that's gone, but I'm always curious to understand stuff in more detail anyway (don't particularly want to start unmounting and taking apart the alternator yet though!) Simon.
-
It does need battery power, yes, and I think the field rotor is getting it as there appears to be some output from the alternator when it is spinning. Not knowing much about alternators I could be missing something obvious, but I believe that side of things is OK but will check again. As an aside, I wonder what kind of output the alternator is supposed to produce to get a 5kva 230v output from the control/inverter box. Must be quite large, but the wiring looks pretty weedy (even though it is three-phase) unless a high voltage is produced by the alternator. When the unit first stopped working, I noticed the one of the wires to the remote control had come off. "Aha" I thought, "that must be why it's not working, I'll just solder it back on and we'll be able to do the washing again". Alas, it was not so, with the remote completely disconnected, and using the buttons and indicators on the control box, the same thing still happens. And I have shecked all the connections to the alternator. If it's the control box you're right, it won't be easy to fix (a) because of lack of a circuit diagram or explanation (could it be something else badged as Sterlnig?) ( the presence of dangerous voltages. Simon. Oops, didn't mean to put that smiley in there - dangerous voltages aren't that cool!
-
That's exactly my concern... no traceable design or build standard! But someone must have a similar thing. Or are 230v engine generators not as common as I think they are?
-
Hi there. I've got a problem with my Sterling 5kva engine-driven generator. Normally to start it working, you press a black button which puts a load in the alternator causing the engine sound to change and an LED lights up. Then holding the button for a few seconds makes the "minimum RPM OK" light go on and you're away. Now I press the black button and the first light goes on but no change in engine sound and the thing won't "strart up" Does anyone else have one of these? It consists of a modified Bosch alernator with a 9-wire loom to a control box which rectifies the output and then inverts it to give a 230v sine wave output. I can find absolutely zero information about it, but it must be a bit like the electrolux travelpower I imagine (can't find anything about that either). It came with an A4 sheet of installation instructions (it was already working when I got the boat) and there is no model number or any other clue about its design or circuit diagram (the only thing I know is that it was made in 2000). A circuit diagram would be most useful, but trying to contact Sterling is probably a non-starter after my last try. Going to buy a standalone generator soon, but it would be very useful getting this thing working again as I understand they are quite expensive to install... Do I have the only one in the world?!? Any leads, I've run out of simple ideas? Thanks, Simon.
-
Having just bought a second hand boat with a sterling 1800W inverter and 5 kva generator, I posted on here a couple of weeks ago about N-E bonding of the inverter and generator, and the best way to do it. I just phoned Sterling about this and was absolutely shocked at their "Technical Support". I spoke to some Irish guy, who didn't appear to know anything about my inverter and told me things like "why do you want to do that", "it's fine as it is", "don't know , you can if you want" and "(this earthing and RCD stuff) it's all bollox". Me: "So, what about the generator, that has an earth lead coming out, what's that connected to inside? Can it be bonded to the neutral?" Sterling guy: "Uh, don't know, might be connected to the case or a capacitor, just connect it to what you want." Plus more etc. etc., and it gets better (/worse)...! I then phoned back to ask if there was anyone else I could speak to. Sterling guy: "You inverter is quite old, we got them from the far east and modified them, there are thousands out there, they work fine" Me: "So if I did want to bond the N to E and the hull on both the inverter ......" (and the generator, would that be OK?) Sterling guy: "Look, it's your kit, just do what what you want. Bye" He hung up. Unbelievable! Almost hilariously useless. Is this typical of technical advice from Sterling? I can see that their printed instructions are crap too. I think I will not be buying anything from them ever... So, anyone got any real helpful advice???!!! Simon.
-
OK, thanks for your replies so far. Just to say I am an electronic engineer so do understand things like impedance and capacitative coupling, so wouldn't really class myself as a "beginner" as technical language is very useful to me. However, I appreciate that I am not a fully experienced marine electrician so "option 6" will almost certainly be involved at some time or another, especially if internal equipment modifications are needed. Some of my 'suggestions' were deliberately a bit weird, just wanted to see if others had anything similar. I realise that a neutral-earth bonded system is safest and can see all the reasons why that is so. So maybe I could simplify the questions a little. I suppose basically I am asking if anyone has an inverter which cannotbe earth-neutral bonded? (Mine has no internal connection to the output socket 'earth' pin and no stud on the case, I have yet to find out if the case really is at the centre-tap or whether it is just somehow coupled, and could be brought to the same potential as one of the output pins. Maybe it is possible but then why no stud connection, if so was it just that output-earth bonding wasn't standard practice when it was made.) Ooops, lunchtime ove...... got to go. Simon.
-
Hi there, Firstly, hello to you all. I've just bought a narrowboat to use as a liveaboard, but the electrical installation concerns me slightly - I'll try to explain what the situation is at the moment and what I believe the potential solutions are, so here we go... OK, there are three sources of 230V AC power 1) a landline via an isolation transformer, 2) an 1800 watt Sterling I241800 (non-sine) inverter and 3) a Sterling 4.8 kva enhine-driven generator. The switching arrangement is a bit strange but essentially you can select any of three sources via double-pole toggle switches. (The 230V ans 24V wiring all appears to run close together and is intermixed at the panel which has got to be pretty unadvisable, but that will be dealt with.) There is NO (intentional) hull earth-neutral bonding at the output of any of the three sources (no RCDs are installed) While the inverter was powering the TV the other day I got a tingle from the antenna connected to it, subsequently I measured about 60 volts AC between that and the hull, which I thought was strange as I expected the AC system to be floating. At the output of the inverter, I then measured 60 volts between the hull and one pin and 180 volts between the hull and the other pin. Weirdly, when the output from the inverter was unplugged, I measured 120 volts from either pin to the inverter case. I coucluded that the (perhaps faulty TV) antenna might be connected to the 'neutral', which would obviously not cause a problem in normal earth-neutral bonded systems at home. An unrecognised fault or unpexected condition must have occured in the wiring causing a dangerous potential difference between bits of exposed metal (i.e. the hull and the antenna). So currently, from everything I've read, I can understand that providing a neutral-earth bonded system with RCDs would be a good idea. Here are the problems... 1) The inverter case appears to be at the L-N mid-point, does this mean it cannot be E-N bonded? Does anyone else have the same or similar inverter? 2) The generator is also "split phase" I believe, so there is a dangerous voltage on bothe the 'live' and 'neutral' 3) The iso-trans has a centre tap on the output but it is not used. So, should I (in increasing order of expense)... 1) Leave it as a floating system. Very undesirable due to the problems of dangerous undiagnosed faults in installation, until it's too late... What do the BSS, and various codes of practice say about this (was it ever allowed and what about now, would it be counted as a 'new installation' if anything at all was changed?) 2) Can this inverter and generator actually be E-N bonded? (If not, why not, why were they built like this, at what point in history was this deemed preferable?) Best case, but a bit hopeful. 3) Maybe use a "split phase" system (iso trans centre tap, inverter case (if it is really at the output mid-point) ans generator midpoint all bonded to the hull). Advantages - can hopefully be done with existing equipment. Disadvantages - will RCDs work just the same with only 115v between fault conductor and ground? Is most domestic equipment OK with this, since it expects a neutral 'neutral' which should be safe, not a hot 'neutral'? Is there also an issue with colour coding of the wires here? 4) Do all the source switching BEFORE the isolation tranformer, that way I could bond the iso trans output to the hull, and use an RCD as intended. Not sure of the pitfalls (e.g. efficiency?) with this but it can't be that standard. 5) Buy a new inverter and generator. FAR too expensive. Sorry for all the detail and questions, I've probably still left somthing important out. Thanks for your time, hope I can be of help sometime in the future once I've got up the narrowboat learning curve a bit. Simon.