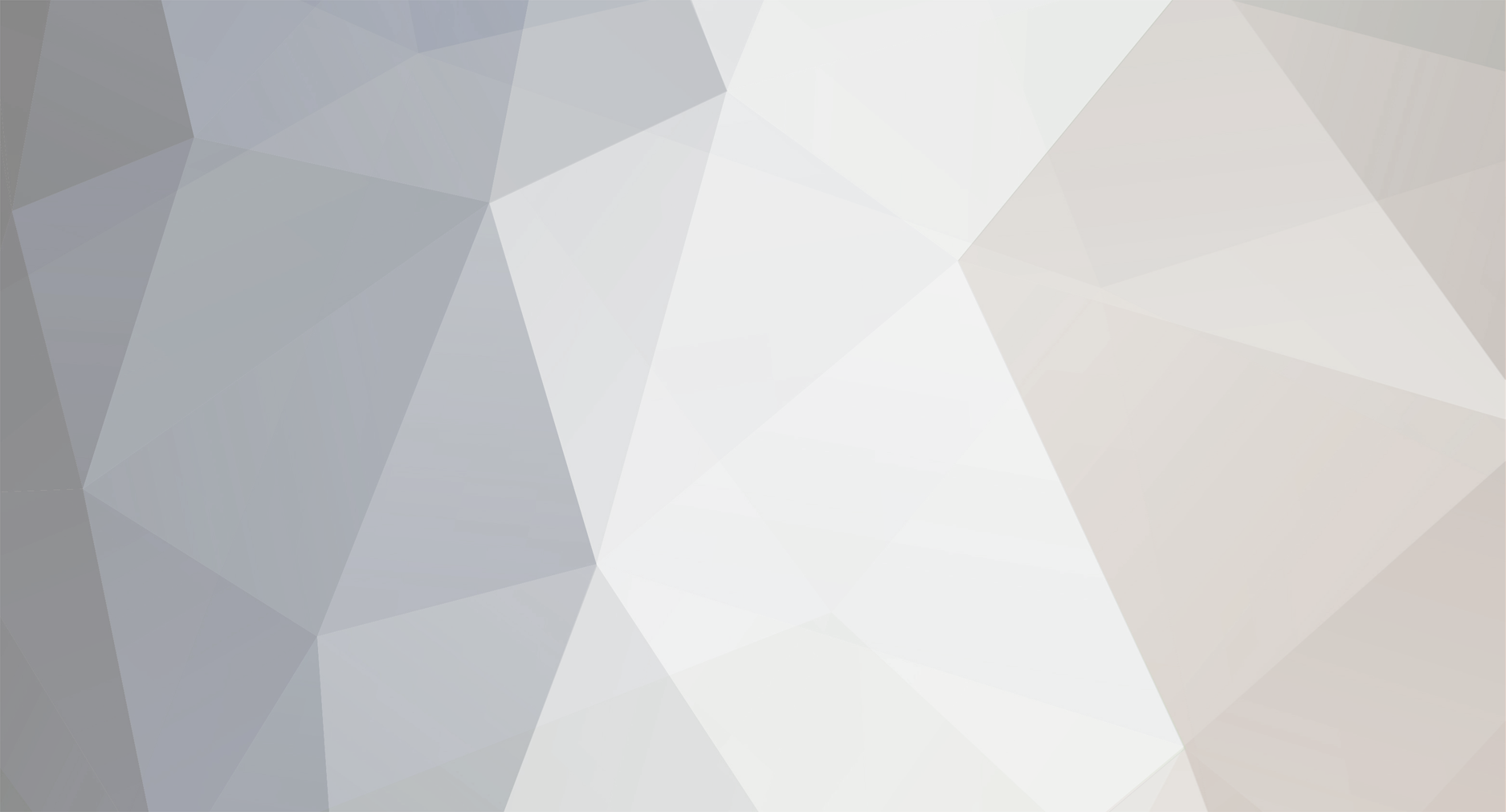
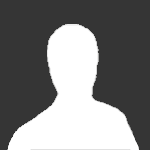
sueanddaren
-
Posts
238 -
Joined
-
Last visited
Content Type
Profiles
Forums
Events
Gallery
Blogs
Store
Posts posted by sueanddaren
-
-
Thanks gents the two plumbers I showed the photo to just shrugged their shoulders. But they where quite young.
-
Does anyone know how one of these comes apart?
Does it have a washer or some sort of sealing face?
As its very old I don't want to break anything.
-
1
-
-
Try a food dye in the tank and see if the wet patch comes out coloured.
-
Don't know if this helps but the Barrus Shanks engines where Liadong engines (Shandong Huayuan Liadong engine company) think the popular one (40hp) was a LL480 but can't be sure about the exact model.
-
19 hours ago, cuthound said:
We will just have to agree to disagree over that.
I can live with that.
-
8 minutes ago, cuthound said:
No, my colleague in headquarters liaised with Yuasa from 2000 to get their pure lead thin plate VRLSA's specifically to reduce the number of early life VRSLA failures. I left BT at the end of 2007, so they may have changed the specification since then. The Gates pure lead acid VRSLSA's used in the 80's certainly had much thicker plates than their competitors.
Sorry Yuasa don't have or have ever had TPPL. You can't make TPPL on ordinary grid casters, you first have to roll the Lead to the thickness you want (normally around 1.4mm) then punch the grid. Around 2010 Enersys Newport managed to modify a concast machine to cast in pure and it took Leoch 5 years to copy that.
-
2 hours ago, cuthound said:
The Chloride product suffered group bar corrosion too, I dismantled many of these batteries from the mid 80's until the mid 20's when BT changed its sole supplier of VRSLA's to Yuasa, who made thin plate pure lead VRSLA's.
The high temperatures in the exchanges resulted from decisions made in the 70's to change from wet cells to VRSLA's and house them with the switch and transmission equipment rather than in their own dedicated battery rooms and to cool the equipment areas using fresh air cooling for up 85% of the year (the Air Handling Units contained a small compressor refrigeration unit as well as fans). This was based on the outside temperature only being 35 degrees C or more once in a hundred years at the time of the decision, but by the mid 2000's it had became something that occurred most summers in the UK. As you say, the increasing equipment room temperatures resulted in the installation of full time air conditioning for the hotter exchanges. I have seen temperatures in excess of 50 degrees C in exchanges where the high summer ambient temperatures coincided with a mains failure.
I witnessed some "System X" tests at Plessey in the very early 80's where the switch and transmission equipment was still working at 70 degrees C, however the rate of change of temperature had to be closely managed to get the equipment up to that temperature and back down to normal again, and the batteries were useless after being subjected to that temperature for a few hours.
Sorry BT used the Yuasa EN100-6 which is a lead tin calcium product they don't have a thin plate pure lead product, only Gates (then called Hawker, now called Enersys) Northstar (again now part of Enersys) and Leoch had or have TPPL.
-
7 minutes ago, cuthound said:
Yes BT initially took VRSLA's from Chloride, Tungstone and Gates (Hawker Energy). All had a predicted 10 year life.
Only the Gates batteries achieved this, the others failing after as little as two years. It turned out that only Gates used pure lead plates and group bars and the other manufacturers used alloyed group bars and plates. The alloyed batteries were failing because group bar corrosion was causing the plates to fall off in extreme cases. This was exacerbated by the average temperature of the batteries being above 25 degrees C, which reduced battery life.
Not quite, it was the Tungstone product that had the group bar corrosion, they put them down their automotive lines and used antimony in the neg group casting. The Chloride product was fine in most cases unless the temp of the exchange went too high, as the telecoms industry boomed they crammed more and more equipment into the exchanges this gave off allot of heat and that speeded up the pos grid corrosion. Ive been in one central London exchange that was at 37 deg C even in mid January. Even the Gates cells couldn't take that sort of temp for too long, nor could some of the exchange equipment, so they put air con eventually.
-
At the very cheap end of the market some manufacturers have always used screw in caps on VRLA batteries, it allows them to get away with using standard lids and boxes. That said it does allow for the vent pressure to be pre tested before fitting. As for adding water to AGM, it can be done but you need a vacuum pump and a swap over filling head otherwise the water just sits on the top of the element.
Without taking the whole battery apart and squeezing a sep between my fingers even I can't tell if the sep is too dry or not.
Back in the early 1980's Exide tried to get into the AGM telecoms market without really knowing what they were doing and got the alloys all wrong. The cells gassed too much and dried out in less than a year, they had teams going round to all the AT & T sites adding water. Cost them a fortune and gave us (Chloride) an open market.
These days everyone knows how to make AGM, but I have still seen the odd Chinese company get it wrong.
-
3 minutes ago, Alan de Enfield said:
If they are not the same company (Knights Narrowboats) that closed in 2020, what is the name of the company in Aquaduct Marina ?
Knights Narrowboats | New Build Narrowboats | Aqueduct Marina
-
25 minutes ago, Tracy D'arth said:
And that is in Church Minshull not Middlewich.
Yes
-
Knights are built and sold out of aquaduct marina.
-
- Popular Post
- Popular Post
The hardener that PCSB gave me worked brilliantly.
So the paint is a 2K Acrylic system normally used on commercial vehicles. PCSB also had the spec sheet, so I have managed to find a 0.25liter tin of hardener for less than £12.
Result
-
7
-
12 minutes ago, PCSB said:
If you are passing Middlewich in the next day or two, we are moored on the branch, I can let you have some hardener to see if it will work.
Thanks can you pm me your details?
-
1
-
-
16 minutes ago, PCSB said:
It looks like an auto paint as in cars, in which case you will need a hardener. Usually known as 2 pack paint. It is an epoxy based paint I believe. Whereabouts are you?
Cheshire
-
Just rung them, they think it might be something called spiezeca (but they can't be sure) and a tin of hardener is £45 plus £10 P and P or it might be something else.
-
16 minutes ago, bizzard said:
Cellulose paint has a very pungent powerful smell, very different to ordinary oil paint. Cellulose thinners will clean oil paint off brushes indeed most paints. Most Ordinary oil paint uses linseed oil as the dryer.
clean
Are you suggesting using Linseed oil?
Are you suggesting using Linseed oil?
14 minutes ago, beerbeerbeerbeerbeer said:Can you provide images of the labels on the can?
Will help identify what paint you’re using.
Does the paint at least go tacky to the touch?
After about a month it goes bobbly but is still soft.
-
When we bought the boat the previous owner gave me a 1 litre tin of the same green paint. I have tried it on a small scratch and it is a perfect match however it does not dry, even after a week in hot sunny weather. I assumed it was cellulose paint as that's what I managed to clean the brush with having failed with white spirit. The boat is also spray painted.
So far I have tried adding Owtrol to a small sample with no luck and epoxy hardener again with no luck. Does anyone know what I can add to make it dry?
-
Pretty sure alternator is an Iskra AAK1812 and the regulator is an AER1701:-11.203.657 AAK1812 MG581 MAHLE (Letrika, Iskra) alternator (11203657) - Trade Service Kft
This reg has a set voltage of 14.2 . I tried for months to find a reg but gave up and changed the whole alternator, be careful if you go down this route as most of the replacements are upgraded to 120A (like the MG851 that Tony linked) and you only have a single belt.
-
Thats not a Powertwist belt, I think its called a T link belt.
-
Sad to hear John died....When he 'tested' the hull on our old boat by hitting it with a b*****y big hammer, he said if it ever needed plating he'd do it for free. He was a character.
-
2 hours ago, Mark R said:
Hi Tony,
Just an update. I’ve unexpectedly gone to my boat today and taken a much closer look at the morse control, which I now believe to be the MV-1. After getting my hands dirty, the improvements have been fantastic. There is a huge improvement in control, the handle takes the boat into forward and reverse and the acceleration in both directions goes from the gearbox turning very slowly and incrementally increasing in speed as the handle is pushed forward or pulled backwards. There is no longer the slamming into gear that I’ve previously experienced. I’m hoping that I’ve not damaged the gearbox in anyway, time will tell, at the moment it sounds pretty good.
The amendment made was to the shift cable where it met the control arm. It was wound out a few turns and the nut on the cable tightened, I think this allowed the cable to push the arm at the gearbox that little bit further, ensuring it went into gear, something it must have just been missing previously. From the information I’ve gained, it looks like the cable also needs to be attached to the arm in the same direction as the throttle cable. I’ll do this when I’ve purchased a few replacement split pins. You wouldn't by any chance know where I could purchase the pivot (the part that the split pin threads though)? Seems they are only available in the US.
Once again, thanks for all your input, I’ve found it invaluable. If you are anywhere near Stockport I’ll buy you a beer or three!
Mark
Try looking for clevis pins
As an example:-Clevis Pin Bright Zinc Plated Steel, All sizes | eBay
A thin washer under the split pin also takes out some of the slack.
-
2 hours ago, Tony Brooks said:
Thanks, that part number should help the OP
Any idea where the modification came from?
Wish I did, we had that boat for 14 years, contacted all the previous owners even spoke to the guy that actually built her, but never found out about the pulleys or many other odd things. The engine however was marinerised by Oxford Marine but never found any info on them.
-
Our old boat with a BMC 1.5 had a very similar modification, that used a 4PK1052 belt, but until you offer up a new belt to the pulleys it is very difficult to tell.
Clicking when trying to start engine
in Boat Equipment
Posted
Ronaldo47 posted this a couple of years back:-
Unlike ordinary lubricating greases,which are designed to strongly adhere to metal surfaces to prevent them coming into contact,;Vaseline is a pure hydrocarbon that readily flows under pressure and does not strongly adhere to metals. It therefore allows the metal surfaces to achieve a good electrical contact while preventing atmospheric oxygen from coming into contact with the mated surfaces and oxidising them.