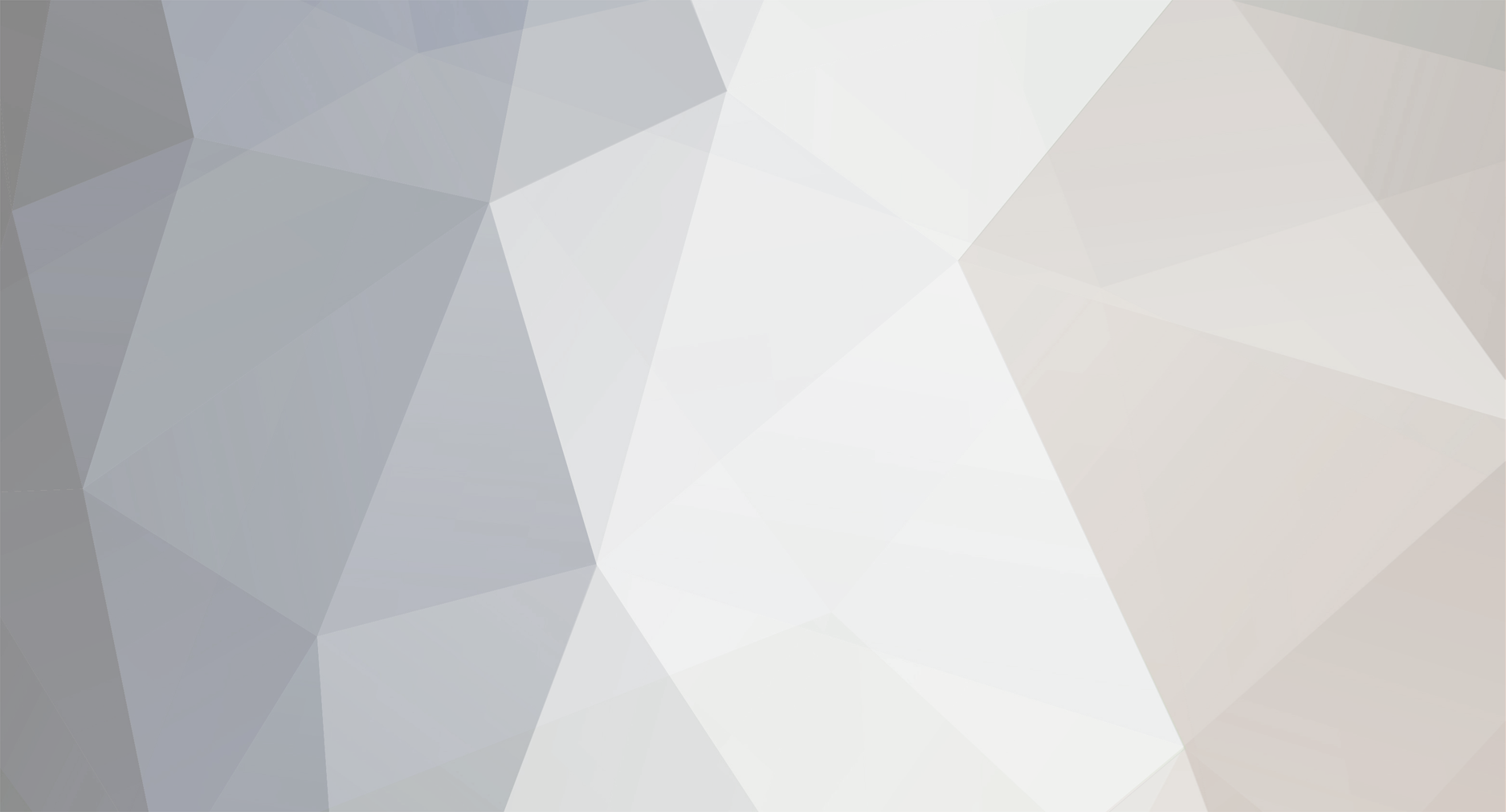
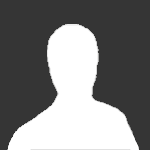
Craig Shelley
-
Posts
62 -
Joined
-
Last visited
Content Type
Profiles
Forums
Events
Gallery
Blogs
Store
Posts posted by Craig Shelley
-
-
1 hour ago, ivan&alice said:
Do you use a thermostat with it?
We currently have no thermostat. I cut the heater film into 3 separate sections, one for each battery enclosure. The heaters were then wired together in series instead of the original parallel configuration. That reduced the overall power to a level sufficient to provide a gentle heat which, from memory, eventually reaches an equilibrium temperature approx 20 degrees above ambient.
This enables the heaters to be left on without any means of control. Fuses provide basic protection for over current, and the switch is a guarded and illuminates to give a very clear indication that the heaters are powered.
As the new monitoring system gives us better visibility of battery temperature, it is theoretically possible to automatically control the heaters. I doubt we'll ever get around to making that happen.
1 hour ago, ivan&alice said:Do you mean to say the cells are blocks of 4 in series x 3 blocks in parallel?
There are 3 separate enclosures, each containing 4 cells in series. The -ve and +ve wires from each enclosure connects to the busbars.
-
- Popular Post
- Popular Post
1 hour ago, ivan&alice said:How's everyone's installs coming? Would love an update @redwing and @nicknorman!
The past couple of months have been fairly heavy going with this project - a final push to get a BMS designed, built and installed. We're beginning to see light at the end of the tunnel.
The MK2 prototype is now installed although more work is needed to move the current the measurement functionality across to the new system.
Just a quick re-cap on this project so far:
12 CALB 210Ah batteries purchased from EV Support in 2017, and installed with no BMS.
The only means of monitoring for the first year was via a 5 digit panel volt meter, and 3 ammeters.
A under/over voltage cut off switch was implemented using a BlueSea Systems remote controlled switch wired to two off-the-shelf voltage switch modules.
In 2018, a rudimentary means of estimating state of charge was lashed together using a raspbery pi zero and a waveshare ADS1256 module.
A few op-amps in a breadboard provide some level shifting and scaling for the ADC. Two years later, this lash-up is still running in on a breadboard on the top shelf of the electrical cupboard.
The means of logging data via a google sheet, and plotting using the graphing facility has proved to exceed our expectations regarding reliability and flexibility. It's extremely useful to be able to view the live graphs from anywhere using the google sheets app and it has the ability to share access with family members etc...
Time eventually came to build a MK2 unit to overcome some of the limitations, and make a proper installation. Also by this point, I was beginning to get a little nervous about what might be going on with the individual cell voltages. We have only ever carried out spot checks on the cell voltages, but there's never a convenient time to do it. Looking at my spreadsheet, the last measurements were taken nearly a year ago!
By this point I have a reasonable idea of what was needed, and what I wanted! I was hoping that an off-the-shelf system would be available by now, as what we're doing isn't exactly novel, and we're not alone in needing a means of precisely measuring multiple voltages. Each time i've looked, the available systems haven't satisfied our specific needs. For instance, many of the multi-cell monitoring solutions are designed for long strings of cells in series, not series-parallel combinations. Also i'm not convinced by the accuracy if the individual per-cell PCB modules as the ones i've seen just rely on the built-in reference within the microcontroller. Having become accustomed to seeing the overall pack voltage displayed with mV resolution and how useful this is whilst observing charge/discharge, I was determined to design something at least as good, but also had an accuracy to complement this resolution. i.e. able to measure the 12V pack voltage within few millivolts.
Our setup adds extra complication in that we have 12 cells to monitor. Whilst we could add connecting links between the cells to reduce the number of voltages which need to be monitored, we've chosen not to add the links for the following reasons; Firstly it would be a bit awkward due to the physical layout. Second I believe it might reduce the fault resilience of the pack i.e. 1 faulty cell might then take out 2 more cells. Finally it would not be easy to measure the individual performance of the cells without breaking the links.
The system I've ended up designing, for the most part follows a very traditional layout of ADC, instrumentation amplifier and multiplexer. It provides 30 measurement nodes with a somewhat unusual, but flexible multiplexing scheme. It is possible to measure differential voltages between any two nodes; therefore only 5 nodes are needed per battery pack. This scheme enables the polarity of the measurement to be taken in forward and reversed directions. By subtracting the reversed measurements it is possible to eliminate voltage offset of the signal path. A precision voltage reference IC is available via internal nodes 31 and 32 to allow the system to continually self-calibrate.
The C code for the raspberry pi is now fully written, I've ended up reusing most of my old python script for uploading the data samples to google sheets. The next phase is to produce some meaningful graphs/dials on the google sheet using the data. I've ended up doing a fair bit of verification work on this prototype unit, even checked it against a reference standard. At 10V the measurement error against the standard was less than 1.5mV. This equates to an error of 0.015%, which is acceptable and well within the spec of the reference IC. It's possible to further reduce this either by using the trim facility available on the reference IC, or by software calibration. I don't think it's necessary to go that far.
With the system installed on the boat, a comparison of the sum the individual cell voltages, with the measured overall voltage was found to give a discrepancy of less than 100uV on each of the packs.
So after 3 years without balancing, the battery pack isn't looking too bad. We'll need to leave the monitoring system to gather more data across a range of SOC. Initial data with the cells with a light load and at about 75% SOC is showing a maximum cell to cell variation of 2.5mV.
There's still a lot of work to do on this project. The next job is to retire the old lash-up system but to do that the battery current measurement signals need to be moved onto this MK2 system.
I've drastically underestimated how time consuming this project would be to complete. My biggest oversight so far has been the time taken to build of the prototype unit. I wish i'd gone straight to PCB. After all i'd gone to the effort of properly drawing up the schematic. Due to the way i'd drawn the schematic, I underestimated the sheer number of interconnections needed - well that's 8 days i'm not going to get back!
Making the cable assemblies also seemed to take forever. At least the end is now in sight!
Photo shows prototype MK2 unit assembled onto lid of diecast enclosure.
-
6
-
12 minutes ago, ivan&alice said:
Since this is a bit of a niche topic I thought I'd continue this thread rather than starting a new one...
My BMS is set up to trip the charging relay at low temperature. But a better solution would be to warm the cells up so that they can be charged safely.
I've been told to use soil warming cables or vivarium heating pads for this purpose, as they apparently come in 12V versions with thermostats. The reptile ones especially have temperature control in the right range (0 to 35 degrees). The ones I find online are 240V though.
I did find plenty of thermostatically controlled car seat warmers which sound ideal, but I expect I need a thermostat that is much cooler - shutting off at 5 degrees or so.
I know that keeping them in the cabin goes a long way towards keeping them warm, but the room they're in does get cold if I'm not in it and running the diesel heater, and don't want to rely 100% on that. I would love to hear any suggestions or how anyone else has solved this problem.
How's everyone's installs coming? Would love an update @redwing and @nicknorman!
We ended up using these heated mats. (See photo) They are available on eBay, search for "camper van heating mat" They are rated at 220w/m2. They can be cut down lengthways to fit the size of your enclosure.
We have 3 wired in series which, from memory, draws about 1 amp at 12V. In our setup this provides enough heat to maintain the cells above 5 deg C when the ambient temperature is at about -10 deg C.
We've fused both the +ve and -ve supply feed to the battery heater circuit so that a single fault e.g short to +ve battery terminal could not cause a meltdown.
--
Craig
-
1
-
-
Hello,
Apologies in advance if this question has already been discussed in this thread.
I've just been trying to determine the "number of cycles" we're putting on our battery pack per year. I have doubts that this data has much meaning because it doesn't factor in depth of discharge, but was trying to get a rough idea of usage/aging.
The values i'm getting are in the region of 30 - 40 cycles per year, that's on a ~600Ah pack.
Just wondering if these values seem sensible.
The method used to estimate this, which is perhaps a little debatable, is to sum the absolute value of the charge for all samples to find the total charge which has passed through the shunts (in+out). Then divide by 2, and divide by the capacity. I also subtracted the measurement drift error which accounts for 3 cycles or so.
I imagine there will be other factors which affect cell ageing before the cycles do.
--
Craig
-
12 hours ago, ivan&alice said:
Per cell or across the whole 12V battery?
That's the whole battery, but the measurement point is not right at the battery terminals. It is at the "bus-bars", the junction points of the 3 packs. These are connected with about 1m of 50mm2 wire to each of the 6 terminals.
The cells are connected using the proper links, all connections polished before tightening the bolts etc... I would say the majority of that drop will be from the cells rather than the wiring.
-
For comparison, on 12x SE210AHA cells, we drop 0.42V at 130A.
-
Might be worth taking a look at how the heating element is wired. If you're very lucky there might be 2 elements in parallel, which can easily be reconfigured. I'm doubtful though.
Other options; to fit a series diode on the heater to half the power, fit a series capacitor in the heater circuit, install a trasformer/autotransformer, lower the voltage at the inverter (some are adjustable e.g. 210-240v), disconnect the heater, fit a lower power heater, mod the hardware to shut off the heater when motor runs, mod the software, choose a different wash cycle, only run the wash when batteries are at a high SOC and warm, adjust the low battery voltage trips to be less sensitive to transients, install more batteries.
-
My guess would be the current surge when the motor starts, combined with the heaters being on is causing the voltage to dip momentarily at the batteries. Does the BMS have any time delay or filtering functionality to prevent a momentary dip in voltage from tripping the battery disconnect?
-
On 21/07/2020 at 09:30, Dr Bob said:
There is something funny going on if your washing machine on a cold cycle took the voltage that low yet your toaster and hair dryer didn't. I agree with MP your voltages are low. Important to put the clamp meter on - and check all 3 to see their comparative draws.
Jeremy who sold you the batteries does check them by putting them under a load that is seen by EVs. Not sure if that is 1C, 2C or 3C, but likely to be at the high end. When MP and T&B got theirs, he said they were not quite there for EV usage so they got them cheaper. When I got mine he had run out of the 'weaker' ones so I had to pay a premium as mine were fit for EV duty. I am sure he will have told you which category yours fall into but even the weaker ones should be able to cope with any boat duty they are asked to do. My Tesla does 0-60mph in 4 secs. God knows how much power that draws!!!
As Richard says above, could it be a bad connection? Maybe one of the battery cell interconnects is not perfect? I think I remember you saying you had split the bank down a number of times? That would be my best guess but looking at the draw on the washing machine, the toaster and the hair dryer might help.
I know I have seen it but can you repost the diagram of how you have everything wired up.
Hi again, I've been keeping an eye on this thread for a while now, and was curious to know how many other people on here are using old cells from Jeremy at EVSupport?
On the subject of voltage variation, we've noticed the batteries appear to have a higher "internal resistance" when state of charge is lower. This has caused the low voltage protection to trip out when starting the Dyson. I don't think this is helped by the fact that we often have the inverter in power save mode, so not only is there the surge current from starting the motor, there is also the inrush current of the inverter charging its DC link capacitors. This hasn't been a problem in the past couple of years as we've improved the state of charge monitoring and now maintain a higher SOC during cold weather.
I saw, a few weeks back, discussion of cell configuration series-parallel vs parallel-series. All of the points seemed quite valid, but there are a few extras I'd like to throw into the mix.
To simplify integration into the existing boat wiring, we went for 3 parallel packs, each consisting of 4 cells in series. The obvious downside is that much more monitoring is required, not that we've installed any yet. But this gives more flexibility for the cells to settle at their own preferred voltages. The danger we envisaged was that one cell becomes out of balance, and suddenly starts to dip in voltage. However, since the cells are all separated between the packs, a single lazy cell causes a reduced contribution to the overall current from its pack. We do notice this as we have independent ammeters for each pack. Sometimes one pack will be providing a lower current than the others. Later on the same day, the same pack might be providing a slightly higher current than the others. It all ends up balancing out, but hints at how imprecise and chaotic the cells really are inside.
-
Before it went offline, the Willington gauge prediction was showing a bit of a bump. See attachment
We're moored on the pontoon at trent lock, and there are a couple of narrowboats before the floodgates on the cranfleet cut which have started to break free from their moorings. One is currently on the towpath facing the opposite direction - the owner is aware.
The other also appears to have broken free at one end, but we haven't seen the owner yet.
Access is currently a little awkward due to the water level.
-
On Monday morning (4th Nov), my father was approaching bridge 55 on the Trent and Mersey, and was told by walkers on the tow path to be careful as another narrowboat had come adrift near the bridge.
CRT staff boarded the boat as he was passing it, and were securing it to the bank.
Unusually, the front doors on the boat were open and there was no front mooring line.
Today while we were out walking (different location) my father recognised the same boat and ended up chatting to the owner. It turns out it had been broken into, and ransacked. Among other things, domestic & starter batteries, tiller, windlasses, and mooring lines had been stolen. The owner had left boat quite substantially and visibly secured, and would have required a determined effort to break in.
-
Just catching up on the past few days of messages.
I'd advise at least having a panel voltage meter with 3 decimal places of precision. Over time you develop a "feel" for the state of charge based upon the voltage.
In our system, we had no bms or cell level monitoring.
In the early days, we didn't know what limits to work to, and had very little instrumentation, no ammeters etc...
The measured voltage predominantly depends on two things; state of charge and load/charging current. When the batteries are in a rested state I.e. Very little load/charging current for a couple of hours or so, the voltage is a very accurate indicator of state of charge. For us, 13.330V fully charged 13.200V middle ish. 13.100V middle to low, 13.000V we try to avoid going too much lower than this.
At either end of the charge curve, you notice the voltage fluctuates much more.
For the first few months after installation, we kept the voltage around the 13.2V region. As we later installed the various safety systems, we became a little more adventurous, and carefully explored the upper and lower ends of the characteristic.
While charging, the measured voltage will be higher than the resting voltage, and will depend on the charging current and state of charge. Annoyingly, charging current depends to a certain extent on alternator RPM.
During the middle three quarters of the capacity curve, the voltage doesn't change a great deal as the batteries are charged. For example if the alternator is kicking out 80A, at about 50% SOC we might see ~13.6xxV for well over an hour. This is where the extra decimal places on the meter really help. The numbers will slowly be counting up as the batteries charge e.g. 13.614 ... 13.615 etc... You get a good feel for the rate of charge.
When approaching about 80% (what we call full), the voltage starts to rise quite rapidly. The last decimal place becomes a bit irrelevant at this point because of the speed the voltage is moving. At somewhere between 13.9 and 14.0V, we cut the alternator field and charging stops.
The battery voltage rapidly drops to say 13.4xxV. It then takes an hour or so, depending on load current, for the voltage to settle out at the resting voltage value.
When choosing a voltage to cut the alternator off at, we were initially very over cautious. The problem with setting it too low e.g.13.7V is that the dependence of charge current on engine RPM means that while traveling, revving the engine might cause the current to ramp up momentarily. This causes the measured voltage to increase, and hence lead to premature tripping.
As we got more accustomed, and understood what was happening, the trip threshold was gradually increased. We're now quite happy with a value around 13.95V. Providing the alternator is supplying sufficient current, the voltage does not remain at this high value for any significant length of time. Once the voltage has passed about 13.7V, it really does start to rise quite quickly, accelerating as it goes. The alternator cut off threshold is then tripped cleanly and is far less susceptible to premature triggering.
This strategy gives a clean cut off at a consistent state of charge.
It would be nice to either control the alternator current to a set value, or compensate for its variation using a software battery model.
To summarise; the measured voltage is mainly determined by the battery, which is predominantly dependant on state of charge and load / charging current.
With LA batteries, the alternator is required to regulate the voltage while the battery absorbs the energy.
In my opinion an alternator voltage regulator is not needed for lithium unless you wish to either fully charge the batteries to 100% using CI/CV mode, or wish to regulate alternator temperature/engine load, or if the alternator current rating is too high for the capacity of the battery pack.
-
2
-
-
Just now, WotEver said:
How would that work then? Short the +ve charging cable to the hull and the fuse in the +ve cable would blow.
The fuse in the +ve is 250A to the motor controller.
The fuses in the +ve and -ve charge cables are 50A.
The charge cables are 10mm2, and route through the cabin. The negative terminates at the busbar. The +ve goes via a charge relay contact to the starter alternator.
If "somehow" the +ve bow thruster battery terminal were to be shorted to the hull, the fault current would circulate via the hull and engine to the negative busbar, then back along the charging cable -ve to the bow thruster battery.
Without a fuse in the -ve there is a possibility that the -ve charge cable might burn up. At 10mm2 I'm doubtful it would go that far, but the cable does run through the cabin. There's no harm in fusing it close to the battery.
-
1 hour ago, nicknorman said:
Be careful with earth/0v straps. If you put a strap between battery negative and hull and if, like most people, you have an alternator and starter whose case is connected to 0v and an engine block that, by various means, is connected to hull (exhaust, control cables, fuel lines, prop shaft etc) then by adding another path between battery negative and hull, you provide a return current path between alternator and starter negatives, and battery negative, via the hull. Which is not what you want! Any 0v strap for the DC system is best taken from the engine to hull, for this reason. But obviously, since you already have a proven path between hull and battery negative (due to items mentioned above) there may not be much point in adding another dedicated one.
Very good point. Engine to hull would certainly be a much better place for a bonding point.
Also often overlooked is fusing the negative charging wire to bow thruster batteries, in case of short from +ve to hull at the battery.
-
1 hour ago, Alan de Enfield said:
I really wouldn't have expected it to have caused pitting on brass components as Brass is WAY up the Galvanic scale, virtually everything else on the boat (Steel, stainless steel, etc) are bellow Brass on the galvanic chart.
I think you may have another problem.
Sorry, there's an error in my original post.
The prop shaft actually has a flexible coupling, which is electrically isolating it. The prop shaft at the seal is at about +0.5V from the hull. I imagine this is due to the metal the prop is made from.
The lost return current can be measured at the engine -ve wire so it must therefore be returning via some other route on the engine e.g. exhaust.
-
Thanks for the quick reply.
Would this work for powered DAB aerial?
The aerial has two coax cables, and an amplifier power supply wire. The DAB coax is terminated with SMA/SMB connectors.
-
Yesterday, while tidying up some cabling, we discovered the current supply to the radio is higher than its current return.
Current supply: ~1A
Current return: ~400mA
The remainder has been traced to be going down the aerial cable screen to the hull, and then back to battery negative via the engine .
This may be unrelated, but when we recently serviced the prop shaft seal and discovered one of the brass components was bright green and pitted, indicating galvanic corrosion.
Currently, there is no bonding from battery negative bus bar to the hull. I'm going to install a bond wire with sufficient captivity to handle parasitic and fault currents. It makes a lot of sense to have a bond wire from the negative bus bar to the hull. There is another forum thread which discusses the need for a bond wire in detail.
The supply to the radio is shared for TV, and several cigarette lighter sockets. A percentage of the current from these devices is also returning via the radio.
Does anyone have any suggestions to prevent current escaping to the hull via the radio aerial?
-
1 hour ago, Dr Bob said:
We got ours from
Jeremy Bloomfield
sales@ev-support.co.uk
07736467455
www.ev-support.co.ukHe is based in Colchester.
Give him a ring. If he hasnt got any then he will know where to get some from. Ours are Winston thundersky bare cells.
He does not deliver. You have to arrange collection yourself. I drove down there.
Snap! Same person. He was very helpful, and even made us the cabling and connectors.
-
1 hour ago, WotEver said:
Gosh, he’s excitable!
I guess he got the wrong end of the stick when his doctor prescribed Lithium.
-
4
-
1
-
-
14 minutes ago, Mike the Boilerman said:
I'm getting more bemused. What button is this, please?
Sorry, I was being a little metaphorical. The "pressing of a button" implied taking a manual action such as operating a switch on the dash board.
This might be done after engine start, but ultimately, the decision of whether or not to run the alternator is with the helmsman.
-
3 hours ago, Tom and Bex said:
You also need to get out of the lead acid way of thinking. It really doesn't matter if the batteries are supplying boat loads after they are charged. You don't want to keep the batteries at 100% and leave the alternator supplying all loads. Unless you have a really small bank, and high usage, there should be no problem leaving the alternator disconnected after voltage hits set point. If it was really going to be a problem, then manually restarting charging wouldn't be too onerous.
Agreed 100%. It really isn't too onerous to press a button when you decide to charge up. A simple cut-off when a pre-set voltage is reached is adequate. It's also useful to be able to manually turn off the alternator when for example, you find yourself going against the flow on a river and wish to shed some load from the engine to help keep the temperature down.
While travelling, having the domestic loads supplied by the batteries after the alternator has "cut-out" really isn't an issue either, just a different way of thinking compared to LA.
The easiest and safest way of shutting down the alternator is to de-energise the field as is a relatively low current and trivial to switch with a standard automotive relay.
-
1 hour ago, Mike the Boilerman said:
Thanks Tom.
Trouble is, I hardly understand any of this! Could you, or anyone, expand into detail please? Are you proposing simply using the high power relay to disconnect the alternator charging output when the lithium battery terminal voltage rises to a certain pre-selected level?
If so, the voltage control board would need to be one which opens a switch when that pre-selected voltage is reached. I wonder if there would be any 'chattering' effect if the LA batts cause a slight fall in voltage on disconnection.
The accuracy of such a voltage control board would need to he high. I'll have a look on ebay now.
This one perhaps?
Features:
Digital display DC voltage detection, control the relay output.
Adjustable voltage limit: 0-99.9V.
When the measured voltage is lower than the lower limit or higher than upper limit value, the relay works.
Can be used for voltage detection switch, battery over/under voltage protector or discharge meter.
The instructions for this module are a little lacking, so some time back I wrote these notes:
long press set: output logic invert (can only be done if input voltage is not in hysteresis band) enter - toggle between displays: 1 Live Voltage 2 Minutes output has been on for Set key steps through settings: 1 Voltage measuremet 2 Upper voltage, above this relay will turn on 3 Lower voltage, below this relay will turn off (this cannot be higher than Upper voltage) 4 calibration +/- 0.5V 5 dl display shutdown delay in minutes Input pins (top right): When input is active, relay will come on irrespective of invert setting Jumper configures: Short to activate External 5V to activate Notes: At power on, output will always be off. At power on, if voltage is in hysteresis band, it will default to off. Hysteresis band can be configured so that output behaves like a triggered latch by setting one of the thresholds to an unrealistic value Crossing a threshold occurs when voltage has passed through the threshold and next digit is displayed i.e if lower threshold is set to 12.0, then the switch will operate at the boundary between 11.9 and 12.0 if upper thershold is set to 12.0, then the switch will operate at the boundare between 12.0 and 12.1 Power Consumption: 18.67mA relay off 49.5mA relay on 8mA display removed 39.6mA Relay on and display removed 15-20mA from 5V (output of regulator display dependent) 7mA from output of regulator with no display
-
3
-
-
2 hours ago, nicknorman said:
“Drop in” batteries typically have mosfets for over and under voltage protection, but this results in limited maximum discharge rate. Fine if you just want lights, pump, fridge, but no good if you have a 3kw inverter.
I think it still ought to be doable. MOSFETs are now down to below 500uOhms Rdson. Several in parallel would be needed for 3kw, but still cheaper than a motorised, or latching switch.
-
Are there any solid state solutions to this available yet?
Should be a lot cheaper and simpler than latching or motorised switches, in theory.
Would still want to have a proper switch for manual isolation though.
Cheap LiFePO4 BMS?
in Boat Equipment
Posted
I always find the term ”loss of capacity at low temperature" a bit of a curious conundrum. If the capacity of a charged battery goes down, where does the energy go?
Even if the voltage at the terminals is lower at low temperatures, the energy stored cannot simply disappear.
The main thing I have observed at low temperatures is the apparent increase in internal resistance. I.e. pulling a heavy load causes the terminal voltage to drop more when the batteries are cold. Likewise, our charger which charges until a voltage threshold is crossed, trips out notably earlier when the batteries are cold.
In an EV with long strings of cells I could imagine this internal resistance increase being problematic as the load would have to be stopped as soon as the weakest cell voltage reached its minimum allowed value. This would definitely cause an apparent loss of range.
I theorise that if the batteries were to be warned up, the the lost EV range would be recovered, hence energy conserved.
One other observation worthy of note is that the internal resistance resistance of the cells is highly dependent on the state of charge. The effect of temperature and SOC seem to add together to influence the overall internal resistance.