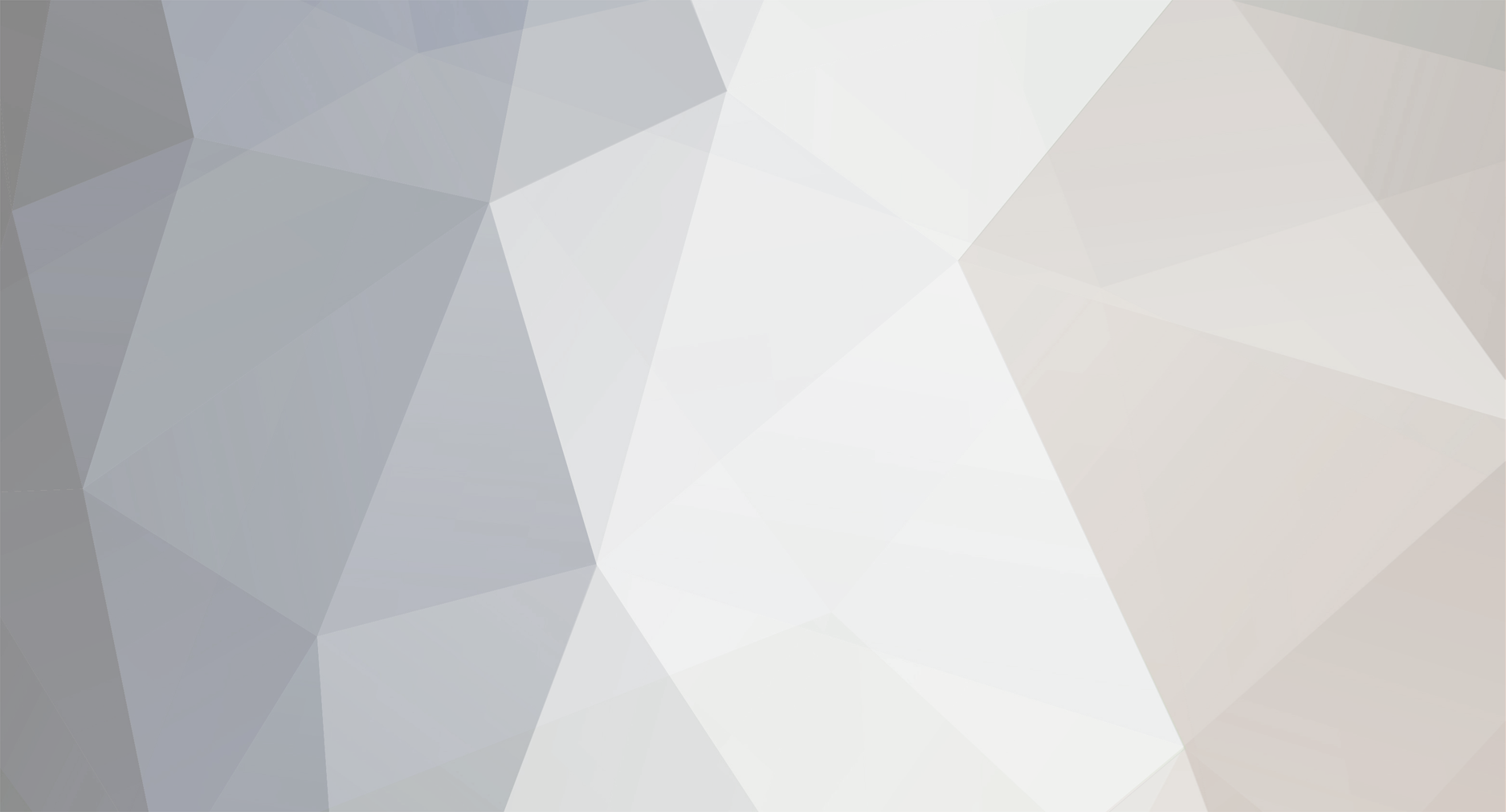
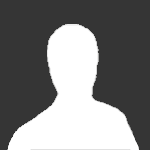
Split Pin
-
Posts
235 -
Joined
-
Last visited
Content Type
Profiles
Forums
Events
Gallery
Blogs
Store
Posts posted by Split Pin
-
-
-
I spoke to Malcolm Braine last night, he remembers a company called either Dami or Dani located in Stockport producing some boats in the early 1960's, maybe ties up with the previous post.
He also mentioned some boats built by a company called Halmo, also known as Halesowen Motor Company by anyone living in the West Midlands , one of the owners /directors was involved with the Avon restoration, although this was probably nearer the mid 60's
Steve
-
Hi Glenn
Yes I know Micheal. He kept the boat at Stourbridge, and is a member of the Staffs & Worcs canal society, both of which I am associated with.
Interestingly my brother had tried to purchase Golitah but Michael had beaten him to it.
Had I checked the EXIF info for the photo and not relied on memory I would have got the time correct. It was taken on 21 September last year at 9.42am
Steve
-
-
Yes, The Merry Hill shopping center is built partially on what was called the new level mill of Round Oak Steel Works. The photograph is taken from just through Greens Bridge heading for Park Head, next to where The Brewers Wharf hostelry is now The water intake for the water used in the mills is on the right of the photographer. The cleaned water was returned through a filtration system on the left through the bridge in the picture. In the late 50,s through to the late 70's the canal had a permanent film of oil. Delph top lock had a permanent coating of sticky oil. What is now often refereed to as the Marina at Merry Hill was originally a wider section where the filtration plant was located. When Merry hill was constructed the canal was realigned. During the redevelopment the bank retaining the canal was undermined which lead to the canal being closed as it was no longer safe. There was some speculation that the developer was trying to get the canal closed.
The Pensnett railway company was integrated into the internal railway within the steel works and was still in used until the 1980's, I remember seeing steam locomotives on there, they ran until the early 1960's. How long the livery would have remained on the trucks is anyone's guess.
Steve
-
Starts at around 52 min. Interestingly the 1L2 is an anticlockwise version.
When Trinity house decommissioned the lightships many of the 2/3 cyl engines found their way into narrow boats.
Steve
-
I have a 50ft narrow boat with a 3LW PRM 2:1 and 23" X 23" prop. The B.A.R of the prop is around the 60% mark, this is more commonly known as a compensated prop. A standard being 45-50% Max revs are limited to about 1100rpm, normal running speed is 475/500rpm on narrow canals 6-700rpm on Northern waterways. 7-750rpm on tidal rivers. anything more is purely just moving water for no great gain. Slow running i.e passing moored boats is at 350-375rpm. I originally had a 24" X 18" 50% B.A.R blade fitted, normal running was 600rpm and stopping was poor.
All LW's can have there tick over reduced to 330rpm by fitting a different rack spring. This was detailed in a service bulletin A.I 160 issued in February 1952Gardner's recommended prop dia for a 3LW with 2:1 gearbox is 27"
Steve
-
41 minutes ago, Athy said:
Thanks, Steve. In a post a few years ago you mentioned how to interpret this pattern number: something to do with the date in reverse order? So, obviously this one would not mean 3/8/94, as 2LWs were not being made in 1994 (I know they were revived later in the '90s but this appears to be an old one). Could it mean 3/8/49?
I did not notice an engine number - but then I have never noticed one on my own 2LW either!
The post that you mention most likely refers to a different number. Each crankcase was pressure tested before being used, the date of the pressure test was stamped on the crankcase usually on the rear face as per the picture , this one is dated 1/11/51 and was tested as a completed engine in May 1952.
On painted cast iron engines the serial number tends to get obscured by the paint job so unless you go looking it is not always easy to spot, and if it was a South African engine it may have even been altered.
Steve
picture
-
The numbers cast in the side of the block are pattern numbers and should be on all LW blocks with slight variations in numbers between 2 and 3cly blocks and possibly of different ages when there has been a modification to the pattern, and or batches of castings for identification later.
The engine number should be stamped into the top of the crankcase just behind the injection pump next to the front cyl block holding down stud, if the engine has many layers of paint it is probably obscured, the injector pump should also have a number either on a plate or stamped on which matches the engine number, assuming its the original pump to the engine.
The number stenciled on is probably a plant number as you suspect, I have seen ex Trinity House engine's painted green so maybe one from there.
If you can find out the engine number then it should be possible to find more information by asking the Anson Engine Museum to check the records (small fee)or maybe Martyn can help.
Steve
-
Well done Ray, I must have missed this first time around.
Looking at all those people stuffed onto old coal boats regardless of DTI regs, and no life jackets.
Little cruisers with petrol outboards no secondary escape hatches and portable stoves ..... all without a single Safety Certificate in sight.
One can only assume they must have died in their hundreds on that day. Or perhaps common sense and personal responsibility were more embraced?
At least one made it back out as I am still here to testify.
Sadly most of the contributors are no longer around to share their memories and wisdom.
We owe a great deal to them and other enthusiasts of that time without which there would be considerably less of the current network available for cruising.
Steve
-
When I came past in April this year the demolition crew was busy removing the buildings, so probably nothing left of the offices now.
Used to feel like a little oasis in the middle of the industrial conurbation, another sad loss.
Steve
-
Acr alternators were never more than 45A but if that is enough I can easily get you that at tick over with a modified alternator.
I have a Lucas publication from about 1990 that list the ACR range from 15ACR - 28A up to 25ACR - 65A.
Never came across anything above the 22ACR - 45A though.
I had an 18ACR with an Adverc controller fitted for about 25 years, worked well except that the front bearing life was poor.
The 3/8 in (9mm) blade is rated by Lucas at 35A maximum so anything bigger needs to use both blades
Steve
-
2
-
-
The clip starts 29 mins in, I suspect that the 9.43 mentioned in the earlier post is the real time showing,
Nice little piece and a bit of good publicity well done to all concerned
Steve
-
They look like Worcester windows, the company has changed hands at least once.since 1999
This is I think is the current company http://www.narrowboatwindows.co.uk/
Steve
-
I'd like to be able to see the current that my 240V appliances are using, eg the washing machine (on cold wash). Is there any reason why I should not just wire in one of these things in the 240V line from the inverter?
http://uk.rs-online.com/web/p/analogue-panel-ammeters/8861831/
I have one similar fitted as your question, different scale but does the job.
I also monitor the battery current and voltage as well.
Steve
-
`Looks like Hillman Imp Drive shaft coupling doughnut, particularly as the gearbox end looks to be fabricated from the end of a drive shaft./
one source of supply from a google
http://www.mevspares.co.uk/RUBBER-DOUGHNUTS-x2-Hillman-Imp.html
Steve
edit to add link
-
Just downloaded a boaters guide and this information is copied from itFoxton Locks
Winter opening times for 2016/17,
Opening Times(19Sep16-16Mar17):
Foxton Locks Winter opening times for 2016/17 have been confirmed.
19 September 2016- 23 October 2016 Mon- Thurs, 8:00am to 4:00pm (last boat in 3:15pm)Fri- Sun, 9:00am to 5:00pm (last boat in 4:15pm)
24 October 2016;-16 March 2017 Mon - Thurs, 9:00am to 3:30pm (last boat in 2:45pm) Fri-Sun, 9:00am to 3:30pm(last boat in 2:45pm)
As locks can be very busy, please allow yourself plenty of time to ensure passage It takes approximately 45minutesto pass through the flight and you must
be through the flight byt he time of closure. Last boat will be allowed through the lock 45 minutes prior to closureJust downloaded a boater guide and theses are from it.
Seems to me that they decided not to allow anyone to start up despite the fact that they could have passed in the middle and still made it out before closing time.
Steve
-
Those numbers don't fit the standard formulae. OD =N+2/DP
SO at 8DP the OD should be 22.125 in or at 10DP the OD should be 17.70 in.
Alternatovely for a 20.00in OD there should be either 198 teeth or158Teeth.
Since I am sure the info given is correct, I suspect that the ring gear tooth form is not a standard involute gear
You live and learn. Is this common to other ring gears?
The odd tooth form will also apply to the pinion and means that cutting a new pinoon is a rather more ticklish job than it first appears.
N
Thanks to Martyn for the tooth designation description.
Having looked it up in Machinery's Handbook it becomes a little easier to understand, the OD is calculated as an 8DP standard involute tooth as per the calculation, giving the OD as 22.125"
As I have one to hand I measured it at 22.080, so give a little bit of manufacturing tolerance is correct.
The tooth form and depth is calculated from the 10DP giving a narrower tooth form.
The pressure angle is 20 Degrees as with current convention
Interestingly my 26th Edition of Machinery's Handbook published in 2000 refers me back to the 18th edition for further details saying that it is a seldom used tooth profile.
The 18th edition was published in 1969, so it has been out of general use for some years now
Maudesmaster is the sensor that you have ordered one specifically for picking up the edge of tooth profiles?, most sensors have a specified target size, if it is to large then it will not be able to detect the gap between the teeth and will give you a constant output as it will see the next tooth before the last one has passed.
Steve
-
Like other engine builders I spread the ring gaps around as per manufacturers manuals, I was pointed to this article some time ago.
Enjoy the read and come to your own conclusion
Ring Gaps vs Knowledge Gaps
During school summer holidays there occurs a period known as the "silly season" when breaking news is slack and newspapers, radio and TV issue forth all sorts of drivel to justify their existence. In our industry I sometimes think that we use ring gaps to fulfil a similar purpose – and we do it all year round. There are more old wives tales about ring gaps than any other facet of our job, so lets spend a while and bin a few of them.
Frequently I hear in court that when an engine is dismantled it is discovered that the ring gaps were not staggered when they were installed. Frequently I read workshop manuals that go into great detail on the necessity to stagger ring gaps. Frequently these manuals specify ring gap limits – which is yet another myth we can bin before we are finished.
In days gone by, some compression rings used to have a ‘threepenny bit’ expander behind them. These braced against the base of the ring groove and forced the ring onto the cylinder bore but these are very much the technology of yesteryear and, as such, an exception to what I am about to say.
Piston rings are free agents and can rotate or not rotate as they see fit. They are not in touch with the base of the groove and neither are they trapped between the upper and lower faces of the groove. The rings are entirely free to rotate – except where a stop peg is fitted – so what's the point in staggering the gaps on installation?
We used to work on a minimum of 0.020" back clearance on radius or, to put it another way, the inside diameter of the ring when installed in the cylinder must be at least 0.040" bigger than the groove root diameter. Minimum side clearance was generally held to be 0.0015" and if you could fit a 0.006" feeler gauge in the groove along with the new ring then the groove was "goosed" so the piston was replaced.
The piston ring was manufactured with a tangential load – the force with which the ring presses against the cylinder wall – but apart from that it is completely uncontrolled. There is no way, under these circumstances, that you could prevent the ring from turning so, to repeat the question, why stagger the ring gaps on installation?
Staggering ring gaps when installing pistons is every bit as daft as having four tyres fitted and placing all the valves at "twelve o'clock". One trip to Tesco and they end up all over the place.
Equally daft are those who expect ring gaps to stay staggered when the engine is in operation. When there is clearly nothing to prevent the ring from rotating, why should the gaps stay staggered?
More than one county court judge has fallen for the hocus pocus that because the gaps were in line when the engine was dismantled, they must have been in line when installed. Absolute poppycock! Yet the inclusion of such rubbish in workshop manuals does admittedly give it an air of authority. When you think about it, you don't need me to tell you – but I will anyhow – that rings do rotate in operation. Every now and again the gaps do line up – and once lined up there is a tendency for them to stay lined up at least until the vehicle hits the next pothole in the road when one or other will rotate and break the line. Staggering ring gaps when installing rings is a myth that we can bin forthwith. Even worse is the preoccupation with the size of the ring gap. Yes, there is a minimum but this varies considerably depending on the material used. Normally 0.003"/0.004" per inch of bore size is given but where, for example, low expansion SG (spheroidal graphite) iron is used, it can be considerably less.
It’s no problem if the gap is too small because it can, in the final analysis, be filed bigger but what do you do if it's too big? You cannot stick a bit extra in there! Well, the answer to that was that you melted them down and started afresh – until AE research asked the question, "What is too big?" and set out to quantify that. The results were interesting – very interesting – and what you are about to read was kept quiet because it bestowed an enormous commercial advantage on AE. This is probably the first time the information has been published although the research was undertaken in the late 1970's – almost 25 years ago. A Ford Kent engine was stripped and fitted with compression rings which had end gaps of 0.015" when fitted in the bores. The engine was wired up with the usual telemetry to measure blow-by and oil consumption and then run in one of the test cells. After making due note of the blow-by and oil consumption, the engine was stripped and fitted with new compression rings with gaps of 0.025" and the test cycle repeated. These rings were subsequently replaced by ones having end gaps of 0.035" and the test cycle repeated again. It had been planned to stop at 0.035" gaps ----------> but the results were so interesting that it was agreed to proceed to 0.045” and then not to 0.0055” but to 0.0625” – 1/16"! Whoever heard of rings with 1/16” gaps – a ridiculous figure – but the interesting thing was that the increase in blow-by and oil consumption at 0.0625” was only marginally above the figures obtained with 0.015” gaps. Practical tests established that the gap was not the villain of the peace. To all practical purposes the size of the gap didn’t matter. It is important to stress at this point that we were dealing with compression rings that were brand new when fitted to the test engine. The gap was specially manufactured for the tests. So how come all oil burners and heavy breathers have ring gaps you can back a bus through? Well, the tangential load that the ring exerts onto the cylinder wall is a direct function of its radial thickness. As the periphery wears in contact with the bore, the radial thickness obviously decreases, as does the tangential load. Peripheral wear means a smaller ring o/d and this manifests itself as an increase in the ring gap. So, whilst all oil burners and heavy breathers have big ring gaps, it's not the gap but the reduced tangential load that is detrimental to the performance of the engine. The ring gap is a complete red herring.
Imagine four top compression rings all with 1/16” gaps. The total gap for all four would be 1/4”. Now imagine the seal provided in an 80 mm diameter bore. Pi x Diameter = Circumference, so we have 3.14” x 3.15” = 9.891”. Multiply that by four cylinders and we have 39.564” – over a yard of contact seal between piston rings and bore. Now visualise the many litres of blow-by and consider whether all the gas is squeezing through 1/4” of total gaps or passing through 39½” of reduced pressure contact seal!
But even this ignores one important facet of the argument because there is not just the one compression ring on a piston – there are usually at least two and that is because rings work as a team to form a labyrinth seal. For gaps to be the villain of the peace, the gas would have to find the gap in the top compression ring and pass through. It would then have to circulate to find the gap in the second ring and pass through that and so on. Now this may be possible if the power stroke lasts for 10 minutes but it doesn't, does it?
At 3,000 rpm the power stroke duration is a mere 1/100second. Quite simply, the power stroke does not last long enough for the combustion gas to find its way around the maze – or labyrinth seal, so the villain of the peace has to be the reduced tangential load of the ring on the bore caused by peripheral wear or reduced radial thickness of the ring.
This was our hypothesis based on the results obtained in the engine test cell but it took a very clever American to prove it. This genius invented telemetry that measured gas pressure between the piston rings in a working engine.
Use of his brainchild revealed that some gas did get through the top ring gap sufficient to generate a hell of a pressure between the top and second rings – so it clearly was not finding the gap in the second ring. The labyrinth was working well. Caterpillar and IHC must have thought it was working too well because they increased some second ring gaps to 0.050” and 0.070” thought to be beneficial.
Come to think of it, the exception proves the rule – as usual. Two stroke engines would not need stop pegs to prevent the end gap from crossing a port if the ring didn't rotate. The people who allege that ring gaps were not staggered when installed just because they are in line when the engine is dismantled don't need stop pegs.
They could simply position the end gap away from the port and expect it to stay there – and we all know that this would get them into more hot water than a Yorkshireman’s tea bag! So why do they always blurt out their rubbish on the importance of staggering gaps?
The very presence of a stop peg also proves my point about the size of ring gaps. Where a peg is fitted, the end gap has got to be 1/8” to accommodate the peg. There would be one hell of a draught through that if the 0.015”/0.018” boys were correct.
This knowledge was commercial dynamite because, instead of the '0.015”/0.018” spec., it meant that new rings with gaps over 0.018” could be used without any detriment to the engine's performance. The gap was only detrimental when it was the result of peripheral wear. Customer acceptance was the only problem. To re-educate the customer would let the cat out of the bag, thereby losing the distinct commercial advantage. It was decided, therefore, to accept rings with gaps of up to 0.030” in a nominal bore but even then there were arguments. 0.030" in a nominal bore is 0.045” in a bore worn by 0.005” – and it's normally engines with this sort of wear that get new rings. The gaps on the new rings were bigger than the gaps on the ones being replaced which led to several heated conversations – and how the hell do you pacify the customer and keep the cat in the bag? It made diagnostics a lot harder too because when all rings set off in the 0.015”/0.018” area gaps of .040” meant something but now, when you don't know what they set off at, what they measure is meaningless. Well, now you know. All rings are free agents to rotate as they like, making staggering of gaps on installation a joke and ring gaps are not a problem provided that the gap is not the manifestation of reduced ring radial thickness caused by peripheral wear.
In the light of the logic expressed in this article we are offering an expensive prize to anyone who gives us a good reason for staggering ring gaps on installation – a free burial at sea.
M H Booth F.I.Diag.ECopied from http://www.diagnosticengineers.org/journal_%20articles/Ring%20Gaps%20vs%20Knowledge%20Gaps.php
Steve
-
2
-
-
Gardner's recommendation is that 100 ampere-hours at the 10 hour rate is sufficient for starting purposes.
I used 110 ampere-hours battery on a 12 volt system for many years, now use 2 X 110 ampere-hours battery's on 24V system.
Steve
-
The rotor is £58.40 + Vat,
-
-
Not of any use to Bernard for Enterprise spares as she has a 5L2 fitted
-
These used to be commonly used in industrial installations on 3 phase circuits, normally in an insulated box http://www.cablecraft.co.uk/line-taps-for-branch-joints-10mm.html
Any good industrial electrical wholesalers should have them.
Steve
4LW starter battery size
in Gardner
Posted
Depends on which manual you look at. My quote is from No 67, (which I believe is the last version published) it does mention that it my need to refining depending on the amount of electrics on the vehicle.
Not normally an issue for a dedicated start battery on a boat. It does only give one size
Steve