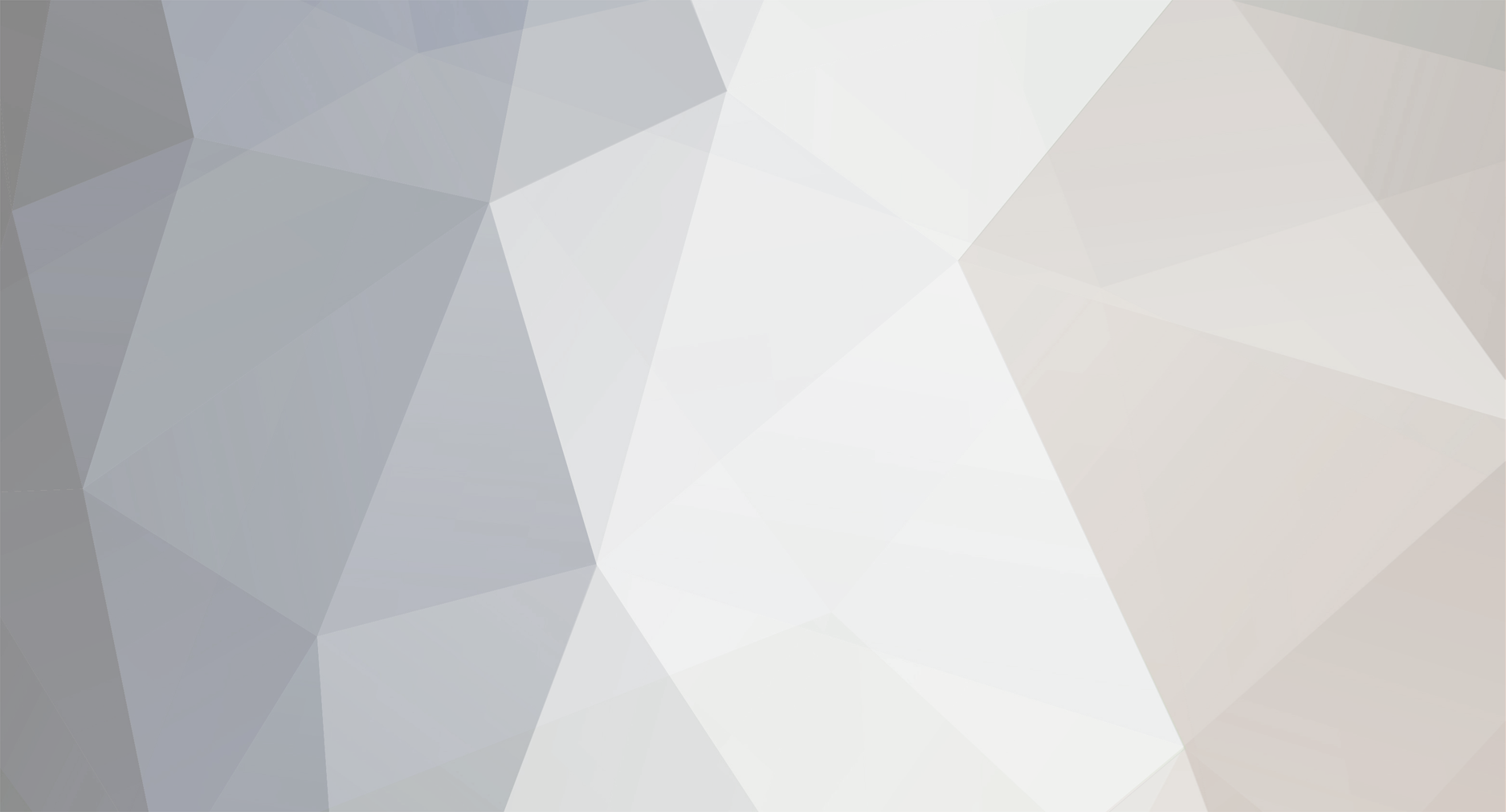
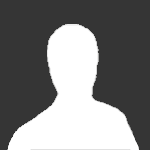
Slow and Steady
Member-
Posts
538 -
Joined
-
Last visited
Content Type
Profiles
Forums
Events
Gallery
Blogs
Store
Everything posted by Slow and Steady
-
Re-insulating liveaboard bit by bit
Slow and Steady replied to Slow and Steady's topic in Boat Building & Maintenance
I suspect the problem may have many aspects for example the gluing, the fact it hasn't expanded as the makers claim, air getting in behind the panels as the panel fixing glue has deteriorated and quite possibly less than complete coverage. Whatever, it does need an overhaul and despite others having success with it my own view is not favourable. I appreciate that any insulation system succeeds or fails on the quality of it's installation and a narrowboat being a steel box makes the symptoms of failure severe. This boat has quite a few defects that would have taken a few more hours to do properly but will take days or weeks to correct. Another is the hull builder built the correct sq m of skin tanks but the engine installer connected only one of the two, then the interior fitter built permanently over it's air bleed - not even an access hatch to it. Connecting the second tank requires bigger connections than installed and due to the engine being in the way, access to the lower one is impossible without removing the engine first. That is... annoying - it's a Beta 43 so quite a chunk of a thing. Meanwhile I cannot venture onto a river. All for the sake of a few hours extra work when the boat was built. I think I may be able to gain enough access by lifting one end of the engine with a block and tackle, but I'll be surely cursing the lazy arze builder throughout. If I was 30 instead of being in my 60's I'd probably just get on with it but these things are not as much un as they used to be. -
Re-insulating liveaboard bit by bit
Slow and Steady replied to Slow and Steady's topic in Boat Building & Maintenance
Mulling it over, perhaps I can do as Linnet's photo earlier, then re-use my thinsulate to fill the resultant recessed panels. Thinsulate maybe an ok product but I fail to see how it can be used alone AND create a vapour barrier plus it's only ever advertised as an acoustic insulator - 3M do not provide any thermal spec for it. It's supposed to expand to 42mm thick, but where I can see mine as per my photo, it definitely has not expanded to anywhere near that claim, more like 15mm or 20mm if I was being kind. Considering the upheaval and PITA this job will be, what I'm thinking right now is that rebuilding it as it is/was would be a massive waste of effort. -
Re-insulating liveaboard bit by bit
Slow and Steady replied to Slow and Steady's topic in Boat Building & Maintenance
Fortunately it's at the shallow end of roof curves. -
Re-insulating liveaboard bit by bit
Slow and Steady replied to Slow and Steady's topic in Boat Building & Maintenance
Well, nothing is decided and I am listening. I'll see what's what when I start to dismantle the panels and if the cause of my problems seems to be something else or bad fitting then I may indeed reuse it, I'm not keen on spending money unnecessarily but really - I do not think it a recoverable product if it's glued in place? At this point I'm considering my options and getting advice and opinions including yours which I'm grateful for. I restored and mechaniced old vehicles for a living for a while and if there was one thing I learned it was not to pre-order parts on guesswork - I really will not make a decision without having a damn good look first and that will include trying to remove some if it needs removing and seeing if it can be reinstalled - this is something I would not have tried without this discussion and enlightenment about the thinsulate currently fitted. Thanks again for your advice. -
Re-insulating liveaboard bit by bit
Slow and Steady replied to Slow and Steady's topic in Boat Building & Maintenance
I think this is where spray foam wins? It's not suitable for us, but does cover the steel and get in every nook and cranny. As said earlier I have insulated a large wooden building in this way, taping all the joints to form a vapour barrier then panelling it out but a steel box is another thing altogether isn't it? But I know it can be done and I have the determination and experience to at least know to not cut corners. Maybe... but I have a sort of thing about it now! Perhaps when I start to dismantle I'll change my mind. Also if it's kind of half-baked glued on I'm likely to destroy it removing it - all that work I think I'd be more content to do it completely differently. -
Re-insulating liveaboard bit by bit
Slow and Steady replied to Slow and Steady's topic in Boat Building & Maintenance
Great minds think alike... or something... that process is exactly how I see it going - 2 boards off fix the first, remove the third, fix the second and onwards. Damn shame the boards are so big, if they were 4ft the job would be so much more containable! Really - zero storage, I'm 200 miles away from anyone I know from my past that lives in a house... and I have no transport so not worth renting storage - can't drive to a medical condition or I'd buy a temporary van which I could fetch and store materials in. Probably my best option, if I were a barsteward, would be clean up and paint over the mould, sell it and buy a good one. It's worth considering. Or.. buy a small one to live in while we work and sell it on after, the prices are only going up... -
Re-insulating liveaboard bit by bit
Slow and Steady replied to Slow and Steady's topic in Boat Building & Maintenance
Sigh, it's such a shame when a boat is built with good intentions but somewhere along the line goes over budget and the only savings possibilities are from doing it faster. I know a couple were built at the same time using different hull builders and my hull built by a steel constructor who though extremely good had never built a narrowboat and I know the builder and steelwork firm fell out big-time over it. I think that's where it went awry and over budget. The boat was built to make a profit for a marina owner who was by all accounts not a nice person. It's not hard to imagine that he would have put pressure on the fitout people to come up with a cheap price or imagine that he bought the materials for both boats himself, in bulk prior. I've done a lot of digging into the boat history including going to see the hull builder but i can't find out who did the fitout - it would be interesting to talk to them. Taking on board that the thinsulate, despite being marketed as a sound insulation, is ok stuff, I'm thinking the main problem I have started when the the no more nails type glue started to disintegrate allowing air to get in behind the panels. Hmm. Well, at least I know something NOT to do when I finally get to putting it back together.. I wonder how the battens are fixed to the hull? Anyone know how this is normally done? I've always wondered. -
Re-insulating liveaboard bit by bit
Slow and Steady replied to Slow and Steady's topic in Boat Building & Maintenance
Interesting. Thanks for identifying it. Hope it wasn't you guys who did my boat! I have to say my boat is constructed with very good materials and spec all round, from the electrics to the engine to the hull and the fitout. The problems stem from the cheaping out on the labour fitting it out. It's interesting to read that you have a positive view of the insulation. That being said, why would you think I have the problems that I do? I know you can only guess but an educated guess is better than I can do. I'm quite looking forward to removing some of the lining and finding out exactly what's been going on but until then... -
Re-insulating liveaboard bit by bit
Slow and Steady replied to Slow and Steady's topic in Boat Building & Maintenance
Brilliant, real life advice - do you inhabit your boat through the winter? I think this makes all the difference, for 9 months of the year we have no problem at all, then... bosh - dripping. I suspect if we weren't here and left a couple of windows open it would stay dry. -
Re-insulating liveaboard bit by bit
Slow and Steady replied to Slow and Steady's topic in Boat Building & Maintenance
Right - so does the team think 1" will be enough? That would REALLY help with the window and porthole surrounds and general refit of all the woodwork, but if more would be better... -
Re-insulating liveaboard bit by bit
Slow and Steady replied to Slow and Steady's topic in Boat Building & Maintenance
Damn. this is going to be a PITA, I'm going to have to buy the Kingspan/3M or whatever a bit at a time due to lack of storage so no bulk deals either. Oh well! I'm intending to re-use the ply paneling if I can and paint it if I ruin it's good looks, which I no doubt will. One good thing is that it must be "proper stuff" and it's not delaminating or warping despite the conditions. My god, the price of oak faced marine ply with a decent thick veneer is ... high... and there are acres of it. I'm not intending to do anything with the floor but I have had some of it up previously - looking good and bone dry under there. I have an inspection hatch at the back and from the pieces I've had up there is nothing to stop any water making it's way back there. The floor supports have gaps at the ends - at least that's one thing done correctly. Hi all - thank you all so much for your replies and advice, I feel like a plan coming together and it's so nice to get this off my chest so to speak. -
Re-insulating liveaboard bit by bit
Slow and Steady replied to Slow and Steady's topic in Boat Building & Maintenance
Thanks again, I've checked under the floor, it's just about the only place this boat is dry!!! For sure the low level ventilation is a big part of the problem. I do recognise this and it's part of the plan. I won't be doing any work until the spring so for the rest of this winter will just have to cope as best we can and be ready to hit the ground running so to speak when the weather warms up a bit. As noted, with the damp at this time of year nothing is going to stick well... apart from spray foam. That looks like mine will in my dreams. I see there must be air gaps under the wood lining? Is this considered "ok"? I guess it should be fine as long as air cannot circulated through them? Over the battens, is that just thin ali tape or is it insulating type stuff? Thanks for posting the photo. -
Re-insulating liveaboard bit by bit
Slow and Steady replied to Slow and Steady's topic in Boat Building & Maintenance
Thanks for the tip, I think you're right and it's the foil that stops it bending. Yes you're correct about the ventilation, I posted about that as you were typing - just above your post. This is something I will tackle along with the refit as I will be able to build in some low level ducting as I go. In at the bottom, out at the top. Yes I'm sure about the roof, I painted it myself with all the fittings off and sealed them and every screw when I refitted. It's amazing how much water can get in through the tiniest crack - I had a nav light off the side and one screw hole let it LOADS until I stopped it. -
Re-insulating liveaboard bit by bit
Slow and Steady replied to Slow and Steady's topic in Boat Building & Maintenance
Got to admit also that without a handy cratch door the air flow in here is poor. Getting air in at low level is nigh on impossible. To that end I have built in a ducted inlet opposite the stove that does (probably) help a little, but with the really poor thermal insulation it's all too tempting to keep the windows shut. We do have mushroom vents but to illustrate the ventilation situation, cold air often blasts IN from them when I know it should be going out - one is directly over my head in bed and I often block it up because of this. It's a perfect storm isn't it. I feel like one of those poor people who can't afford heating, keeps all the windows shut and wonders why their home is going mouldy. In my case I can afford the heating but it's just not enough due to the poor insulation. My previous boat was self fitted out by someone who did a fantastic job, it was warm and toasty and DRY - I know it can be done. -
Re-insulating liveaboard bit by bit
Slow and Steady replied to Slow and Steady's topic in Boat Building & Maintenance
I do have a dehumidifier...it can't keep up. The rot and white mould is visually apparent eve on ceiling panels. I know it's condensation as it runs inside of the wall panels until it hits horizontal battens (or whatever the panels are fixed to) then soaks out through the ply. The back of the ply will be untreated, this was a slap together and run job, though the craftsmanship of the woodwork is excellent in itself so clearly done by someone skilled.. but in a hell f a hurry. Whatever they used on the interior side of the panels and woodwork I think was one coat and sprayed after all the chippy work was complete. The modern world eh? Ref kingspan, not very Flexible is it? Really - not at all flexible, I have used it before in a summerhouse/office I built. My worry would be that on the ceiling it would slowly straighten itself out and delaminate leaving the silver backing stuck to the ceiling? Any thoughts? I would take a photo of the worst mouldy bit and post if I could get past my embarrassment of how BAD it is! Maybe later. -
Hi everyone, first post so go easy on me! Background: For my sins I have a 60ft narrowboat that I live on with my grown up son. We kind of look after each other. We bought the boat in a hurry 4 years ago, I had a smaller REALLY NICE one but we had to expand when my son suddenly had to join me. So... we chose this one because of it's layout - he lives at one end in a sort of bachelor pad that was a 15ft bedroom, I live at the other end with a living room c/w solid fuel stove, galley and walkthrough bathroom between. The front has a sort of bay window instead of a cratch, the rear has an engine room and small steering deck. I'd call it a trad... but it's not really, it's a flat on water, I don't think it was ever really intended to be much of a boat, it's not boaty if you know what I mean. It was obviously "designed" to have a large open interior and so the panelling is not deep and the insulation is terrible - not in terms of heat (though that isn't very good) as much as condensation. It's been insulated with fluffy stuff off a roll, black one side, white on the other about an inch thick. I don't know exactly what it is but here's a photo so you get the idea, fag papers for scale. That's it - that is all we have for insulation! It was glued-ish to the steel but... like everything else in this naughty boat it's coming adrift. The whole fitout has been constructed with no more nails and pins to hold it in place while it set. Bulkheads fixed in place with those plastic blocks used in kitchen cabinets. 15 years later it's falling to pieces. A real shame as it's good quality oak faced ply and oak trim. Because it's falling to pieces, air is able to circulate behind the panels, condensation forms against the steel, it's BAD, it's dripping, it's going mouldy in a big way, the boat smells of rotting wood. There really is only one thing for it - start again. Now, what I'd really like to do is strip the entire interior, spray foam it and rebuild. There are a number of things that make this impractical - we live on it, we have nowhere to store things, we have no transport, we're quite poor and need to get max value from spending. With the above in mind it seems like our only approach would be to start at one end and do the job in chunks. It's not going to be straightforward room by room either as the bulkheads are all partway along the lining ply sheets, it's wired and plumbed and we don't want to rewire etc etc. The one thing we do have is time, lots of time. That's where we are, the boat is not sellable like it is, the layout is perfect for us, it has a beta engine that's barely past it's first oil change hours!, it has good elec fitout with travel power, webasto central heating etc etc, so it's not all doom and gloom. The steelwork and welding is top notch in good order, 2 pac "blacking". It would be a great home/boat if not for the poor insulation situation. Here's the question - if you were in this position, what insulation would you install? It seems to me essential that no air is permitted to get at the steel in order to stop that condensation, we'd be happy if the space inside got smaller in the process and whatever we do must be a permanent solutio with much better thermal properties than the skinny stuff above. Cost of materials? Well it matters, but with the effort involved it's secondary to the result - if it'll help it will be purchased. I'm handy with DIY, I have lots and lots of tools. In fact, tools are about all I do own apart from clothes! Thanks for reading this long first post. I'm a long time lurker here so I thought I'd just wade in. No - we're not planning on bridge hopping, moving to London, CCing in one sq mile etc etc. We have always had marina mooring but we need to get this boat sorted while we're here and then we'll be off on a real open ended cruise to see where it takes us.