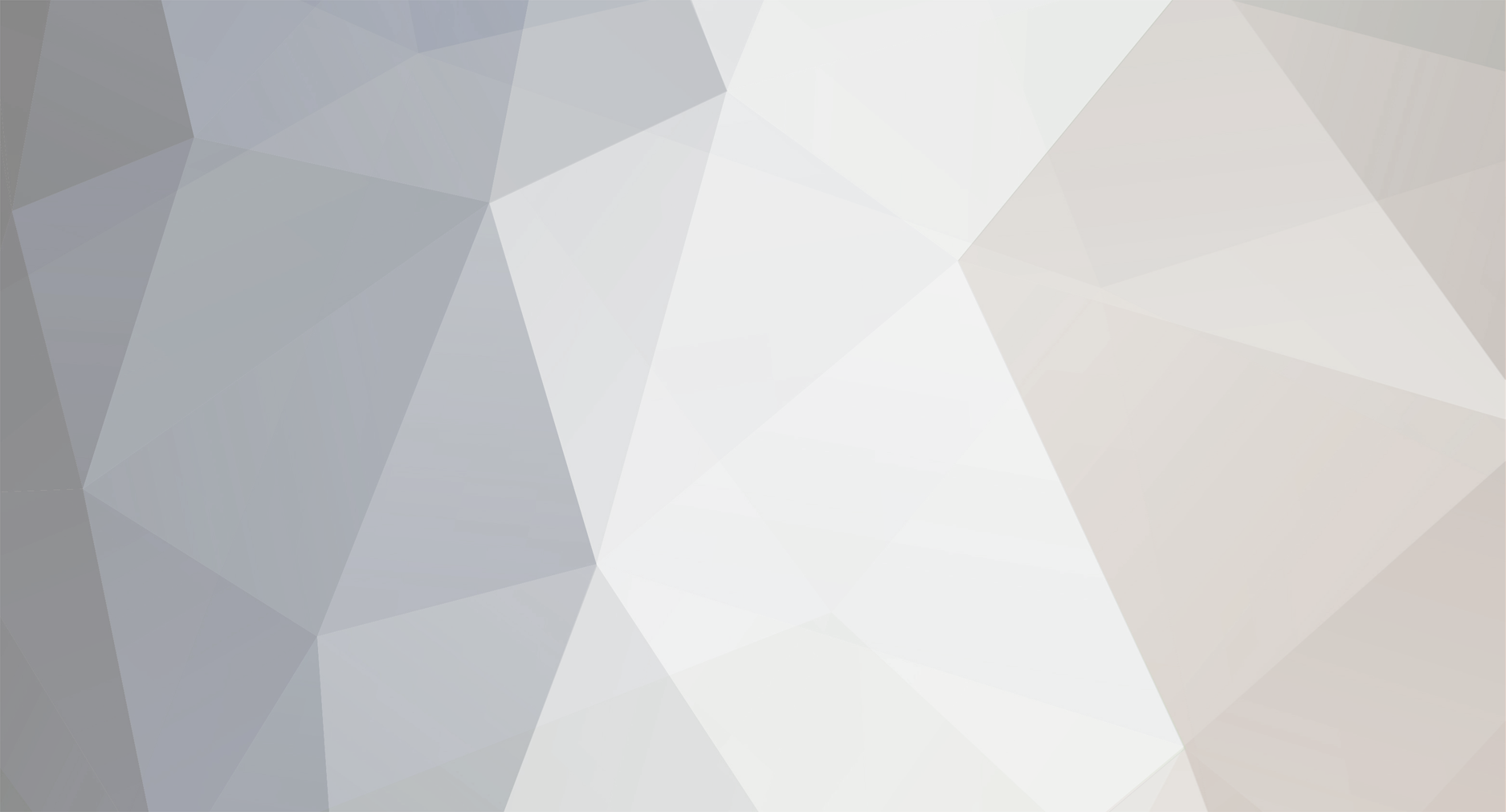
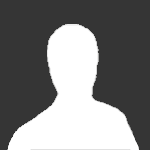
simonebb
-
Posts
56 -
Joined
-
Last visited
Content Type
Profiles
Forums
Events
Gallery
Blogs
Store
Posts posted by simonebb
-
-
If there is no other way then use 'double' clips (ie two x jubilee clips) to minimise the chance of the hose coming off - I think because of the risk there is something I the BSS about 'double clipping'
Edit : I cannot see anything in the latest BSS about 'double clipping' but I'm sure it was mentioned to me during a BSS inspection.
Hi Alan do you know of any alternatives to jubilee clips, I will certaily go for double clipping but even that doesn't fill me with confidence
-
What height above the waterline is the skin fitting ?
Is the 2" length of pipe plastic, brass, copper ???????
Is the 2" length of pipe standard 'waste pipe' ? If so maybe you could solvent weld more of the same and connect to your sink.
The problem with connecting to a smooth pipe is that when hot water goes down the sink it can soften some plastics, &/or rubber hoses. If you are relying on (say) jubilee clips then it is possible that these can allow the 'softened' pipe to come off the fitting.
If this happens and your fitting is close to the water line then you could have water getting into the boat - potentially enough to sink it.
Ideally your hull fitting should be 10" Or more above the water line - some are less but you then have to think of ways of ensuring no water ingress - eg
Is there enough space / height to install a 'swan-neck' into the pipe ?
The pipe is copper, the skin fitting is 10" above the waterline BUT the boat is currently moored on a tidal river and at high tide on a rough day the waves breach the pipe (both outlets currently have rubber bungs in them)
I am not sure about the swan neck will have to double check height of sink outlet but presumably this would prevent water ingress - assuming hoses havent fallen off!
-
If you are fitting a hose over onto the 2'' long bit of pipe with no thread on it make sure the end of it is internally chamfered or muck will keep building up on a the flow facing ridge and you'll be forever using the plunger. If there's no chamfer I'd file one.
Thanks Bizzard will do.
presumably i could safely attach the hose with a jubilee clip?
-
Hi All,
I am trying to install a sink and have two existing skin fittings on my boat that could serve as waste water outlets, however the internal fitting appears to be just a 2" length of standard piece of pipe (no thread) approx size 19mm/ 3/4".
Is this normal?
Could i use a hose connector
and flexible hose pipe to provide an outlet from the sink? if so is brass or plastic better.
Or is there a better way to do this?
Thanks in advance
Simone
-
Hi All,
Am about to install a new lighting system and am looking at LEd lights, I know from here that most people rate Bedazzled but for a whole new system this is quite pricey. I have found some sold by Central Waterways Uk that are £9.50 a pop
http://www.centralwaterways.uk/index.php?dispatch=products.view&product_id=1038
they are apparently spike protected but do not have an internal fuse as beddazzled do.
So 2 questions : has anybody used these?
How important is the internal fuse?
Many thanks
Simone
-
Thanks everyone!
Some really interesting, helpful and creative suggestions ... I will let you know what we decide to do.
-
I'm not a fan of grinders but have had to use mine a lot recently ! Might well get someone to cut them off and then finish them off myself with a grinding disc, alternatively if they are as lightly welded as the rest of the boat I might just be able to remove the weld and tap them out!Ground off? I think they will have to be cut off with a cutting disc and then the rough edges ground flush with a grinding disc and lapping disc.
If the OP is not confident with an angle grinder then this is not a job I would encourage her to do herself, but assuming there are four or five tunnels then somebody who knows what they are doing should be able to cut them off and grind them flush within a couple of hours. Just make sure they don't cut through the roof!
On a related matter, the cabin is predominately 3 mm, consequently any remedial welding causes it to curtain, also welding a plate in the roof repair a hole has made the roof dip, has anyone else experienced this, if so any tips?
Linked to the photos for you.
Thank you!
-
Int dia = 105 mmThanks for the pics.....
Now - would you please measure the diameters (inside and outer edge) of the tumes please.
(with a little luck) It may well be that these can be ground off and mushroom vents fitted inside
Ext dia =115mm
Thats a pretty unmaintanable detail. There's no way you could properly prepare and paint that steel, even if the rust and pitting hadn't got a hold.
As others have said, take an angle grinder to the edges of the tunnels, and grind down flush with the roof. I woudl be inclined to do the same with the tubes outside and inside so you just have circular holes which you can then fit conventional vents over.
You could leave the internal tube as a sleeeve through the cabin lining/insulation, but I suspect a steel sleeve would be prone to condensation, and a separate plastic tube or a brass liner not in intimate contact with the shell would be better.
Not the answer I wanted and the one I was hoping to avoid but I suspect you are right and this will prove to be the only sensible course of action, good point about the inner tube, best get rid of the lot!
-
Okay hope this works...
https://www.flickr.com/photos/96201195@N07/
Hopefully you should now be able to see images of the vents!
-
I'm not sure if mushroom vents will fit over because of the way the tube projects above the roof.
I am trying to upload some photos for clarity but do not know how to attach them to the post - help!
-
would brass mushrooms slide over the tubes?
-
Hi Simone,
It would help if you would take some photographs and download them on here so we can see whate we're dealing with........
Will have a go at taking some pics tomorrow, it should make more sense then....
-
I have 4 vents on my roof that consist of 115mm dia steel tubes that project through the roof, these are covered over by a curved rectangle of steel that is welded on at the corners. The problem is that is is impossible to maintain the roof section underneath and subsequently these areas are very corroded. I want to remove the covering steel, clean up the roof and fit something more suitable but I would rather not have to cut out the tubes. Any ideas?
Simone
-
Why wasn't this raised when you first booked the job, surely they knew then?? Does this mean less thickness of interzone, or more cost due to the hempadur addition.
Apparently it doesn't change the price, not surprising since hempadur is about a quarter of the price of interzone, I suspect it does mean less thickness of interzone although this has been denied. I was told that they had recently had problems with interzone and have started to using this method recently, I don't know why this was not discussed especially as they knew I would be present, my only consolation is that they do do a lot of the large sea going and fishing vessels locally.
I would ensure that I have insurance backed guarantees on the work. Sorry this does not answer your direct question.
Yes, good idea, wish I'd thought of that earlier!
-
Hi , I arranged for my boat to be hydro blasted and then coated with interzone 954. Today I went to check on progress just at the point when the guys were unloading the paint to discover they were planning to put hempadur on first and the interzone on top. I explained this was not what I had agreed with the boss and was expecting interzone only at 500 microns. I was told that they had experienced adhesion problems with interzone and now routinely used hempadur 2 pack on the ginger metal and then put the interzone on top.
Does anyone have an informed view on the suitability of this? I'm totally out of my depth, It's not a cheap job and I need it to last.
Thanks
Simone
-
If it gives you peace of mind it's worth a coat of top coat
Thanks, its all about preserving my sanity!!!
-
Hi Pete,
Thanks for thIs, i had read the thread on oxides which was why i used Bonda Prima, however there does seem to be conflicting advice as to whether it can just be left and because of this I called the manufacturer, they do suggest a topcoat is applied over the Bonda, it doesn't seem to matter what the topcoat is as long as it is sealed in.
I agree that its probably a bit 'belt & braces' but having spent weeks cleaning back the metal work due to extensive rust caused primarily (but not exclusively, water was coming in anywhere it could!!!) by leaking windows, I never want to do it again! Oh dear i seem to be ranting
The boat is stripped right back to the hull and as I am now starting from scratch, I'm really keen to get it right and protect from further damage, should water get in again or just from plain old condensation, its all a bit of a learning curve and I do find myself agonising over every decision, every step of the way!!
Ranting again
I'll stop now...
-
beyond me I'm afraid! Just when I googled it Owatrol seemed to get good reviews - not cheap though ... I am sure there are many people on here who can answer the question though!
-
What about Owatrol Oil - would this be a suitable alternative?
-
Hi Andy
WOW
Looks fantastic!
Any reason you chose to use gloss over bitumen?
-
I am restoring my boat and have cleaned back the internal cabin steel and given it 2 coats of Bonda Prima all over, I now want to relay the ballast, is it okay to put a coat of Bitumen straight on top of the Bonda Prima before relaying the slabs?
-
Simone,
When insulating your boat, it's important to get the insulation material (e.g. Kingspan/Celotex) to adhere to the steel everywhere, you need to avoid any airgaps, because any airgaps will create condensation - and condensation will eventually rust.
Superquilt will work, and it's kight and easy to use, (I've used in our demountable wheelhouse roof). However, because it's so extremely flexible, you may have a problem getting it to adhere to your steelwork, and you may also need more than one layer* *(I'm being cautious here, because I do not know haw effective it is compared to Kingspan)
I was wondering how you get the superquilt to adhere to the steel, I know with kigspan/celotex you use adhesive, is it the same with superquilt as all the examples i have seen it has been nailed in place? I have been told ithat superquilt has the same thermal values as the others.
Simone
Sorry I can't help on superquilt- never seen it. Your interpretation of what to do with kingspan foam sheets is good. thre is some risk of cold bridges where any frames are, but thin foam or polystyrene between the tape and the lining will sort this.
N
Thanks again N, the clarification helps as I am a total novice!!!
Simone
-
Re-using the existing slab ballast is OK. You might want to give it a good pressure wash and to ensure it is dry before it goes back in the bilge.
Any continuous sheet will trap moisture ( condensation or leaks) between itself and the base. Bitumen with cable housing will be fine. No need to put primer under it as it sticks better to steel.
The most important thing is to cut an access hatch at the back and to check the bilge is staying dry regularly- say monthly. That way you can tackle any problems as soon as they arise and before they become major.
As you rebuild its a good idea to ensure there is a water vapour barrier between the cabin and the insulation. That will prevent condensation on the cabin sides behind the insulation. Sprayfoam has a built-in vapour barrier but kingspan, rockwool and polystyrene all should have a separate barrier- builders thick polythene sheet and duct tape is good for polystyrene and rockwool or for aluminium faced kingspan the aluminium tape is good.
N
Thanks N, Nice to know I can re-use the ballast and thanks for all the tips re having an inspection hatch etc, dont think I can stretch to sprayfoam and was planning to use kingspan or similar product, if I understand correctly you are saying that all the joints of the kingspan should be filled and taped over with the aluminium tape? Someone has also mentioned a newish product called superquilt, is this something you have come across?
Simone
-
I have recently acquired a 40ft, cruiser stern, Norseman, Hancock and Lane. It has become a major project, (never the intention!) having discovered a large amount of water under the cabin floor. The windows, hatches and around the chimney flue were all leaking significantly. the ballast, 2 ft square concrete slabs, were wet and orange with rust. Having identified the leaks I am now in the process of beginning to put her back together, I am going to clean back the metal on the inside and re prime with Bonda rust primer. So a few questions:
Can i re-use the existing ballast, I was going to lay the ballast on roofing felt and cable housing to raise it a little but I have read that roofing felt can trap moisture, would i be better painting a bitumous paint on the primer instead?
This is just the beginning there will be many more questions!!!
Thanks
Simone
unusual skin fittings?
in Boat Building & Maintenance
Posted
I bought a 22mm brass pushfit fitting but its too big and as far as I am aware they are not available in 3/4"? because the pipe has to be accessed through a hole in the cladding and has spray foam insulation there is very little room even if i could find the right size copper or compression fitting, my plumber is a bit baffled and has left it to me to find a solution...
Yes I am beginning to think this is probably the way to go, new hull fitting, fit for purpose
thanks Alan