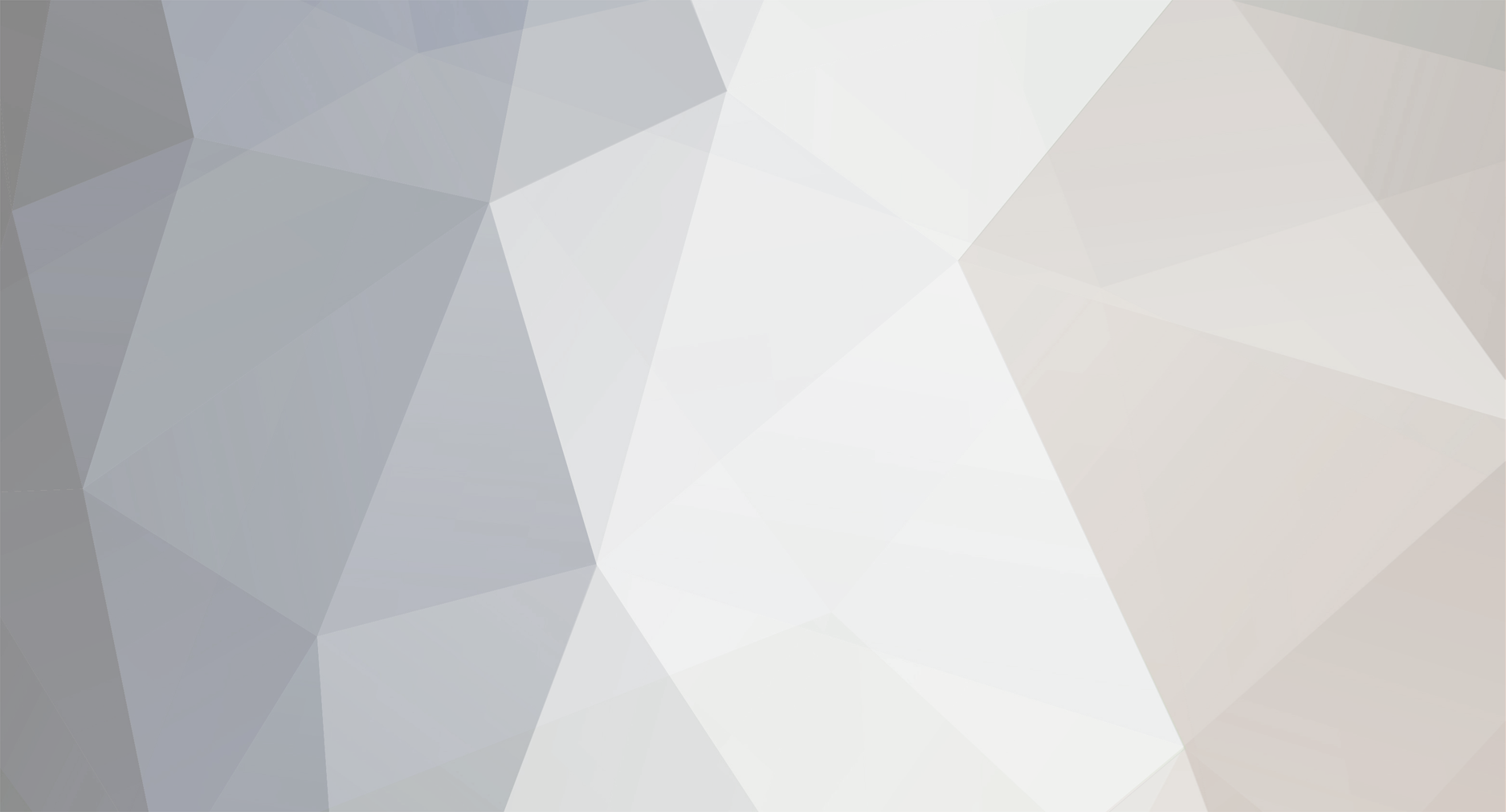
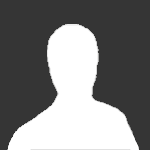
chris collins
Member-
Posts
52 -
Joined
-
Last visited
Content Type
Profiles
Forums
Events
Gallery
Blogs
Store
Everything posted by chris collins
-
Or nearly back to “Progress”, may be just clarifying a few points and putting it all into an inland waterways context. I hope that I did infer that Hull speed is an invincible barrier, it is however the point at which the energy input starts to rise dramatically out of proportion to the gain in speed, there are many boats that exceed their hull speed, indeed, the category of “medium speed” displacement craft are recognised as those achieving a speed /length ratio of between 1.6 and 3. By way of illustration let's consider a 50ft, 15 ton narrowboat; hull speed 1.34 x square root of the waterline length, 48 ft maybe, so; 1.34 x 6.928 = 9.28 knots. Power required for 8 knots = approximately 34 hp, power required for 15 knots = 325 hp!! The craft doesn't vaporise or disappear into a black hole (unlike the steerer who would or should) it would however be using about 18 gallons of diesel per hour, less than 1 mile per gallon! Clearly unless you own a very short narrowboat most of this is inconsequential and so it might be of more interest to look at the implications that do affect canal craft. The most influential of these factors is without doubt the weight or displacement of the craft, for whilst the study of wetted area, resistance, prismatic coefficient, laminar flow etc. all have their place, it is the displacement that is by far the overriding factor. If we take a simplified look at this with our hypothetical 50ft narrowboat and make a reasonably educated guess that given an average entry and swim it will probably displace about 0.7 tons per inch of draft and so we can reckon that to achieve 4mph we need; with 1ft draft ( 8.4 tons) requires approximately 3hp with 2ft draft ( 16 .8 tons) requires approximately 6hp with a lovely traditional 3ft draft ( 25.2 tons) requires approximately 9hp. Note, these figures are approximate (rounded up, rounded down, rounded round) but should give the gist of things. Maybe of more interest in the history and heritage section is the effect on a loaded or unloaded boat. Lets have a look at “Mimas”, ( National dm2 18.5 hp) theoretically unloaded it should be capable of around 8 mph, load it up with 18 ton though and it's down to about 6mph. From practical experience I can say the theory is a bit optimistic and strangely is probably not allowing for the original and fairly battered and worn cast iron propeller that is fitted, probably doesn't account for B.W's no dredging policy either! Logic says that when it was towing “Ray” it would have been capable of around 3 mph which could be about right. A quick look at “Progress”? at 4' 6'' draft with a 60 ton load and 30hp engine would give it a top speed of around 5 1/2 mph. Bearing in mind that to the best of my knowledge there was never an intention for a “Progress” butty (although Lawrence could prove me wrong and post a set of drawings for his next post!) that would work on the river (with the tide) but could be moving an uncomfortable amount of water on the canal. Lastly, Derek, I quite like the theory about long thin boats and the hydrodynamics of fish, however I can't get the figures to substantiate the former (if “Progress was 25' wide and of the same displacement the speed figure is exactly the same!). And the fish? Consider a trout, a sole, an angel fish and an eel and we'd have to think that evolution has more important influences than trying to imitate a boat whizzing along half in and half out of the water. However I am sure that you are correct that for our purposes the shape of the stern is the dominating influence. Phew! ,hopefully next time it really will be back to “Progress”
-
It's not really the time and place here, but it's an interesting subject that does have ramifications in the narrowboat/ barge world, it will also shed some light on why a tug with 110 hp may “only” reach 11 mph. So, lets go for it. Lets imagine that we have a fifty foot narrowboat and we set off along any reasonable stretch of waterway, as it gathers speed our boat will set up a series of waves that start quite close together and get further apart the faster we go. If we travel at for instance, 6 knots then the waves will be 20ft apart, 7knots 27.2 ft apart, 8knots 35.6 ft apart. This wavelength is entirely governed by the speed of our boat and would remain constant whether we are steering a narrowboat or a supertanker (not on the BCN of course). If we get tramping along at six knots our boat will be travelling along on three wave crests, one at the front, one at 20 ft and one at 40ft while our friend in the supertanker will have many, many more all spaced at the same 20 ft intervals. All fine and dandy apart from the trail of boats that we have pulled off their moorings (sorry), now lets suppose that we can get to 10 knots, the wavelength is now 55.6 ft, longer than our boat and as a result the front of our boat is supported by the crest of the bow wave whilst the stern is considerably lower in the trough before the stern wave. We are now trying to go uphill ! Any further increase in speed requires an exponential input of energy to achieve, we have achieved ( more correctly exceeded) the hull speed of our boat. Meanwhile Mr supertanker is smugly chugging away at 20 knots still supported by many waves. (225ft apart)! Because the relationship between wavelength and speed is fixed we can calculate with certainty the hull speed for any displacement boat, 1.34 x the square root of the waterline length gives the speed in knots. So a seventy foot narrowboat will be around 11 knots, Major the tug? Well, we don't know the length of it but if we assumed say, 40ft then the power requirements would rise dramatically to get over 9 knots ( 1 knot = 1.15078 m.p.h) So how much power does a 40ft tug need ? Well, the second biggest factor is the weight of the boat, if we guess at 15 tons then we need around 5 h.p for 5 knots, 25 h.p for 7knots, 46 h.p for 8 knots and a massive 128 to get to 10 knots! How much difference does the weight make ? Lets look at that 8 knot speed, if we reduced the weight to 8 tons we would need a mere 26 h.p, conversely add a bit more ballast to 20 tons and we'll be paying to fuel 66 h.p! Hope that's of interest, next time back to “Progress”
-
Tim, re the spikes, that's a very nice offer, thanks for the thought, I feel that ultimately it may be doomed by postal charges, I'm also thinking that there must be far more deserving cases than mine. However, if there is a way and it does happen, brilliant!! Lawrence, that's a demon set of drawings, and, placed alongside these of “Progress” would make a good game of spot the difference. It would be really good to get the two sets together for comparison, apart from the obvious constructional details there is again the anchor winch, navigation lights/mast, coamings and hatchboards that would be more at place on the estuary. I'm struggling to read the details on your drawing but it looks as though one of the potential problems with “Progress” is addressed with the stern ballast tanks. For me this is a new and very interesting part of the history of “Progress,” a possible indication that G.U.C.C where intending more than just the one? Certainly would answer the question I had about the availability of timber for more than just a few wooden ones. Incidentally the “Progress” drawing is dated 29-1-34 , drawing number 131, how does this compare? I appreciate that you'll probably all get a bit fed up with me banging on about the river/ estuary bit but it is worth comparing Lawrence's drawings with the picture of what is, in my humble opinion, the more canal orientated “Pioneer” in post 34. .Pete, very interesting that “Progress” shows up at 12' 1 ½'' , it is very definitely 12' 6'' on the drawings and in real life, I have never seen the gauging sheet though so it's a little mystery Re the 1958 trial, thanks for all your input, it's a fascinating scion in the history of the wide motorboat and it would be nice to know the full unadulterated truth, it's quite sad that B.W is held in such low esteem that one bridgehole is regarded as a bridge too far. Hopefully one day solid evidence will surface as to the true intent and result of the event. SPA50312 by chriscollins1, on Flickr SPA50315 by chriscollins1, on Flickr
-
Tim, thanks for that, it's a good point. Years ago just before Walker bros succumbed to becoming a Tesco store I got the opportunity (courtesy of Tony Walker) to clear out the old nail store, here are a few pictured next to the equivalent sizes from Glasgow steel nail. The “originals” are a much finer shank, almost a different animal. The newer nails definitely won't cut their own way in and require a full depth pilot hole, even a little short of full depth is risking a mullered head (the nails, not mine, - although........) The rusty one on the right is one taken out of “Progress” and bent exactly as you describe. SPA50295 by chriscollins1, on Flickr
-
Those of you who have had “previous” with planking wooden boats will be familiar with scrabbling around trying to find enough space whilst trying to fit the planks, there are probably enough anecdotes to keep a stand up comedian in dinners all year round. The next couple of photographs will be no surprise, “Progress” being what it is it seems a bit more extreme, that might just be me getting a bit older. The yard here is quite long, narrow and at the end of a navigation so it was decided quite early on that a floating dock would be the best way forward, not only does it give more work space, it can also be moved to give a bit more leeway when the going gets tough. SPA50269 by chriscollins1, on Flickr SPA50272 by chriscollins1, on Flickr The nice bit about slogging away at the big bits is that they do cover a bit of space when done. SPA50280 by chriscollins1, on Flickr Once the plank is pulled round and fitting snugly it is fastened to the plank below. The nail is a 4'' galvanised rosehead boat nail, I normally get them from ; Davey & Company in Colchester (01206 500945) they stock a good range of sizes (and lots of other goodies), unfortunately they do not stock the 1 ½'' needed for the shearing, in the past I have always got these from; The Glasgow steel nail co ( 0141 7623355) but they normally require a big order. SPA50281 by chriscollins1, on Flickr Back to the fastening, the nails sit in pockets in the upper plank and are driven at a slight angle through and into the lower plank. I normally use a gouge for the majority of the pocket and finish it off with a few turns of a round nosed bit, the nails need a pilot hole which because of the tight angle requires an extra long twist drill. SPA50282 by chriscollins1, on Flickr Back to the fastening, the nails sit in pockets in the upper plank and are driven at a slight angle through and into the lower plank. I normally use a gouge for the majority of the pocket and finish it off with a few turns of a round nosed bit, the nails need a pilot hole which because of the tight angle requires an extra long twist drill. I hope you'll forgive me for getting a bit anal about a few spikes, it may or may not help some one out. SPA50283 by chriscollins1, on Flickr And over to the other side, this plank was about 3ft longer than it's opposite number and was determined to cause space problems, I jacked the boat up another 6'', took off just about everything unnecessary off the dock (gained another inch or so) and it was still determined. When I'm working by myself I really need to get the hood end of the plank in place and cramped quickly and accurately, the first few minutes when the plank is really hot are really make or break (pardon the expression), if the hood end goes in well – cramp it – run to the other end pull some bend in – tie it – run back – more cramps – run back – more pull...................... First five minutes ….....critical. Five to ten minutes......... 90% bent. Ten to twenty minutes........details. When it all goes well it's a real pleasure, plank bends easily, no strain on the frames and a minimum of cramps to hold it all in place. SPA50288 by chriscollins1, on Flickr As it happens this one did go well.
-
1)Laurence, many thanks for your kind words, back in the day when my wife and I bought our first boat that little “Boatmans cabin” catalogue was the “wish book” of choice, that first boat was an old joey and so presented little opportunity for adornment and probably did little to help your business. It may well however have helped fuel the passion for ex working boats. 2)David, many thanks for knowing how to use the miracles of modern technology and taking the trouble to help out. 3)Admiral, Thanks, no book, I'm no writer, at the moment I'm just trying to record a few hints, tips and tricks that I've picked up over the years, I won't try listing all the mistakes I've made because there probably isn't enough room on the forum. Maybe one day I'll put it on it's own webpage. 4)Carl, was that the Carl that Martin Cox used to speak of? Where you with John Wooley at Iver, Ham wharf or Eel pie island? As far as I am aware John had quite a bit to do with “Progress” , perhaps Tam & Di can fill in the details? Do you have a current address for John at all ? Yes I do use a bevel board as you describe, I just haven't taken any decent pictures yet, one day...
-
The next plank up follows a similar process, firstly hanging battens and fairing the frames, ascertaining the position and angle of the stempost hooding, cutting the hoodings, spiling the shape of the plank etc. The short wooden frames in this shot give an accurate angle for the joint between the fist and second plank, they are only really to give an accurate position for the spiling board as any deviation here has a profound and unwanted effect on the shape of the plank SPA50251 by chriscollins1, on Flickr More bagatelle, the two lines here delineate the inside and outside of the plank bevel, the inner line is the size of the inside of the plank and is therefore the more critical in the pursuit of a “good tight ship.” The angle that the two planks meet dictate the bevel that needs to be planed into the lower edge of the plank, this angle will change from stempost to the beginning of the straight section and needs to be marked accordingly. Normally the angle of the bevel causes the plank to be larger on the outside of the boat hence the two lines. SPA50263 by chriscollins1, on Flickr The romance of boatbuilding, drawknife by william Gilpin , if you are looking at/for old tools and you find anything by “william gilpin wedges mills” it'll repay the hours of restoration time handsomely, really fine quality steel that takes and holds an edge and makes a nonsense of modern “technological advances”. The wedges mills moniker dates it around mid eighteen hundreds. If you look at the floor in the background you'll also see the smaller chippings where I was doing the straight section with a non romantic power plane, ho-hum. SPA50267 by chriscollins1, on Flickr The wooden narrowboat had evolved as a very efficient way to use of the “average” oak tree to produce a boat, both the width and length of planks coincide nicely with oaks (given average fertility and rainfall) in the prime of condition. I strongly believe that this “average” tree size and it's influence on boat size also played a very fundamental role in the dimensions and particularly lock length of our canal system. Enough of the pontificating, suffice to say that by the time the plank rippings have been turned into shearing, the narrower boards gunnels , the short boards decking, etc, there is very very little waste. These “average” oaks are generally around 125 – 150 years old, above this age there seems to be exponentially increasing risk of wind or lightening damage and it's associated fungal attack and an increasing risk of fungus attack at the base of the tree. It is very noticeable in early photographs of this area (the environs of Walkers of Rickmansworth) how few trees there are of any description. Which has what to do with “Progress”? Well this lovely tree is a bit over 200 years old (and took a bit of finding) and after allowing for the sapwood and a bit of heart shake is only just big enough to be getting these planks from. Bear in mind that this is the second plank up and that the first strake is wider still. The shape of these planks is a function of the shape of the bow, I.e. the bluffer the bow the more “banana” shaped the plank will need to be, conversely the finer the bow the less “banana” and therefore the narrower the board required. Needless to say “Progress” is very much in the bluffer camp, knowing how difficult it was to find suitable timber for the rebuild it begs the question – could G.U.C.C have found enough timber to build even a small fleet of “Progresses” even if it had been a commercial success? SPA50266 by chriscollins1, on Flickr Sticking with the bluff fore end theme here's a lovely picture of the original build, it shows all manner of constructional details which hopefully we can discuss later, for now it gives a fair indication of the shape of the fore end. SCAN0001 by chriscollins1, on Flickr The general arraignment blueprint issued by G.U.CC is entitled “Motor barge for service on canal or river” and I must admit that I didn't really grasp the significance of the “or river” bit until I saw this photograph ( reproduced here in two parts because it wouldn't fit under my scanner in one hit). Check out the navigation lamps, they feature on the blueprint and are serious pieces of kit. SCAN0002 by chriscollins1, on Flickr Now check the mast and mast head lamp, again it features in the G.U specifications, again it's a no nonsense piece of kit, indeed more “or river” than roving bridge. So now that bluff fore end makes much more sense, the additional fore end buoyancy would certainly aid a passage on the the short sharp chop of wind over tide in the Thames estuary. I've read in the past that “Progress” was commercially unsuccessful because although the locks on the G.U had been widened the channel was too narrow, I'll happily admit that the canal north of Berkhamstead is not wide boat territory but below that saw a lot of (unpowered) wide traffic. Notwithstanding a loaded draught of 4' 6'' this still gives “Progress” rich vein potential business. If we treat G.U.C.C with a little more respect we could quite reasonably speculate that “Progress” was built to spend a large portion of her time on the river, most likely loading over the ship side before delivery to a factory or works. I'd go one step further and say that there is a strong possibility that “Progress” was built for a specific cargo that for some reason or other failed to materialise. I'm just the boat builder so I'll grateful to leave that for the canal historians amongst you to mull over SCAN0003 by chriscollins1, on Flickr
-
With the evenings drawing in there is a little more time to put captions to photo's, possibly not enough time to answer xadmx's question of “why?” To be honest it would be easier for a man to explain the inner workings of a woman's mind, certainly scared me off the keyboard for a while. So the next plank, this “should” be an exact mirror image of the one just fitted, however if the original builder had to work around a fault in his timber stock there could well be a variation side to side, common sense says to work to the original intent. On “Progress” the length is slightly longer side to side but other than that identical. Should the next board in the pile be suitable it would be good to mark around the first plank to ensure the two are as alike as possible. As it happens the next board wasn't suitable, or the next, or the next,........... SPA50230 by chriscollins1, on Flickr SPA50231 by chriscollins1, on Flickr With the first strake in on both sides I could start putting in another pair of frames, it's all a bit of a balancing act at this point, obviously the number one priority is to to copy the original shape and construction as accurately as possible, one piece out and a new piece in would be ideal, unfortunately pieces are falling off quicker than I can replace them – hence the big hole on the port side, not ideal but still enough to get a good copy of the original. SPA50233 by chriscollins1, on Flickr SPA50238 by chriscollins1, on Flickr Over the years I have tried dealing with cutting the hoodings in the stempost in different ways, the easiest is to cut them using what is left of the original as a pattern, unfortunately this is normally the least accurate. Working the rebate as you go up the stempost using a batten hung on the frames to give the angle of the plank landing is far more accurate but generally involves a deal of balancing, contortions and ambidexterity. Once the angle has be accertained a block planed to the same pattern can be cramped to the post to guide the cutting. SPA50241 by chriscollins1, on Flickr
-
Guess I failed at that attempt to clarify the spiling business then, I'll try and get some clearer pictures over the next few planks, I'm no photographer so when I get home and download the pictures that I hope will illustrate a certain detail it's not unusual to find I've got a shot of the wrong end of the boat! So, plank cut, bottom edge bevelled (right hand side in this picture) , the top edge is normally, but not exclusively, cut and planed square. SPA50198 by chriscollins1, on Flickr In the good old days of Walkers and Bushell Bros the steam box would be large enough to take most of the plank and set a little distance from the boat being built, when the time was right the team would set to hoisting the plank out of the steam box, over to the boat and start cramping it around the frames. In these good new days there is only me on the team and if I have to move the plank any distance it will have cooled to much to do any bending. Best move the mountain to Mohamed. I try and set the plank up as close as possible to it's final position and fit the steam box over and around it. This particular plank was very top heavy and really didn't want to to be cooperative at all, with that and trying to cramp at those angles you just know that there is a farce in there just waiting to happen. SPA50203 by chriscollins1, on Flickr The equipment and to a degree the method of wooden boat construction often has more to do with what is to hand or easily available – well demonstrated by the varying ways of driving the bottom spikes alluded to earlier in the thread, steam boxes and boilers definitely come into this category. I generally end up making a new steam box for each rebuild, each one a development and hopefully an improvement on the last, up till now they have been simple plywood tubes, light enough for me to throw off at the appointed time and with varying degrees of insulation. This time time I have gone a bit high tech and built one of alloy sheet with a more modern insulation, I'm thinking that the alloy will not soak up the moisture in the steam the way that plywood does and I'll get a more pliable plank quicker for it. I've also made this tube split along it's length as this will help removal within the confines of the dock. SPA50211 by chriscollins1, on Flickr SPA50204 by chriscollins1, on Flickr The boiler is another of those “under development” parts, this is this years model, it has an uncanny resemblance to a gas bottle, just some quirky coincidence I guess. Inside it looks a bit less like a gas bottle, the small tubes are to increase the surface area available to heat, the large centre tube holds about half a gallon of water which I can top up (red funnel) as the level drops. A gas blowlamp provides the heat. This model is working quite well, it is quick to raise steam, economical, reliable and mobile, should last until the next big idea then. This particular steam box/boiler combination seemed to provide a good moist heat, possibly moister than previous setups so I have been trying piping in the hot exhaust gas to the steam box, just trying to use the energy more efficiently. This seemed to work well, about 10-15 degrees hotter over the length of the steam box. SPA50206 by chriscollins1, on Flickr SPA50209 by chriscollins1, on Flickr All seems to work, plank is bent,it fits, farce not totally avoided (angles,slippery plank, cramps imitating scud missiles) but result shows no scars. I'd have loved to be apart of that team at Bushell bros first time round. SPA50208 by chriscollins1, on Flickr
-
Hi Derek, yes Kevins saw runs along a couple of rails at ground level, the log is dogged in place to keep it still on the lower cuts. With the benefit of hindsight the photo's could have been better. That's a lovely link to the steam powered sawmill,stunning saw and some stunning timbers, thanks for that. The shape along the bottom edge of the plank will be dictated by the shape of the bottom boards and the amount of twist in the plank as it flows from the stempost back to the straight centre section, “Progress” is quite barrel sided, the bottom boards are 10ft wide on an overall beam of 12ft 6 inches so the bottom strake is angled out at 45 degrees, as we will see this makes for a fairly radically shaped plank. The shape of the top edge of the plank is ascertained by hanging a batten from stempost back to the centre plank hopefully coinciding with the shape of the original whilst getting a fair curve. First problem; find a batten around 25ft long with a nice straight grain, no knots or other hard spots, it won't have Wickes name on it for sure. SPA50171 by chriscollins1, on Flickr I'll deal with spiling the shape of the plank in a bit of detail as hopefully it may be useful to someone else, because of the shape of “Progress” this differed slightly from normal narrow boat practise but should give a general idea. Once the batten position is finalised the shape of the plank can be spiled onto a spiling board cramped into position, due to the angle of the bottom strake it was found easier to make the spiling marks on the inside of the spiling board rather than the more normal spiling block/ outside of the board marks. Also because of the large amount of curve in the shape of the plank I found it easier to make some longer than usual templates for the fore end and scarph rather than joining several pieces of board together. SPA50175 by chriscollins1, on Flickr SPA50173 by chriscollins1, on Flickr All fair? Then I can start striking marks from where the projected line of the inside of the top and inside bottom edges of the plank should be. In this photo I have marked three inches from where my plank edge should be to the spile, when I move the spile to the board that I want to mark out I will need to measure three inches out from this mark to get the true shape, I'll try to keep this distance a constant, if I do need to alter the distance I'll make sure to note it – the plank won't need any help from me to be an unlikely shape. The more marks the better really. I normally aim at around six inch intervals. Before I take the battens down I'll record the bevel of the lower edge of the plank, this bevel will vary as the plank curves round to meet the stempost so I'll check it at 12 inch intervals and mark it onto a strip of wood the same thickness as the plank for future reference. SPA50177 by chriscollins1, on Flickr With the spile transferred to the timber pile it can be moved around to try and best avoid any faults in the board, I normally tack a nail in place to mark the positions from the spiling marks, a good quality batten can then be used to make sure these lines are fair before pencilling in the shape of the plank, could be the worlds most expensive bagatelle board. SPA50179 by chriscollins1, on Flickr When the plank is steamed around the curve the inside radius compresses somewhat whilst the outer stretches, intuition would would make you inclined to say that the inside compresses less than the outside stretches – I have no proof of this though, any way the upshot is that if you take the length direct from a spile taken from the inside of the planking the the plank will be short when fitted. To counteract this I normally add a small amount, it obviously depends on the length of the curve as to how much this “small amount” is, but in this case 3/8 inch worked nicely. SPA50181 by chriscollins1, on Flickr
-
A bit of a delayed update, an errant card reader (camera not tarot) and a couple of other pressing jobs means I'm behind with the updates and more importantly behind with the job, no change there then. Would I like an alfa 75? Well yes, but a 33 stradale would be an even nicer way to get even further behind with the job. I'm still in need of any photographic evidence of “Progress's” past life so if you do know of any please let me know (or better still post it on the forum) . A special “pretty please” to Tam & Di. For the timber for this job I have been dealing with Kevin at Willows sawmills in Uckfield, East Sussex (01825 763507) it's been a real pleasure and he has sourced us a couple of exceptional planking butts, here's a couple of shots of him cutting some framing stock. Highly recommended. SPA50164 by chriscollins1, on Flickr SPA50163 by chriscollins1, on Flickr In order to avoid ridiculously wide planks “Progress” has a couple of “stealer's" let into the bottom strake at the fore end, I had thought that they may have had a few fasteners to hold them before the bottom strake was fitted but can find no trace, just the normal side plank to bottom board spikes. Although some of the planking timber Kevin supplied would be wide enough to span both plank and stealer the resulting plank shape would be a bit extreme with some fairly weak short grain in that corner, so stealer's it is. SPA50165 by chriscollins1, on Flickr It's a nice surprise to find some little (manageable without a hernia) bits whilst your all keyed up for the big stuff. SPA50172 by chriscollins1, on Flickr There are a couple of photographs around that show “Progress” during construction, unfortunately the copies I have are quite poor so I won't try to reproduce them here, they do however show that the boat was built up over a set of dummy wooden formers or frames. I believe that this method was fairly common in this area, the immediate apparent advantage would be that if the adjacent strakes are tied together with rampers and a degree of flexibility built into the strake to former joints any shrinkage of the planks during construction is automatically taken care of. I'll try to clarify that with some photos later in the rebuild. (maybe also have a little discussion about the relationship of plank widths/lengths, tree sizes, shrinkage etc.). Anyway for now here's a shot of some temporary frames to allow me to steam that first bend. They are just tall enough to get the bottom strake shaped up. You'll obviously have noted the missing bottom board and you'd be right thinking that the boat might leak a bit like that, I normally leave out a board or two by way of the scarphs in the bottom strake until the boat is at least two strakes high as in the past I have had trouble with the bottom boards expanding and straining the fastenings through the scarph. I'll try and catch up with the updates over the next couple of weeks, catching up with job will be a little more difficult. SPA50170 by chriscollins1, on Flickr
-
Hi Phil, How can you look at something that is going to be so desperately in need of paint and claim that you can be of “absolutely no help at all”?? Good to hear from you, hope your well and enjoying life, I'd kinda hoped that you might be coming down this way and find time to do the bedhole and drawer fronts on “Mimas”, it will all come together one day. Wife and family are fantastic and a welcome distraction from alfa's (just a little bit more to do on alfetta, lots on bertie.) Still hoping to get up your way on the motorcycle ….... one day. Therapy for alfa romeos? That would be a bit like sending your wife to the surgeon because her figure was just too exciting, “oh excuse me doctor but what I really wanted was an ironing board” clearly Alfas are a therapy. Many,many thanks to all the people who have contributed to this post,I really appreciate the goodwill,the compliments (who was it that said “your trumpet never sounds so good as when someone else is playing it”?, and most of all the anecdotes and information conveyed. Sorry about the lack of updated pictures, I'll try and sort that soon.
-
The fore end frames are not normally attached to the bottom boards and would in a new build be fitted after the first strake had been steamed and fitted around temporary formers, having the old boat to work around slightly complicates matters, I'd like to try and get new bulkhead frames and deck beam into place and shored up before thinking about that first stake. The port frame is in very poor shape, luckily the starboard one has kept the integrity of the planking lines although the diagonals are a long way out, If I take the outer shape of the starboard frame,the length of the original deck beam and, from the old bottom boards, the chine measurement, I should be able to get pretty close to original. SPA50142 by chriscollins1, on Flickr The position of the frames where marked on the original bottoms with a shallow saw cut, I haven't seen this on other boats that I've worked on. SPA50140 by chriscollins1, on Flickr It's getting harder to find suitable timbers for frames, I did used to plank the trees myself to get the right shapes, unfortunately this was making a long job longer and I really wanted to be a boatbuilder more than a sawyer. This butt had a bit of buttress to it which will just about suffice for this pair of frames. SPA50148 by chriscollins1, on Flickr The frames and deck beam where set up “dry” to check the dimensions, angles and fit and once correct painted to slow down the drying process, they are then positioned ready to fine tune the bevels. SPA50153 by chriscollins1, on Flickr SPA50157 by chriscollins1, on Flickr
-
Unusually for a job like this I am lucky enough to be in possession of some of both the original drawings and the written specification as laid out by G.U , whilst this is by no means complete this does give a fascinating insight into the history of the boatbuilding process. It also throws up a few anomolies, one of which is the stempost, the specifications and drawings quite clearly show the dimensions as 10 inches by 16 inches, the original post is 10 inches by 14 inches. The discrepancy is almost certainly due to the availability of a suitable piece of oak at the time of build, the dilemma is, do I build to specification or follow the original? On the face of it either could be the “right” thing to do, win, win or lose, lose depending on your half full glass point of view, but, just to enlarge upon this a little bit............ (This next bit does get a bit “anoracky” so you may well want to skip it, I'm hoping that one day it may help some other restoration,on the other hand it could just turn out a bit gobbledegooky..........). “Progress” or any other wooden boat would have started life as four or five unique trees each with their own quirks, foibles, shakes, knots hard spots and all manner of other individual characteristics for the boat builder to fashion to the required size and shape. Bearing in mind that a wooden narrowboat (or wideboat) is very close to the limits of what can be achieved with the “average” sized trees it will be appreciated that some of the features,faults and character of any given wooden narrowboat will be caused by the uniqueness of those original materials, thus the restorer may find odd/mismatched plank sizes, hard spots on the bends, stealers, an assortment drying quirks, etc,etc. Now picture said restorer with his own four or five unique trees, any attempt to blindly follow those original characteristics is likely to end up with twice as much “character” and not all of it welcome. Whilst our intention must be as accurate historical record as possible it is fair to say some measure of compromise is needed to allow for the “naturalness” of the materials. Without wishing to throw any more fuel on the “it's restored/ no it's a new boat” fire I do feel that in order to make a more accurate restoration we have to start by studying the original intention and giving that intention priority. This means that we need to approach the manufacture of any component part from both a new build thought pattern and a replicate thought pattern and carefully balance both for the benefit of the boat. Once we appreciate the relationship of the material to the resultant boat it becomes apparent just how significant original photographs/literature are, and if you have an unrestored boat, treasure it. I'm glad that little lot's out of the way, I hope it wasn't too boring/ranty/pious for you. SPA50123 by chriscollins1, on Flickr Back to the stempost, the leading edge is marked from the stem iron albeit allowing for any repairs needed. The backside marked to follow the original, I prefer to do the hoodings with the stempost in place as it is more accurate but they need to be roughly marked now to guide the shaping of the stempost. SPA50126 by chriscollins1, on Flickr As to shaping, whatever weapon you fancy, I have done one entirely by hand with axe and adze, I wont be doing that again. This one was chainsaw/adze/plane(s). SPA50129 by chriscollins1, on Flickr SPA50135 by chriscollins1, on Flickr A nice little knee (lot nicer than my knees) to support the bottom. SPA50139 by chriscollins1, on Flickr
-
And on to fitting fitting those bottom boards, the idea is to finish up with a good accurate, solid platform with both sides identical and a dependable datum from which to build the rest of the boat. I'm lucky now that I have the dock to work in as it provides a much better base than previous rebuilds (softish ground). With those fore end bottom boards fitted there is a head/heart choice, the head says do the two outer kelsons . But to be truthful although the selection/cutting/scarph is fairly interesting, the sequence of bolting them in becomes a bit laborious, along the lines of; climb in boat, mark and counterbore the top of kelson, clear away swarf, clean under kelson, climb out of boat scramble underneath, jack up the next couple of boards snug to kelson, climb in boat, drill through kelson/bottom, clear swarf, climb out of boat, scramble underneath, counterbore bottom board, drive up bolts, climb in boat, fit washers/nuts, clean under kelson for the next couple of boards, climb out of boat.................. The heart says do the stem post, artisanal, photogenic, a psychological landmark …...........get out the traditional tools... or not. So I'll be sensible. This picture shows quite well the stresses that sometimes build up in trees, although there was no real hint in the grain pattern this pulled a lot more than normal when cut along the centre. Sometimes it's possible to use this to advantage, say on a straight centre centre plank, pre stressed against hogging for instance. In this case I really wanted nice straight pieces so having relieved the stress the two halves where re cut straight. SPA50109 by chriscollins1, on Flickr SPA50115 by chriscollins1, on Flickr Once the side kelsons are fitted the heart can have it's day, this is the embyrionic stem post. It's always a bit of a battle to find a good piece of timber for this job as the older and bigger diameter trees are often starting to rot at the base and the younger boles are generally to small. This piece is not bad but I'll have to include a bit of heart shake. SPA50118 by chriscollins1, on Flickr
-
By coincidence Mark Pullinger emailed me a copy of this photograph (many thanks Mark) at the same time that Tam wrote that snippet about the side decks being modified by B.W, the photograph shows the modification superbly and also demonstrates the shortcomings of wide beam above Berko. Tam yes, I was planning to go back to original specification as best as I can. I'll be taking out the r.s.j and restoring the frames to their original length. 08-28P%20Progress by chriscollins1, on Flickr I normally try to restore the boats on a kind of plank out - plank in system, although this takes longer than cutting off large chunks and replacing them, without wishing to get too arty-farty, it gives you time to really get a feel for the spirit of the original. However, in this case I did pull out a large chunk of the fore end bottom boards, which when laid out and clamped enabled me take off measurements with far more accuracy than would otherwise be possible,these where then lofted full size before being transferred to the new boards. The old boards, although of reasonable thickness had really suffered on the chines which would be expected along the full beam parts, less so on the fore and aft swims, hmmmm. SPA50103 by chriscollins1, on Flickr SPA50101 by chriscollins1, on Flickr
-
In 1989 Waterways world published this photograph in an article about Bushell bros, I hope that they won't mind me using it here, I believe that it is part of a collection belonging to the family. The caption refered to the timber being for the kelsons on “Progress” being bought to Tring from Millwall, at the time I must admit I was a bit sceptical, after all “Progress” is 75ft long the centre kelson would need to be 68ft to fit in one piece, surely not? Anyway when we first obtained and deconverted her I had a good look and sure enough no joins! The picture makes me smile every time I look at it, having transported some long lengths of timber in my time I know how much it bounces when it's got a bit of overhang – that lorry must have had it's wheels off the ground at times! Let alone guiding the overhangs round the bends! It serves to remind how sanitised the H&S regime have turned this country. It also opens up a myriad of other questions, why go to the trouble of dealing with that load,would it have been cheaper than local oak? Would it have been more effective than local oak?Did G.U specify that timber? What sawmill facilities did Bushells have? So, back to the present, whilst I normally try to be as faithful as possible to the original construction Baltic pitch pine in that sort of length is only tradeable for rocking horse poo so I'll be doing the kelsons in oak, 2 pieces for the centre and 3 for each side so that I can stagger the joints. progress kelson by chriscollins1, on Flickr This is the first piece 36ft long and 9 inches by 5, the stepped scarph is 5ft long. SPA50092 by chriscollins1, on Flickr Fitting is fairly straight forward, although as cut it had a little spring so needed a bit of wedgeing to straighten out, carefully centred and careful not to trap any debris underneath as it's bolted down. It's noticeable that over time kelsons tend to rot from the top down whilst the interface between kelson and bottom boards, although untreated as original, tends to last longer, often almost appearing as new when dismantled. I'd presume this is to do with the counterbores on the top side acting as moisture traps as the pitch fillers deteriorate,whilst the available oxygen and moisture content being less suitable for fungal growth preserve the underside. Anyway, on this one I have treated both surfaces before fitting,crossed fingers. SPA50096 by chriscollins1, on Flickr SPA50097 by chriscollins1, on Flickr Sometimes wooden boatbuilding is less romantic than others. SPA50098 by chriscollins1, on Flickr
-
That's a lovely story about Charlie Atkins, I'd reckon that it's the water pressure acting on the outside that helps push the bottom board back in place, the bang on the kelson probably sets up enough shock to break the “sticktion” to the adjacent boards to allow it to seat. Maybe one day I'll give it a try on one of the boats due for a docking. Just about all the boats that I have worked on ( including the composite ones) have used “rampers”midway between the kelson and chine, normally a 5inch flat point boat nail driven at an angle across the joint. To be honest I have never really thought that these lent much in the way of strength (certainly they lent themselves to propagating pockets of rot caused by the moisture collecting in recess for the head), they may give some resistance to any wracking movement athwart the boat, however they are very handy when assembling the boat as they locate the boards during fastening the kelson/bottom strake , they probably help prevent the boards warping during the build aswell. How about “Progress”, well just to be different it has steel dowels and three kelsons, the dowels occur almost directly below the two outmost kelsons, a hint that their function is not vertical strength? SPA50088 by chriscollins1, on Flickr
-
Nice to hear that the rebuilds are lasting well Bill, sounds like good timber selection,good craftsmanship and good practises, well done. It is an interesting process watching your work age, having missed out on the age when generations of the same family would persue the same occupations our experience becomes hard won, Bill your 33years of experience and hindsight is a great assett, hopefully we'll meet one day and chat all things wooden boats. I'm convinced that a wooden boat that is used daily like the trip boat that Bill describes is at a huge advantage in the longevity stakes when compared with a museum exhibit that spends a lot of time shut up at its moorings,even worse clothed up and shut up at its moorings, the air flow through a moving boat is, in my humble opinion,hugely beneficial in clearing the moisture saturated air that promotes fungal growth. Unfortunately I haven't yet rebuilt a boat that is likely to be used daily, if I start one tomorrow I'll be 88 in 33years time. Any other wooden boatbuilders want to share experiences/hindsight?
-
Nice to hear from people that have got the Tshirt, good to set out the choices - not forgetting a strong arm and a good hammer. I guess we tend to use what's handy at the time. I have come across the clenched bottom spikes as Bill describes in the past, not on Walkers or Bushells boats and memory escapes me which boat it was, I had presumed that it was done to counter elms predilection for cupping and warping either before fitting or during the build. Clenching would certainly help preserve the integrity of the chine joint. Bill, pardon my curiosity but when you where doing this it needs an absence of the second strake which infers an extensive rebuild ? I'm certainly getting good results pressing the spikes in, the cramping action seems to promote a very tight joint. SPA50083 by chriscollins1, on Flickr
-
Having had a break at christmas there is no great changes to the apearance of “Progress” however I'd like to keep the thread fairly prominent as I'm still in need of as much photographic evidence as possible, please don't think that something previously published in a book or magazine is of no use, it may well be that I haven't seen it. It would be super to put a whole catalogue of pictures in one place. Anyway I thought I might take a more detailed look at the process of spiking the bottom boards in the hope that it's helpful to anybody else in the same boat/barge/rock/hardplace. Bottom spikes, the one on the left is an original found at Walker Bros shortly after they closed. After trying various copies including forging my own I now use these, supplied by; B.B. Price of Halesowen I think the number is 01384 413341. They now cost around £1.60 each minimum order 500. They are 11 incheslong by 3/8 square. SPA50069 by chriscollins1, on Flickr I have been using this jig to get the bottom strake at the correct width and angle along the straight section of the boat, the bottom strake is angled at 45 degrees which makes for a lovely wide plank land that, well planed should seal marvellously but will be prone to slippage during assembly so jig plus plenty of cramps. SPA50070 by chriscollins1, on Flickr Just more of the same. SPA50072 by chriscollins1, on Flickr Counterbores for the spike heads,in this instance bored before the rest of the pilot hole. SPA50073 by chriscollins1, on Flickr Nice cramp, I got this one from Walkers so it's a lot more experienced than I am. SPA50074 by chriscollins1, on Flickr The wooden bit behind the drill is a jig that cramps on to bottom strake, it helps to get the pilot hole nicely centred in the bottom strake. The drill is the diameter as the spike is square ie; 3/8 inch. SPA50076 by chriscollins1, on Flickr To make driving the spikes a little easier I lubricate them with a little grease, a modified grease gun helps lubricate the holes. SPA50077 by chriscollins1, on Flickr Having sacrificed my knees,back and a finger to the gods of (wet)dry docks and wooden boats I am trying to look after the elbows. Given that there are spikes at five(ish) inch centres along both sides of the boat that all need driving in not the best of positions I built this jig to press the b*****ds in. If your replacing the bottoms on an otherwise complete boat they will normally press up against the weight of the boat, just be sure that you get the base angle of the jack correct. SPA50079 by chriscollins1, on Flickr Don't forget a nice little oakum grommet before driving fully home. SPA50080 by chriscollins1, on Flickr An out side view of the press for the spikes. SPA50081 by chriscollins1, on Flickr Lets hope for bit more action in the coming weeks and please send those pictures in!
-
first off, many, many thanks for all the goodwill messages,very much appreciated, secondly, thanks for the advert block / flickr instructions;given the choice I'd go for the service with the least intrusive adverts.Having said that I haven't taken any photo's this week - it's just been cold/wet/uncomfortable/unphotogenic spiking up the bottom boards/sideplanks Adam, I'm (kind of) trying to avoid putting captions on the photo's - trying to avoid the dilema of how much information is the right amount, trying to avoid the situation where I can't post the photo's as I can't find the time to write the captions, however I do appreciate your interest so by all means ask the questions and I'll do my best to answer. The supports in the third picture are just keeping the bottom boards centralised in the dock,the dock is a floating dock so no plumb bob's or spirit levels so it becomes quite important to have some fixed and accurate datum's to work to. Tam, as a man in need best I'm patient,I doubt I'll get as far as the deck by tea time anyway.I'm in awe of auto-cannibalistic - very thought provoking.
-
Just a bit of an update,Does anyone else get really peeved with the ******g adverts on photobucket? the forum won't let me upload from flickr -any hints? Anyway here's some pictures of new bottom boards,a big pile of oak and the first of the side planks. Many thanks to Mike Constable at Stoke Bruerne for his archive help.
-
Hi Tam, Di, sorry about the delayed reply, many thanks for posting/reposting those two photographs,by coincidence when I bought "Progress" from B.W the price was....£50! Unfortunately it needed a bit more than the mudbox lid to fix.As far as the rebuild goes some parts follow fairly standard wooden narrowboat practise,some parts are notably different but survive well enough to be reliable patterns, some like the front deck/ coaming/ hatch/ winch need all the help they can get. Do you have any photo's/recollections/ just about anything that might help? Also any photo's in dock would help getting the scarph spacing correct.Many thanks & lots of luck Chris.
-
Hi Laurence, that would be great, chriscollinsboatbuilding@gmail.com should reach me,many thanks. Thanks also to yellowback for the link,just having a look through the archive lists.