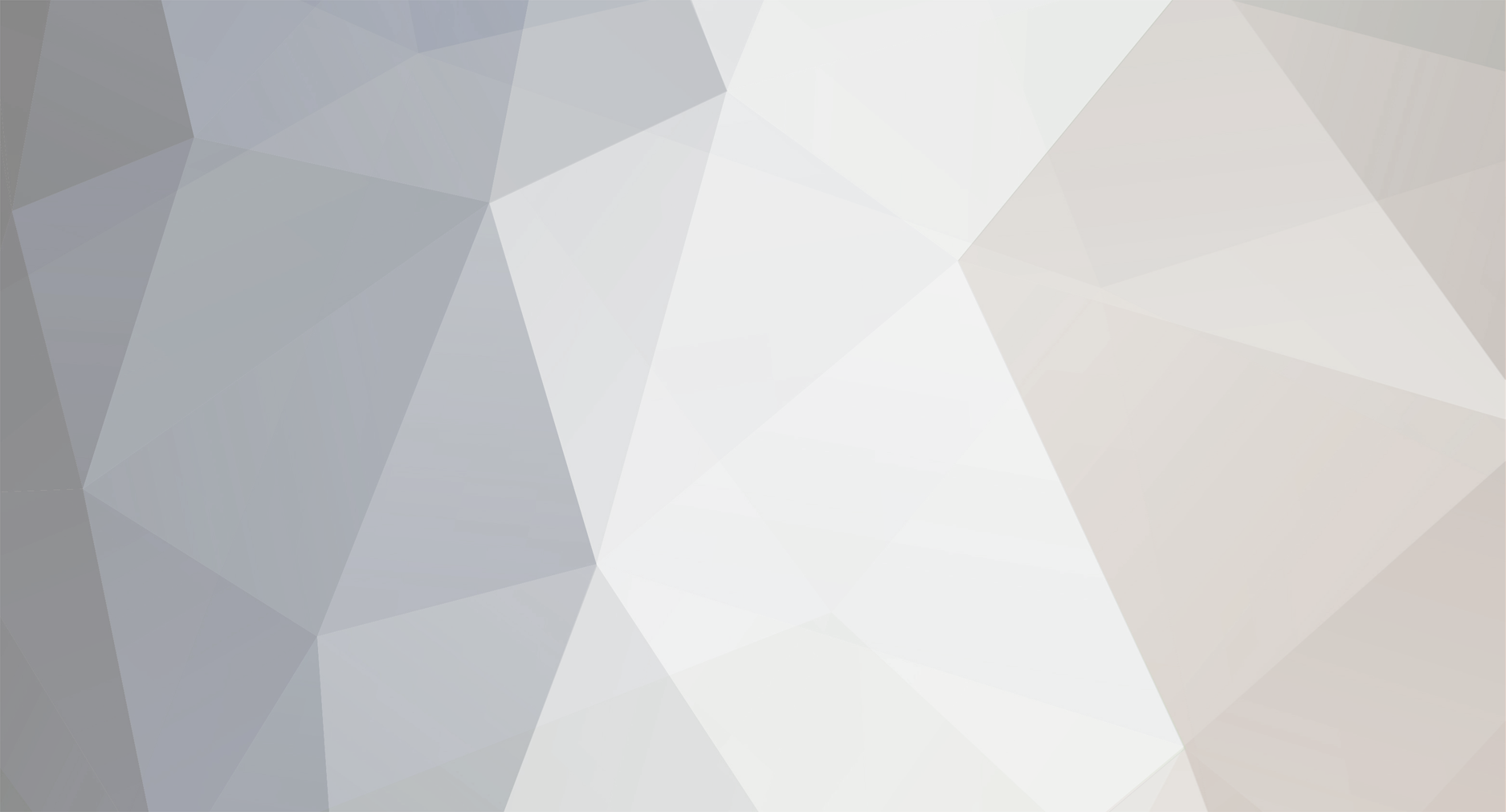
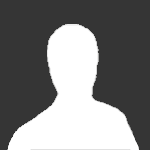
Steve Goddard
Member-
Posts
220 -
Joined
-
Last visited
Content Type
Profiles
Forums
Events
Gallery
Blogs
Store
Everything posted by Steve Goddard
-
Hi Just tried to update my build blog. Have 8 photos in the post but get the message too many pictures. Whats the limit and more to the point given that pictures are stored externally why is there a limit? As an aside can only seem to post the content in Chrome, IE hangs any ideas? Steve
-
I’ve failed on two fronts between this and the last post. First of all I didn’t keep to the new year resolution of a post a week, so that didn’t last too long Secondly I had all the stbd. side rear bulkhead cut and fitted in the last post. I got it all thicknessed the same, and glued up. It looked magic until……. it exploded . The workshop was obviously too cold for the glue and just as I was gluing the last (curved) piece in place I obviously got one of the cramps a little bit skew and the whole bloody thing just fell to bits. Although the glue had (in theory) had enough time to go off the cold weather meant that it had simply degraded and had no strength at all. So now I’ve got to start the glue up all over again. It’s also getting more and more difficult to get to the boat because of personal commitments and I feel at the moment that the fitout is starting to stall a bit. Hopefully I’ll get back into a position soon that I can really spend some time and kick it back into high gear. One job that I did manage to get done was to get the weatherboard fitted. The deckhead needed to be cut back round the hatch so that the weather board fits with the hatch surround. A reasonably simple job with a flush trimming cutter in the router and a bit of ply stuck to the steelwork with some double sided tape. The tulipwood cuts really well but it seems to make an absolutely enormous volume of chips. I was picking them out of my clothes and hair for the rest of the day and trust me I don’t have much hair . With that done the bottom of the weather board needs to be cut to fit to the swim. Now this is where you suddenly realise that life would be so much easier without a tapered swim as the fit at the bottom has to be one of the most complicated fitting jobs I’ve ever done as it slopes in every possible direction. The only way to get it anywhere near right is to template it on some 12mm mdf. It takes me quite a long time to get it near enough to allow me to transfer the measurements onto the weatherboard proper. The main cut is a real pain as the only way to get at it is to mount the weatherboard in the vice and then stand on the bench to make the cut. As you can see the saw is at a really awkward angle as well and you’re trying to keep the blade going down a line on both sides of the timber that are not square to the timber or even parallel. Great fun . Still I manage not to mess it up and some time with the block plane and a chisel soon has it fitting like a good ‘un. The next few days seem to be taken up with varnishing and painting as the weatherboard needs varnishing with an external varnish. I’m using International Schooner Gold which should be good given the price it is. It does give a nice finish but I’m really having difficulty as it seems to form the odd bubble on the surface which means it needs rubbing down and recoating. Not good. The galley doors also need more coats and the new table cupboard bulkheads needs painting AND varnishing. It all takes ages. Still Rex and I get the table cupboard bulkheads fitted anf fixed which is great as it’s the first time that the back cabin is not just one big space. We’ve also got the timber for the construction. Rather than using a softwood (it’s not really ever seen) we’ve got some nice Sapele which we cut and machine up so we’re all ready to start that soon. On top of that Rex gets the table cupboard front (which will in fact be a door) sorted, but more on that next time.
-
Fantastic. Were they expensive?
-
One week on ......Well near enough I’m not that far behind getting a post done within a week. As it is the week was a little bit short because of other commitments but we’ve made some good progress again. My first job was to finish off the bulkhead. It’s all a bit deja vu laminating up plywood. Takes me back to doing the conversion sheets. There’s only one side of the bulkhead that needs Padauk on as the inside will be painted. I’m back to the same situation again where I don’t have quite enough Padauk to do the whole of the side so I need to put an additional piece of ply where it won’t be seen (behind the fireproofing at the side of the range) which makes it a bit more complicated but at least it means I’ve got some decent edges to work to . With all the Padauk cut and shaped it’s time to glue up and throw it in the vacuum bag while the glue sets. A quick run through the sander and the jobs a good ‘un. Well it is from my point of view but although I’ve fitted the Padauk exactly to the bulkhead ply the cabin sides are at an angle to the bulkhead face so it no longer fits properly so Rex has a merry time refining the Padauk so the bulkhead fits properly again . After that I can drill some pocket holes to fix it up, get a holding coat of varnish on the Padauk and a coat of primer on the bare ply, then a coat of satinwood a day later and another coat of satinwood a day after that Next up is the weatherboard. Normally this would be a bit of ply but I’m making it out of solid Padauk. I’ve selected a pair of planks which match well in colour and grain so it’s just a matter of cutting a few biscuit slots and then glueing the two planks together. I love my panel clamps as you can always be certain that whatever your gluing up will be flat and straight. You still need loads of other clamps just to get the joint tight but it’s easy as you don’t have to worry about the boards moving. Rex is beavering away on the panelling around the soap ‘ole. It’s an interesting job as the angles are all funny which makes the joints quite time consuming to cut and get tight especially on the chamfers but as always Rex’s joints are nice, neat and as tight as a bull’s ….. in fly time . Although it’s not quite finished I couldn’t resist putting it up mjust to see what it’s going to look like and I do like the look of it I’m working on the stbd. bulkhead at the same time. I’ve already cut the bottom part plank so that it lines up with the bed box and the plank on the range side and put a nice little bead on the bottom to soften the edge. Then it’s just a case of sorting out the planks above it so I set the chop saw up to cut the side angle and cut a little wedge of plywood to set the angle for the cabin side on the disk sander and it’s then reasonably quick to cut and fit the planks. The only small issue is that some of the planks have not cleaned up properly when they’ve been machined up so I need to run them all through the sander to get them flat and the same thickness and can be fixed back properly. All that needs to be done now is to biscuit joint them and glue them up. (BTW I have made the little bit for the top just didn’t have it in the photo). The MAJOR plus point about this is that the very LAST of the sprayfoam is now (or will be when the bulkhead is fixed up) covered hobloodyray
-
Right most people will have realised by now that this blog is just a copy of my own blog site and that I normally copy my posts here after they've been on my site for a couple of weeks. I've got so behind now that I'm going to bring this blog bang in line with my other one and keep it that way. So there's actually going to be a couple of entries in this one so I hope that it's not too confusing I've just got round to starting a new post. Looking at the last one I realise that it's simply ages and ages since I wrote the last one. There have been so many things going on that a: I've not really been able to spend as much time at the boat as I would like to have done b: I've had no time to sit and write a blog. Oh well lets at least lets get it down now Right one of the big jobs we've tackled is the heating. With winter coming on I really wanted to get some proper heating into the boat so that I can keep the inside at a decent temperature and more importantly stop any excessive temperature swings inside which can lead to issues with the wood work. The range is all piped up and all that needs to be done is to fit the Thermaskirt which I'm using instead of radiators. In reality all that needs to be done is to sort out some woodwork to mount the Thermaskirt on and a couple of runs of pipework underneath the tug deck. The wood works pretty simple. On the stbd. side I've got to box in the main water feed from the tank so I've decided to make the other side match and to bring them out to the same dimension as the gunwales. This will give me a bit of an opportunity to put in some under gunwale furniture if I want to at a later date. The boxing is simply a 125mm upstand of 12mm ply with pockethole screws holding it down to the floor. It's actually really stable and doesn't need any other support which is good. I've actually painted the front face matt black so that it blends in with the Thermaskirt. for the top I've moulded up some more rosewood as a capping. One problem was that I hadn't really thought this out when I was doing he panelling under the gunwales and it would have been better it I had stopped the panelling where the capping went rather than taking it to the floor because if you butt up to the face of the board it looks odd because of the moulding. To get over this I've routed a little groove at the right height for the capping to slide in and with the skirting in place the end result looks pretty good. With the Thermaskirt in place down both sides of the saloon and one side of the bathroom David runs the copper pipe round under the tug deck and we're ready to fill it up and give it a go. The range gets up to temperature really quickly and the skirtings are remarkably hot in no time. Given that outside is brass monkeys (look at the picture of the stern fenders) the inside of the boat gets cosy and warm quickly and because the heat is well distributed there are no hot spots. Everybody who's been on board since the heating been on have been really impressed with how well the heatings working. Couldn't resist putting the kettle on the stove just to make a cuppa. I could live on board now . It's not been all stop on the back cabin either. Rex and I have got all the lining done on the range side and all the lining under the gunwales on the bed side. It all then come to a grinding halt as we've no material. I've decided to do a twist on a traditional back cabin and to use proper hardwood rather than scumble but the big decision is what wood to use. After a lot of checking around to see whats available and a couple of trips to woodyards to see what stock they have we settle on Padauk. The bulkheads and cabin sides will be veneered ply and all the rest will be solid. It's a pretty impressive pile of timber when it all arrives and it looks absolutely phenominal. The first boards to go up are the engine room bulkheads, Same procedure as always. Measure up the bulkhead, transfer it on to a bit of hardboard (or in this case some 4mm MDF which came over the veneered boards), play around with the template until it fits properly then transfer it to the board and make the final cut. Then if all is well it should fit perfectly which of course it does . Then its do it all again on the other side. With the bulkheads up I can start to see what the end effect will be and I really like it. Rex and I get the side linings up as well but as it's so late I don't get a photo but they are something special Will get a photo next time. Well Christmas has come and gone and the New Year is just round the corner so in an attempt to avoid terminal turkey overload I've retreated to my study and am determined to get the blog up to date. There's been quite a lot of work done on Siskin since the last post but you wouldn't necessarily know it just looking at the pictures. The main thing is that the sidebed side liners are now up and everything has had three coats of varnish which will keep it stable until I get the framing on and can finish it properly. It will need at least another three if not more. With the sides up the cabin looks bigger for some unknown reason and best of all nearly all of the hateful foam-spray is now hidden. That in itself is a major bonus. I make a start on the rear bulkhead on the range side. It's 18mm solid padauk. It's a bit of a nightmare to get the planks fitting well as it's all compound angles and of course every board is different. Trimming the end grain is a nightmare. It's as tough as old boots and simply will not cut clean even with a low angle block plane. Rex has a brainwave. It turns out that there is a 12″ pedestal sander under a pile of stuff in the store above the main workshop so we dig it out and a quick trip to Axminster to get some abrasive and we're in business. Man what a difference I can make the slightest adjustments to the ends of the boards easily and quickly and it doesn't take too long to get them cut, fitted and then biscuit jointed together. They look pretty good held up with a clamp . The framing for the soap 'ole is the next challenge Rex in the meantime has been working on getting the table cupboard bulkheads cut and fitted. We're making them out of 12mm birch ply which you may think is a bit thin but given that they will be clad in 12mm padauk they will be more than adequate. Again it's one of those "simple" jobs that just take ages but as I've found to my cost with the shower bulkhead it's imperative that they fit perfectly so you don't get any distortion when they're fixed in place. With both bulkhead up the cabin suddenly has a real shape. While Rex has been working on the bulkheads I've been making a little " foot box" to go under the counter for the foot end of the sidebed. It's simply 18mm birch pocketholed together. Of course it's even more fiddly than the bulkhead as there's not a right angle anywhere that it touches and to make life difficult I'm rather too large to fit comfortably under the counter. Still when I've got it templated and cut out I can give it a coat of primer and a couple of coats of satinwood prior to fitting. The pocket holes will have plugs in them and painted over when it's fitted so they won't be visible. When I come round to fitting it it's slightly out at the top front corner (about 2mm) when I've fixed it down properly. Fortunatley there is a little fillet to go over that corner to conceal a cable run so it wont be seen PHEW as I didn't fancy trying to fix it as it would have been a major job. I'd planned to do a bit of work on getting the bulkheads finished over the Christmas holidays and took all the bits home so I could machine up the timber and laminate the bulkheads. I got the first bit machined up and then bugger me the drive belt on my thickness planer broke. That's the second one in 31 years things just don't last like they used to. It's a standard belt but of course finding somebody who has on AND is open between Christmas and the new year proves to be a fruitless task. So I've ordered two (one for a spare which undoubtabley, if I last as long as the first belt, I will then be unable to find). I guess they'll arrive after new year. Still I've got one piece machined up so I can at least get that glued to the bulkhead. As it's a little bit banana'y I need loads and loads of clamps to make certain it goes down straight but it works. Now here's my first new year resolution. I will get a weekly post on the blog Honest. Lets hope we all get some good boating in in 2013
-
Andy Thanks. Your boat is looking fantastic to and by the look of it you'll be on the water well before me . Have a great new year and I'll see you on the water next year Steve
-
Thanks for the good wishes. Saw Richard at the historic boat show but he was on board and I was on the bank so if you see him give him my regards Steve
-
Well it’s starting to happen, I’m finally getting to cover up the last bits of foam. It’s not all done yet but I think the end is in sight. Having said that I still seem to be cutting back masses of the stuff. Ho hum…. Before I start the lining I need to do something with the filler pipe for the water tank under the floor. When we put it in we simply routed it in the most convienient way which is great at the time but it poses a real problem to sorting out the lining around it. Thje big problem is that with 1 ½” pipe you simply can’t put a tight bend in it and really it needs three. The answers quite simple just get hold of some 1 ½” plastic elbows and lots and lots of hi grip jubilee clips ( two per end) to ensure that there will be no leaks. The resulting job is nice and neat and tucks the pipe well out of the way so it’s a lot easier to figure out how the lining will go. The next bit of the lining to go up are the bits up the side of the swim. These are fitted at the bottom to a batten screwed to the floor. I’ve measured the angle of the swim to the floor along it’s length and taken an average so that I can put a bevel on the front of the batten which is roughly parallel to the swim side. It’s amazing how much the angle changes over the length of the swim. If you didn’t have a tapered swim this bit would be a whole lot easier . Next job is to cut the sheet. You would think that it’s a pretty easy job, measure one end, measure the other and a couple of cuts would do the job. Oh no not at all. Because the sheet curves in three dimensions there are actually no straight edges on it at all and the easiest way is to scribe a template of the bottom edge on a sheet of hardboard and get that to fit, cut the bottom of the sheet and fit it leaving the top edge well oversize and deal with that later. It takes Rex and I half a day to get it right but it’s well worth the effort. I’ve got to put some little bits of floor under the counter for the foot of the side bed and to make a little bit of storage on the range side. I put some battens in before spray foaming but yet again the shapes are a nightmare and it takes a lot of fiddling about to get a decent fit. The little triangular piece fills in the middle and will be removable to allow easy access to the stern gland so that if I ever need to remove it I have some reasonable access. After this the sheet under the gunwales is pretty easy to do as it only really curves in one dimension so you can actually cut it direct from a series of measurements. One thing that I had to do was to make a little batten for the front as there was no where to fix the sheet to. Not a great bit of forward planning but it didn’t take a lot of effort as it’s simply a bit of ply cut to the right shape and a batten fixed to it. With that in place it’s a pretty simple job to fit the sheet under the gunwale (after painting the back of course). It’s then repeat all of above for the other side. With the sheets up under the gunwales and another little batten fixed to the bottom of the sheet it’s time to tackle the top of the sheets up the swim. The challenge is to get the top of the sheet up the swim to the right shape so that the sheet on the top of the swim is level (I hope that makes sense ). In the end we find the easiest way is to use a rip saw and make a cut down the swim sheet until the saw blade is horizontal when it is resting on the batten at the bottom of the gunwale sheet (it a lot easier and clearer when you’re actually doing it believe me). With a set of cuts done it’s simply a matter of joining the dots and Bob’s your uncle. Cutting the top sheet is reasonably easy as at least it’s flat so it’s simply a matter of scribing round and jigsawing out. The sheets are screwed onto the batten on the gunwale sheet and glued and pinned onto the swim sheet which takes a bit of care to ensure that the pins do not come out the front of the sheet. The pliers in the picture point to the fact that I missed with two of the pins . There’s a little bit of excitement on one of the days as there’s a load of boat lifts going on and one of them is lifting Dane out to go over to Alvechurch to be renovated. Given that she’s and all wooden boat and the keelson is rotten there’s a lot of concern that she might bend/break as soon as shes lifted out of the water so loads of extra care is taken with extra slings to ensure that there is not an embarrassing failure and a load of expensive firewood left on the dock side. As always though Barry does a super job and Dane is soon on the lorry to start her journey. Next thing is to get the back bulkhead up behind the soap ‘ole. After all the complex sheets this is a doddle and Rex soon has it cut out so I can paint the back and then glue and pin it in place. Again I’ve missed battens out for the ends of the cabin side sheet so it’s fix a little batten to the bulkhead before we can start on the cabin side sheet. The cabin side sheet is 4″ longer than a standard 8′ sheet (bugger) so Rex routs a little half lap joint on the end of the sheet and glues on a 4″ strip. Now I’m a belt, braces and bit of string guy so I’m not certain how strong that joint is going to be but any fears are banished given that it gets really bent and twisted as we fitt the sheet and despite what I feared it shows no sign of falling apart and that’s only 20 mins after gluing up (don’t you just love polyurethane glue ). With the sheet in place it’s down to me to clear the cabin out, sand all the sheets to get rid of the foot prints etc so that the lining can be primed and painted. As an extra precaution I run a little bead of Sikaflex round the joints. Not only does this tidy up the joints but it also gives a seal against moisture getting in the end grain. After this it’s simply a case of getting the mini roller out and getting everything primed. When that’s done the cabin is starting to look a whole lot nicer. Rex even says I could move in but I think that’s a bit premature
-
Well as Churchill said “This is not the end, this is not even the beginning of the end but it is, perhaps, the end of the beginning”. I really feel that we’re on the last bits of the build as we start to get some timber fixed in the back cabin. I know that there is still loads of stuff to be done in the main cabin and bathroom but it does feel that I’m on the downhill run now. First task is to get the floor down. The sides of the floor will be 18mm birch ply and the center lift up sections will be 6mm birch with some Kwila floorboards I have knocking around. I should look quite nice when it’s done. The port sides quite easy as there are no pipes or electrics going down the swim sides so it’s just a matter of marking up every foot along the center bearer and then measuring to the swim, transferring all these measurements to the ply and cutting it to shape with the jig saw. It’s not a bad fit first time round but I’ve got it a bit wrong at the stern so it takes a little bit of scribing to get it to fit properly. The stbd. side is a bit more complicated as there are all manner of things going through the floor that need cut outs and even a little hatch so that I can get to one of the isolating valves for the skin tank. Still it goes to keep you busy . With the sides cut and fitting I trim the existing bit of rough old ply so that it fits down the center section as I don’t want to put the proper floor down while we’re working in there. Every thing then gets a coat of cuprinol and a coat of red oxide on the underside. Magic. With every thing in place it’s only a matter of screwing it down to the bearers. I started off trying to use Tec screws but they really were no good at all so in the end I drilled and tapped all the fixing holes 5mm and used some countersunk stainless machine screws. The finished job is a lot better than Tec screws and if the truth is known didn’t take much longer to do. You live and learn. There’s lot of little fiddly bits to sort out, reroute the water filler pipe, move some of the wiring, remove the engine control, patch up the sprayfoam (by the way, if there is a bubble in the sprayfoam where it has not stuck to the cabin side DO NOT cut it out and try to patch it, leave it there, poke a hole in it and squirt the foam in throught the hole. A great deal easier ans a lot less messy), cut back the spray foam AGAIN and so on and so on. Before you know it the weeks almost gone and Rex and I have half a day to start on the ceiling. Still we manage to get about half the ceiling up so were moving forward.
-
Boat painting by the lower priced painters.
Steve Goddard replied to Boat&Bikes's topic in Boat Building & Maintenance
John did my boat a couple of months back. I can vouch for the quality and care that he takes in painting a boat as I worked with him while he did mine. You can see the whole process either in the NB Siskin build blog on these forums or at NB Siskin. Over the six weeks I worked with John and the week with Phil Speight I learned far to much about paint systems than is necessary but now at least understand why it is impossible to absolutely guarantee a paint job (given that canal boats are not painted in the highly expensive controlled conditions that cars are) and that the best a painter can do is to follow the paint manufacturers recommendations with regards to conditions (temperature, humidity etc), paint thickness and preparation. I for one would not like to try to make a living out of painting boats. BTW like all things if you look after your paintwork properly then it will last longer than if you don't. -
Well it’s only a week since the last post. What on earth has gone wrong The weeks basically been spent on two things: continuing on with the cupboard doors for the galley and sorting out so that we can start work on the back cabin. I love doing the fiddly woodworking stuff. I really do find it relaxing and fulfilling and it’s makes a change from doing stuff I’m not to sure of how to do it correctly. once all the component parts of the doors are machined the first job is to glue the bubinga edging to the rosewood. It’s pretty easy on the rails but the stiles take a bit more fiddling to make certain that they are in the right place. I’m pretty satisfied when the’re all glued up as they fit really well and won’t need a lot of sanding to get them perfectly flat across the join. I’m fortunate that I have a little drum sander bought when I had a bit of extra cash and its a nice simple job to run all the bits through so that they are flat and all exactly the same thickness which will make assembly easier. Considering that these are less than half the doors I need to make there are an awful lot of bits when you stack them all together As there’s lots of time while the glues drying etc. I’ve still got plenty of time over at the boat. The first day I’m over seems to be a dream day as I rattle throught the jobs I’ve got on the list. Most of the pull out units have now arrived for the galley cabinets. I’m using these in an attempt to maximise the usage of space as you can never get to the back of cupboards and there always seems to be something vaguely unpleasant lurking there if you can’t get in easily. The pull out units fall into place and work first time and in less than a couple of hours there all in place. What a result . They now represent what must be the most expensive pull out tool storage in the world The next little job is one of those that you just love. It’s easy, it’s quick, there is minimal chance of screwing up and the end result is lovely. I’ve finally manged to source a Sika thermometer for the engine at what I think is a reasonable price (£52 inc. postage) and as it was made to fit it’s simple to fit it. With it fitted it’s a good excuse to crank up the engine to see if it’s working and it soon settles down to a constant 62°C reading which given that it’s a 64° thermostat seems reasonable. At least now I can see what the engines doing to get it set up properly. now it’s on to the back cabin. It doesn’t take long to string some cable round the place because theres not a lot of wiring in there but then it’s back to cutting back the dreaded spray foam AGAIN. I really did think that I had finished with this crap. At the end of the day I’ve filled a bag with offcuts of foam, got bits all in what little hair I’ve got and generally lost any good humour I had, And to make it worse I know that I’ll probably have loads more to do when I start fitting the paneling. Oh well at least when this is done it’s really finished. One thing I do find however is a couple of little areas where the spray foam has not stuck to the cabin side and there’s a bit of a bubble. I reckon that the best approach is to cut it back till it’s sound and them patch it with some squirty foam from a can. With a couple of days out to help my daughter move house it’s a short week but by the end of it I feel that I’ve actually got a lot done
-
Here we go again trying to remember whats been going on for the last few weeks . It’s quite easy really we lifted Siskin back into the water and I spent a week round at Debdale finishing off the last few bits and bobs before setting off back to Brinklow and moving all the tools and stuff out of the boat. Now it took three car loads to get everything out and as I just dumped it in the workshop at home I soon had an empty boat but a workshop you couldn’t get in . With the inside of Siskin all clear she’s suddenly developed a marked list to stbd. which given that the majority of the galley and the calorifier is on the stbd. side it’s not surprising. It’s nice because I can just pull the ballast out of two bays in the galley and temporarily stack it on the port side under the tug deck which levels everything up nicely. With everything working properly (apparently) the crew, in the shape of my grandson Corin and Rich his dad arrive down on Friday morning to set off back to Brinklow. The weather is a bit cool but pleasant enough as we head off to Foxton joined on this leg of the trip by MMM and his dad. We arrive at the bottom of the locks just as the lock keeper is heading off to lunch but he has no issue with us going up on our own so we head straight into the locks and away we go. Got to be a first not having to queue Corin is determined to work the locks and to give credit where credit is due does a pretty good job and even remembers the order for the paddles. Smart lad . Will have him on board again . Mark and Joe bid us farewell at the top lock and we head off towards Bosworth where we are planning to moor up for the night. Siskin is working really well, the alternator is charging and since I’ve put the mixing valve in the engine cooling circuit the engine is running at a decent temperature and we’re even making hot water. It’s almost like areal boat. We arrive at Bosworth tunnel and try to get to the bank to moor but despite the water being up there is so much crud that we can’t get within three foot without being hard aground. Not deterred we decide to move on and moor up near North Kilworth but when we turn on the tunnel light nothing happens. Bugger I had some trouble getting it going with the socket shorting out (it’s a bit on the small size) so I head into the tunnel with just the cabin lights on and nearly make it all the way to the other end without clouting the side. Still fortunatley the only thing that’s damaged beside my pride is a bit of blacking. Saturday sees us getting an early start and we’ve arrived and moored up at the Crick tunnel by lunchtime so it’s out with the tools and tackle the problematic tunnel light. An hour later and I’m still none the wiser as it keeps tripping the software fuse. The last thing I actually look at is the bulb and am mortified to find that it’s a 12v bulb. I reckon I’ve had a real senior moment when I was sorting the light out and taken the 12v bulb out of the light only to put it back in rather than the new 24v one I had bought . As there is no hope in getting a 24v bulb in Crick and there’s nobody we can ring to come get us we decide to call it quits and leave the boat and I’ll get the proper bulb and sort it out during the week. However there is always a silver lining and we went and ate at The Moorings. Nice place, good food and a decent price Monday and I check the other bulb for the tunnel light and that’s 12v as well but the box definitely says 24v odd indeed so it’s back round to do my impression of the dead parrot sketch at the shop where I bought it. The guy I spoke to was very sceptical till he went and got another one which was also a 12v bulb in a 24v box. In fact when we checked all their stock over 50% were wrong. With the right bulb in the tunnel light everything works properly Oh well. Chris and I get the boat round to Brinklow the following weekend. Saturday was a wonderful day but on Sunday it absolutely pissed it down and by the time we got round to Brinklow I was soaked and freezing still it was nice to be boating The rest of the week is spent catching up on loads of stuff and making a start on machining up the timber for the galley doors. The’re a little bit complicated because I’m rapidly running out of rosewood so I’m using a bubinga lipping on the inside of a rosewood frame. I think this will look great but it means that there is an awful lot of cutting machining and gluing to do and with a total of eight doors for the cabinets alone it’s going to take some time. Still I hope that they will look OK.
-
I can’t believe that it’s been three weeks since I’ve posted a blog. Where has the time gone? more importantly why can’t I remember what I’ve been doing again Well the first week was taken up with finishing off the paint job. You think that you’ve finished everything and then you come across all the little fiddly bits that needs doing and you suddenly find that there are not enough hours in the day. Still by Saturday the painting is finished and Siskin looks great. There are just a couple of little bits of blacking that need doing but I’ll sort that out when I lift the boat back out of the water to fit the prop. For once we’re right on time as Phil is arriving on Sunday to start the signwriting on Monday morning. Brilliant. Monday arrives and we’re over at the boat yard bright and early to pole Siskin round to the other workshop so John can get the next boat in and started. Oh dear, oh dear oh dear there has been a monumental cock up and there is no space in the workshop. This looks like a complete disaster until John comes to the rescue and says we can stay in his dock for a week and he’ll take some time off. The guy is a real gentleman and a star. The first thing that Phil and I do (after a cuppa) is to look through all the pictures I have ammased to try and decide on exactly what we’re going to do. It’s very interesting as it’s obvious over the life of the original boats that there were all sorts of differences in the signwriting over the length of their lives but we eventually decide seriph letters for Manchester with a capital M only and Ltd in capitals rather than the capital L and lower case t and d and finally the style of the scrolls. With all that sorted Phil lays out some tape for the curves of the letters, roughs out the position of them with a chinagraph pencil and then gets straight into painting. I’m always in awe of anybody who can do something that I think is so hard and make it look so bloody simple. It’s just not fair With the stbd side main panel done Phil moves on the the forward panel which has the name on. The original boats also had silhouette of the bird they were named after on panel. The majority of opionion is that these were chromed and not brass as perhaps you would expect so I’m going to get a couple laser cut out of polished stainless which should be a lot more practical.. However as I’ve not got these done yet Phil has to make do with a cardboard cut out stuck to the panel with masking tape so he can layout the signwriting. Once it’s laid out Phils straight at it and by the end of the first day we have (that a royal we by the way as all I can do to facilitate things is to keep the kettle on the boil ) the first coat of lettering on the whole of the stbd side including the inside of the engine room doors so that it does not obscure the name when the door is open. Signwriting then becomes just like painting in that you get to do it all over again of the other side of the boat, then you get to put the drop shadows in, then you get to paint the lettering with a second coat and before you know it the week has gone. Saturday morning and Phil makes a start on the castles on the stern panels. Again it’s amazing as he knocks them out in three and a half hours each and they are brilliant. The’re different on each side and if I’m honest I prefer the one on the port side if only because there is a little message in it about one of my favorite pubs on the cut. Sunday morning and the second coat of varnish goes on the castles and the first one onto the other panels and then Phils back off to the highlands Monday morning of week three and it’s back to reality. John and I pole Siskin back to the slip so that I can get her lifted out to get the prop on which is done with very little fuss at all. Next is to mix up some two pack black and get it on the bottom rubbing band on the counter and a few little bits that need touching up because of paint splashes or just where I didn’t put enough on when I blacked her Tuesday is a catch up day on the rest of life. Get the car MOTed, go to the bank all the sorts of things that don’t get done while you’re painting. Wednesday and David is around to help me get Siskin ready to cruise again. He starts off sorting out the battery and alternator cables which are 50mm and a real pain to wortk with. While he’s doing that I’m filling up the water tanks and calibrating the tank senders and then it’s time to let some water into the system. Now I’ve expressed my thoughts about plumbing before and how I always have issues when I turn water on. Well I’m glad to report that this time there were no (well nearly no) leaks. The only little on was a compression fitting on one of the calorifier coils which needs to be tightened a bit. We have water at the taps bliss and after a little bit we even have HOT water at the taps as the immersion works so the cups get a good washing up. . Next thing for me is the loo which is pretty simple once we’ve bent up a bit of 15mm pipe to replace the plastic one which so offended me and run some power to the pump. With the loo working and after an inaugural pee (well you have to dont you ) I’m off down tp HAMS in town to pick up some fan belts. Now I’ve calculated that they need to be 73/74″ long which seems to be a right after we’ve run a tape round the pullies. Back with one 74″ belt (it’s all Nick had) and it becomes apparent thet it’s far too long so back into town again and armed with a 72″ and a 70″ belt we finally find that the 72″ is perfect. What a palaver especially as Nick only has one of those as well so I’ve still got to wait for the second one. Thursday and David has finished all the wiring, we’ve got one belt on so we reckon that we can start the engine and check that the alternator is charging. As I’d had the engine running on monday I thought it would be simple. Oh no not at all. We simply could not get it going and the problem seemed to be no fuel up at the injection pump. Two hours later after I’ve stripped and cleaned the lift pump and David has gone all through the pipework looking for leaks we finally get it going without really finding anything obvious causing the issue. Still with the engine running we can check the alternator and it seems to be working properly although the readings off the Mastershunt are a bit different to the ones off the meters so we’ll have to sort that out at some time. Next job is to fit some little LED’s into the cants on the tug deck so that we’ve got some light when we stagger back from the pub. They clip in and I’ve used Sikaflex to seal them so they should be waterproof. Final job of the week (off to a wedding on Friday) is to fix one of the stainless Siskins in place. Now the side of the boat is complete and I am a very very happy bunny
-
Chris saw you last week scabbling the roof of a boat in your dock. I'll say it again it's not easy at all and you earn your money mate. Steve Thanks I'm glad you're enjoying the blog its fun to write as well. watch this space for the further adventures of Siskin Steve
-
Monday watching paint dry Tuesday watching paint dry Wednesday watching paint dry Blimey this painting larks a doddle. I could sit and watch paint dry all day Well if the truth is known I was watching the paint dry from Liverpool . I don’t know that I’d ever been to Liverpool before but I was really impressed. It’s a nice city center, lots of good restaurants and decent pubs and loads of things to see and do. A nice break. Thursday sees us back on the boat and it’s time to rub it all down. Gawd what a soul destroying job. The big flat panels aren’t to bad as they can be knocked back with the orbital sander and some 320 grit paper but all the small detail stuff round the rivets, hinges and anywhere else you can’t get the machine are a pain. First get the pattern out of the paint with 240, then get it smooth with 320 and then tidy it up with Scotchbrite. It seems to go on forever and in fact it takes John and I two and a half days to get it sanded to Johns satisfaction, cleaned with the vac, wiped down with degreaser and finally tack clothed so that it’s ready to start painting. I can now start to understand why getting a good paint job is an expensive exercise, it’s simply the amount of effort required. Again I’m REALLY glad I’m not doing this on my own. Saturday and the first bit of gloss that John puts on is the black on the back cabin stbd. side and the transformation is amazing. I know it’s only the first coat and there is a long way to go yet but the finish is great and the lift that the boat gets from having gloss paint (however little) on is tremendous. John continues on with glossing getting a coat of Manchester red on the panels on the port side and it’s so exciting. I just can’t wait to see it all done. Now you may be thinking that while all this is going on I’ve been living the royal life with my feet up watching John get on with it. How wrong could you be. I’ve been back on all the fiddly bits (letter box vents, mushrooms, engine room slides, deck lid, pigeon box and hatches) and trust me they are fiddly. It’s very difficult especially round the rivets and fitting to ensure that you don’t get any runs and to be honest the odd one is inevitable so heres a tip. Don’t try to rub them down to flatten them simply get a SHARP Stanley knife blade and use it like a plane iron to cut the run off and you end up with a very smooth and quick job. At least now I’m not just painting in grey but have a wide and varied pallet (well grey, black, Manchester red and Raddle red) and all the little bits start looking good. I just hope that I’ve painted them the right colours. With all the little bits out of the way I’ve just got time to layout the white squares on the hatches and get a coat of white undercoat on. Smoking Sunday is a repeat of Saturday for me and John is carrying on getting gloss on more and more of the boat. Just wished I’d remembered to take some pictures. Next time. Well one thing I can say about painting is that it really doesn’t lend itself to blogging . You work and work all day long and for the majority of the time all you have to show at the end of the day is…….. exactly the same thing that you had at the beginning of the day. Normally the most exciting thing in the day is what you have for lunch and that really doesn’t make for riveting reading Still in the time since the last post we’ve moved on quite a lot and all being well the boat should be finished by the bank holiday Monday. The nice thing about it now is that things are really getting finished i.e. after a top coat has been applied it no longer needs to be rubbed down again and repainted. Apart from the fact that this means bits of the boat don’t seem to go backwards as the day progresses it also means that there is less to paint each day so more seems to get done (if that makes any sense at all). The cabin sides are the first things that are finally finished and I can start to think about fitting brightwork back on. The only issue is that the brightwork is no longer very bright. However there is a cunning plan as my grand daughter is looking for ways to earn money for her school trip to New York so with some negotiation we agree on a price and she sets to polishing. I have to say she does a fantastic job in record time so I’ve even got some time to fit the portholes which really does make the boat start to look as if it is finished. Another job I’ve been putting off for a while is sorting out a new alternator pulley for the crankshaft as the one which was on the engine was too small and would not drive my alternator fast enough at cruising speed. Fortunately the pulley is on a taper lock so I can buy an off the shelf one (from Bearing Boys). I’m actually amazed at the cost as the new pulley, taperlock bearing and postage is just over 60 quid. Bargain. So its one more thing that needs three coats of primer, three coats of undercoat and three coats of top coat plus detailing. Oh well As I said more and more of Siskin is starting to look finished. The Manchester red panels and black framing is finished on the back cabin and the yellow coach lines on the mouldings are taped up and in undercoat so we can start to see what the final effect might be. You can also see the bunny ears on the back bulkhead which as far as I can make out from old photos are how the boats originally came out of Yarwoods. Certainly as you look at pictures over the years it’s clear that there were all sorts of different shapes, combinations of colours and coach lines used. Again round the counter I’ve tried as much as I can to keep to the original paint scheme (well as much as you can from looking at black and white photos) with a single white tunnel band and a three colour rams head although I guess that the center colour should be white rather than yellow but with the yellow if matches the back cabin colours . While John’s doing all the tricky bits I can carry on with the bits that nobody sees ( an astute comment on my painting skills I feel). I’ve finally modified the cupboard for the electrics in the engine room so that it fits properly so now guess what? Yep three coats of everything again. Well the next post should see the boat finished which is very exciting and even more exciting is that Phil starts the sign-writing the day after I can’t wait
-
Well the time has finally come to start and get some paint on Siskin and I can’t wait Before we can start painting however John needs to check that conditions are in line with the paint manufacturers specs. He’s got a set of digital instruments which measure the temperature of the steel, the humidity of the air and calculates the dew point. Providing that the steel temp is at least 5°C above the dew point it’s OK to paint Given that the steel is practically at the air temperature we’re 7°C to the good and we can start. Woo Hoo!!!! Right the plan is to put 3 coats of primer on and then 3 coats of undercoat. It doesn’t sound a lot until you look at the amount of boat you have to paint and then it starts to get a bit daunting. However with the two of us working on opposite sides of the boat it’s surprising how quickly you can get on. John keeps checking with a little comb affair to ensure that the wet film thickness is OK and we soldier on. For the primer and undercoat we’re using little 4″ foam rollers as it’s all going to be rubbed down before we start on the top coat anyway. It’s actually amazing how good a finish you can get with a decent paint. While Johns tackling the big bits I’m working on the bits and bobs. All the wood slides are getting three coats of International Yacht primer and the cast bits (letterbox vents, mushroom vents etc.) are getting three coats of etch primer. John can paint both sides of the boat in the same time it takes me to do all the fiddly bits By the end of the day the whole boat has had a coat of primer, grey on everything but the back cabin roof which is in red and the tug deck which is in two pack and Siskin is looking a whole lot tidier than she was at the beginning of the day. Day two arrives and believe it or not it’s a repeat of day one without the benefit of seeing any progress as we’re just going over what we did on day one . The rational is that if you re-coat primer / undercoat within 24 hours the solvents in the paint have not fully evaporated and the new coat of paint will ” reactivate” the surface so that you get a good bond between the two paints. If you leave it any longer then to get a good bond you really need to rub it down to provide the key. Day three, deja vu same as day one and surprise surprise day two. At the end of the day the boat has had three coats of primer over most of it and we’ve used over 10l of the stuff and there’s still more to go Day four and it’s colour day . Well it is for some as I’m still on grey primer on some of the bits and bobs. First thing is the roof which is in Raddle (grey on the front cabin and red on the back cabin) as this goes directly onto the primer (it’s all a bit complicated). So it’s another day of a: trying to remember what colours are going where and b: working out a sequence to paint everything in so that we’re not rubbing against wet paint. That at least is helped by the fact that the paint dries really quickly i.e, the front of the roof is touch dry by the time you get to the back. John and I have got into a nice routine now and we keep out of each others way but still manage to keep working. As the day progresses Siskin starts to look more and more like she will when the job is finished. The aft panels on the back cabin are in white because they will eventually have Castles painted on them and we’ll do the yellow moulding around the panels when all the top coats have been finished. We carry on working straight through Saturday (I’ve come to realise that the paint dictates when you can and can’t work) so by the end of play on Saturday the whole boat (more or less) has had a total of six coats on paint on and I don’t think that that’s bad at all. I’m now really glad that I didn’t end up painting the boat myself. I think I had REALLY underestimated how much work is involved and what you need to do to get a decent job. I know that Siskin will now get the paint job she deserves. Having worked six days solid on the boat we’re both ready for a break, plus the fact that we need to give the paint at least three days to properly harden off before we start to rub it down in preparation for the top coats so we decide to leave the boat until next thursday before we start work again, so John heading off to do a bit of fishing and Chris and I are heading up to Liverpool for a few days. Normal service will be resumed as soon as possible
-
Monday arrives and it’s pouring down (what a surprise) still for once I’ve got a whole raft of little jobs I can do inside the boat so it’s no big problem. The first is to finish off the plumbing for the feed pump to the loo. As I’ve not got a pipe bender I can’t bend up a piece of copper to the angle of the swim so it looks a bit awkward when I’ve finished. I’ll bend up a bit of copper when I have the chance but at least I’m in a position where I can fire up the loo if I want to. Next job is to fit the fresh water tank sender. I have a bit of a struggle in getting the 22-22-15 tee out to replace it with a 22-22-22 but once that is done it’s a pretty simple job to fit the sender and wire it up. A couple of P clips onto the front bulkhead batten and some cable ties to secure the flexible conduit and the job looks nice and neat. With it all connected I can fire up the PC and sure enough I can now see the sender and calibrate it for an empty tank . All I need to do now is to calibrate it when the tank is filled and it’s complete. Easy job. I’m just wondering what to tackle next when Mike pops his head in the hatch and asks if we can move the boat down to the slip as there is a break in the weather. So twenty minutes later Siskin is off on her travels again. Again it seems surreal not to see Siskin behind the container after all the time she’s been there but it is very exciting indeed. We get Siskin down to the slip and sorted out on the trestles just in time for my mate Dave ( the plumber) to come and fit the Thermostatic Mixing Valve on the cooling system. Hopefully this will allow me to manage the temperature a bit better and stop the engine from running so cold. We’ll see when we get going. The plan for Tuesday is to get a second coat of black on the hull and sort out the boat ready to go in the paint dock on Wednesday. Good job that’s all I had to do as a guy turned up to check all the lifting gear and as Siskin was still hooked up to the gantry crane I couldn’t do any thing until he had finished checking it. Still I took the opportunity to savor the high rise living while the boat was on the high trestles. I could quite get used to having a penthouse boat . I did manage however to get the hull blacked again before the end of play. Wednesday morning and Johns round first thing to give us a hand to get the boat round to the paint dock. Doing our best impression of a pair of Gondoliers we pole Siskin round to the dock and despite a strong cross wind we get her in the dock without hitting anything The rest of the morning is taken up stripping all the brightwork and removable stuff off Siskin and masking up all the portholes etc. and come lunch time we’re ready to start and rub her down. As we’re about to start the heavens open and it absolutely buckets it down. Do I give a flying f…ig? no I don’t as I’m basking in the luxury of working inside in the warm and dry for the first time since I’ve started work on Siskin…. Bliss Not really much to write about for the next two and a half days as John and I start to get Siskin ready for paint. We’ve made the decision that if the primer looks suspect at all then it’s back to bare metal so it’s just a steady old job working methodically round the boat with the sanders until John is happy with the surface. By the end of Friday we think we’ve broken the back of the prep work with all the major surfaces sanded back and all round the detail stuff (who the hell put all those rivets on) hand sanded down and cleaned up. Seeing the amount of work that it takes to prep the boat I’m now rather glad that I’m not doing it on my own. can’t wait for next week when hopefully we’ll start to get some paint back on Siskin so that she doesn’t look all spotty
-
There has been a major change of plans and its happened all of a sudden. Originally I was intending to paint the outside of Siskin myself and had hoped to use the paint shop Mike is building with the deadline of getting Siskin back on the water before the winter stoppages so that I could motor back to Brinklow and make a start on the back cabin. However the paint shop is taking longer than expected and its now obvious that if I wait for the paint shop I’m going to miss that deadline. I had talked earlier to John Barnard about working with him to paint the boat but he had no slots available till next year. Imagine my surprise when he came and said that he had had a last minute cancellation and if I wanted to I could get into the dock this week. Gulp!! I had planned a pretty relaxed week mooching around getting the service cupboard for the engine room sorted out and fixing some bits of trim around the place and the first thing that I had made was the door for the cupboard. It’s pretty simple construction just a sheet of 8mm ply with a 12 mm ply chamfered frame glued and pinned on. As you can see from the picture there’s actually shadows on the ground so it can’t have been raining . A quick coat of primer and that’s as much as I can get done on the door for the day so it’s time to get some undercoat on the cupboard itself. Next job is to get the prop off so that I can get it back to CJR in Southampton to see if I can get it re-pitched. The nut comes off pretty easily but the prop is good and tight and even with a couple of hardwood wedges behind the prop there is simply no way that I can shift it . A quick visit to see if Mike has anything that could help and Steve pops along with a bearing splitter which they have modified so that there are three threaded rods which fit between the bats on the blade and through a steel plate which goes over the end of the shaft. With the rods tightened as hard as we can get them the blade still refuses to shift despite the fact that it was greased up before I put it on and it’s only been in the water for a few days. We leave it for a while to get lunch and afterwards I get a lump hammer and with a couple of good wacks the prop pops off the shaft. Result . Tuesday sees me in the car bright and early and off to Southampton to CJR. Speaking to Andy there he’s pretty confident that they can do what I want so I leave the prop and head back. I really wish that I’d done this earlier as it means that Siskin will be lifted into the water to go to the paint dock and then lifted back out again to fit the prop as there is no way it will be done before she goes into the cut. Oh well Wednesday sees me outside the boat sorting out the scuffs and scratches on the hull so that I can get some more blacking on before relaunch. there’s not a lot to do so it does not take too long with the angle grinder and linishing disk to get it back to clean metal and get a coat of two pack primer on. Then its back inside the boat and start to clean up the bilges round the diesel tanks in the engine room so that I can get some paint on the top of the tanks where it has worn off. Then its spend some time in starting to sort out the container as I’ll need to vacate that as well. As a last little job I drain the cooling system so that I can finally get the TMV fitted. a long day with very little really to show at the end of it. It’s only a half day on Thursday but I get a bit more tidying done and a second coat of primer on the hull bits that have been cleaned. While I’m in the mood and have a paint brush in my hand I get a coat of best red undercoat on the top of the rudder and a top coat of red oxide on the service cupboard which I have to say is looking quite good.. Davids over on Friday and the first thing we do is to lift the engine room floor plates back in as that really is a two man job. It’s amazing how muscle memory works as I spend the next couple of hours banging my head on the ceiling as I walk through the engine room as the floor is now 2″ higher . Maybe it will bang some sense into me. While David is finishing off the 240v electrics in the engine room I get round to fitting the last socket outlets in the saloon and under the tug deck which means that as soon as David is finished we can fire up the port side electrics A quick trip outside as its not raining and I can get a coat of blacking over the primer to help restore the buildup prior to doing the whole hull. It’s strange thing about blacking it doesn’t seem to matter how careful you are it always seems to get everywhere and getting black out of the hairs on your arm is a painful experience . Back inside the boat and I take a look at the service panel midships. The panel fits really well but as it’s bead and reed glued up with some stiffening on the back it’s not properly flat so I decide that rather than hinging it I’ll put some machine screws to hold it in place and pull it flat. It looks really good when its in place and the screws are not too obtrusive. Davids finished the wiring in the engine room so we pop the cupboard in place. Disaster it doesn’t fit When I measured it up I measured the width at the engine room bulkhead and I hadn’t realised that the engine room sides actually pull in at the back so the damn thing is not long enough. The good thing is that as it is pocket hole screwed together I can simply take the offending bit out and put a new bit in. I just don’t know when I’ll get the chance to do it though. As Sunday was a really nice day it seemed the ideal time to get a coat of black on so over to the boat, get nice and wet pressure washing it and then get a coat of black on all over. Its amazing how much blacker new black is and Siskin looks good again.
-
Rain, rain rain and more rain just about sums it up. Monday morning it was down to the wood yard to pick up some timber for the porthole liners. I was intending to make them out of Rosewood but I was surprised at the amount that was needed and it would not have left me with enough for the galley doors hence the need for more timber. Choice is whether to try and find a timber which will match the Rosewood (difficult) or find one which compliments it. The local timber yard (Glenmere) is amazing. They actually have two very big yards one dealing with light timbers and one with the darker ones. I started off at the light yard and looked at some Meranti which looked a reasonable match colour wise but the grain was quite different. The guys suggested that the other yard so off there and the guys were so helpful (and knowledgeable). They reckoned that the best match would be Paduk but they didn’t have any so we had a look at at some Bubinga which looked really good compliment to the Rosewood so I decided to go for that. For the seven portholes and two vents I need three planks seven foot long x 14″ x 1 3/4″. Amazing!! It’s then a trip over to Kieth Hunt in Bromsgrove in the absolute pouring rain to drop the timber off. Monday gone. Tuesday and it’s the whole day spent sorting out the bulkhead round the range and finishing off all the bits and bobs round the galley as wednesday the work surfaces are going to be fitted. It’s a matter of getting it fixed down properly, the lift out panel sorted out and a quick coat of paint on. In a change of task it then back out with the angle grinder and cutting disk to trim off the range collar and flue pipe so that I can fit the trim which have been made by a local engineering firm in stainless. They even etch primed it for me . Wednesday morning and the guys turn up with the granite and and the first challenge is to get it in the boat. I’m glad that the long bit was cut in half as it’s a struggle to lift them up onto the tug deck and thread it through the front hatch. The guys (Nick and Rick) soon level off the work surfaces and get the joint glued up and the surfaces siliconed to the cabinets. As with watching anybody who knows what the’re doing it’s great to watch. Theres then a bit of drama as one of the up-stands breaks in two as there is a fault in the stone. It’s a real shame because it was cut in line with the work surface so the pattern matches. The guys head back to the factory to get another piece cut so I decide I can at least sort out some little jobs while the’re gone. I’ve got some little magnetic catches to hold access panels in place so a good place to start is the little “roof” at the back of the loo. It’s a bit of a struggle to get the screws in as the space is quite tight but at least the catches are adjustable so it’s not an “all or nothing” scenario. With one catch at the front and one at the back the access panel seems to be well secured. We’ll see what it’s like underway. The guys arrive back with a new piece of up-stand. Apparently there was just enough left and to be fair it’s not a bad match. By 3:00 the’ve got the job sorted and I’m really pleased with it. Again it makes a massive difference to how the boat looks. Last job before I head off is to fit the galley taps. It’s actually not too difficult as the access holes I cut in the cabinets are just about big enough to get two hands in. A magic day. Thursday and it’s a bit of a “Right said Fred” day as I’ve been conscripted to move a piano to my daughters house. We got it on to the trailer a lot easier than I thought we would but shifting it at the other end was all a bit Mr. Bean. As there wasn’t a great deal of time left after this exercise I headed off to the workshop to machine up some Rosewood trim for round the cooker. Halfway through routing the rebate there was a big bang, loads of sparks and smoke and the router juddered to a halt. After a quick break to change my trousers I stripped it down and found that the nose bearing had seized. I don’t know nothing seems to last these days I’ve only had this router for 35 years . A trip into Leicester and I luck out on the first shop I go to. The guy heads upstairs and in a few mins is back with the old bearing off the rotor and a replacement ready to go. With a total bill of £7.60 you can’t complain . With a functioning router again I can sort out the little bit of trim for the front edge of the bulkhead and get that fixed in place. I’m just wondering what to do next when I get a phone call saying that the basin for the bathroom has finally arrived so it’s back into town to pick it up. On Sunday I’m faced with a choice of a day of tennis or getting an extra day in at the boat. Given my love of tennis and loosing time with all the running around I did during the week it’s no real contest As I’ve finally got the basin thats the first thing to go up. It’s got a couple of mounting screws which are designed to go into very large nylon plugs but as the bulkhead is solid it’s a simple job just to shorten them a bit with the grinder and screw them straight into the bulkhead. I’ve not got all the necessary plumbing bits to connect it up but that’s not going to be a long job when I’ve got them. I would like to think that the bathroom is nearly finished but when I sit back and look at the stuff that needs to be done I realise that there’s still a way to go. Next up is a cupboard to hide all the electrics in the engine room. As its going to be painted to match the cabin sides it can be made out of ply so its a pretty simple construct. Now I can either build it in place which is a bit fiddly or build it complete and then put it in place. As I’d like to be able to remove it completly in the future if I ever need do any serious work on the electrics I go down the latter route. When I’ve got two sides in place I try to get it in place but (if you havn’t already guessed) I can’t get it into place as the vertical clutch rod is in the way . I reckon if I remove it it will be OK so I plough on. I just hope that when I do come to fit it I’m not wrong or I’ll have a lot of wasted effort. A bit of sanding and stopper over the screw heads and it’s time for a quick coat of primer.
-
Now the routine that I've got into in writing the blog is pretty simple. At the weekend or whenever I get round to it, I upload all of the pictures I've taken over at Siskin to my laptop, decide which ones I'm going to use, upload them to the web site and then sit down and write the words. Pretty simple really and a good way of reminding myself just what I've done during the week . When I did it this weekend I was shocked to find that I only had one picture and that wasn't of the boat . Where did the week go? What did I do? I seem to have lost a whole week of my life. I decided that I'd pop over to the boat and look at what I'd done and take the pictures, yeah that would work except that there was really only one thing that you could actually see had been done and that sure as hell didn't take all week so it's down to an increasingly unreliable memory. Oh well One thing I did do was to sort out the 24v electrics in the engine room. This is the challenge of trying to correlate the cryptic markings I've put on the cables with the (much changed) schematics and the new numbering system. If I ever do this again I will make certain that the FIRST thing I do is to sort out the numbering system and number each cable on the schematic as I draw it. It will save a LOT of time. Still with the numbering all sorted it's a pretty simple job to terminate the cable ends with bootlace ferrules and pop them in the appropriate bit of kit, with the exception of the cables for the loo which are 6mm sq to ensure there is not a lot of voltage drop. By the time I've got the ferrules on the end it is the devil of a job to get them into the terminal blocks but with a bit of messing around I eventually get them in although I may just go back and revisit them as I have another idea which may work better. The last little job in the engine room is to fix the trunking under the gunwales. Sticking it on is pretty easy but getting the screws in is more problematical but with some perseverance it's finally done. I've finished off all the last little bits of trim round the galley cupboards with the exception of sanding them down and varnishing them so it's ready for the worktops. A quick visit to Midland Stone Center to see James and see what he's got. Originally we were going to put the same surfaces as we have at home ( I know… boring) but he doesn't have any Verde Marinace in and says that it's now become very expensive (typical) but suggests an alternative called Juperana Fantasy (honest). It all seems a bit iffy but we go out into the factory and he gets the slab pulled out so I can see it. One thing the picture does not show is the scale of bit of stone as it is 4m x 2.5m. It's a really interesting slab and the colours complement the colours we're using in Siskin but I know that for some thing like this I need executive approval or I stand the chance of being in deep do do. Fortunately when Chris saw it she liked it to so next week will see the templating done and the stone being cut last bit of wood work to do is the half bulkhead around the range. It's the normal type of construction ½" ply backer with bead and read on top. There are some holes to be cut into it for access but I'm getting good at that now so it doesn't take too long and surprisingly the holes are the right size. I can't fix it down yet because I don't know how it's going to work round the range until the've been over to do the templating so I also can't get the bead and reed on. Still that shouldn't take too long once I know that I've got it right round the range. So a whole week gone – two pictures to show for it and a nagging feeling that there was something else I should have remembered At last summer has arrived and the weather forecast is for a decent start to the week so the first job of the week is to tidy up the cabin sides where there are little bits of rust coming through the primer. On reflection I really should have slapped a coat of gloss over the cabin sides as well but I didn't so I've got to deal with the consequences. It's almost a feeling of deja vu as I dig out the little angle grinder and the linishing disks and tackle the stbd cabin side. The rust is only a little bit of surface corrosion where the primer was thin so it doesn't take too long to knock it back with a 36 grit disk and then polish any marks out with a 80 grit one. However at the end the side looks a right mess but after spot priming it with two coat it's fine. Tuesday is a big day as they are coming over to template up the work surfaces in the galley and although I can't finish the bulkhead around the cooker until I've discussed how the granite will fit I do need to get the basics finished. I know that I'm going to bead and reed the bulkhead but I still havn't decided how to provide access to the service cupboard. The easiest way would be to have a simple lift off panel as I don't need regular access into the space but I reckon that I could make a concealed door that would be even better but it would need a little return to mount the hinges on which is no big deal to make just a strip of 18mm ply screwed and glued to the bulkhead with some triangular fillets glued and pinned in place. David from Midland Stone arrives to do the templating. When David templated our kitchen at home he did it with sheets of plastic cut and fitted to shape and I expected the same again this time but no things really have moved on a bit. David turns up with something which looks like an over-sized portable typewriter which he sits down on one side of the galley. It's got a pen connected to it by a wire and he simply touches the pen to the corners of the cabinets and it draws the shape on the integrated touch screen. He then can go in and edit it adding overhangs, notes for polishing etc. etc until he has a complete digital description of each bit of stone. Magic!. Out of interest I ask him if he can check how good my angles are and I'm pleased to say that they are all well within ½° Now that I know how the granite is going to go round the range I can finally finish off the little bulkhead, get it fixed in place and get the bead and reed on. I decide that it will be easier to cut out the hole for the cooker controls before I fix the bulkhead in place so it's dig out the bead and reed from the container and cut it to length. The worrying thing is that I'm not certain that I've got enough, it looks as if I will be one length short. How crap is that . A quick dig through the scrap heap and I find another length which has a split in it which I reckon I can glue up with some chair doctor glue. Whew!! With enough bead and reed to do the job I can get enough on the bulkhead so I can cut out the hole. I loose access to a couple of the pocket holes for the mounting screws but that's no big issue. As the hole is already cut in the bulkhead I can simply use a trimming cutter in the router to follow whats there, go round it afterwards with the rebate cutter and trim the corners up with a chisel and the jobs a good un. With the bulkhead mounted and the panel mounted in place it looks the business. I'll put some new hinges on the original door and repaint it to match the bead and reed and it will be great. Thursday's lot of odds and sods As I've got to go over to Midland Stone in the afternoon to decide on how the slab will be cut. Now I think that I've mentioned before that it REALLY does help if you plan ahead. I've got to fit the cylinder stat to the calorifier. It's not a hard job just cut a hole in the foam, pop the stat in place and hold it there with a bit of curtain wire wrapped round the cylinder. Well it would have been a simple job if I had done it BEFORE I fitted the shower bulkhead but with the bulkhead in place getting the wire round the cylinder with only a couple of inches spare on each side is a challenge. With the RF transmitter mounted on the bulkhead the jobs sorted. Next jobs a treat as it's time to fit the first lights . Remember the old second world war lights I bought some time ago from a guy who came round the yard, well I've cleaned and polished them, removed the blackout shields and even found some new gaskets for them so they look fabulous. I took one of them to the Crick boat show and got adapters and LEDs from Bedazzled which work a treat so I can't wait to see what they look like in the ceiling. I'd already cut the holes in the ceiling before we put it up but I think that I must have used a fitting which I had taken the bulb holder out as when I went to fit the first light the screws fouled but a quick sand with the Fein sorted that out. The lights look great in the ceiling and I can't wait to see them working. Thursday afternoon and I'm over at Midland Stone. The templates that David made are on downloaded to the CNC saw and with the stone in front of us it's a really simple job to slide the bits around the screen until we've got the pieces laid out so that we make the most of the patterning in the stone. I can't wait to see it finished. Friday and Davids back over to help finish off the electrics. While he's sorting out the cable terminations I whip the range chimney collar off and cut it down to size and then shorten the flue pipe as well. All we need to finish it off is the trim plate which is made but is waiting to be etch primed. After lunch is the big turn on as we put power onto the Mastervolt system for the first time. With the laptop plugged in it's really satisfying to see all the components appear on the screen and even more satisfying to find that all the pumps that are connected and set to come on at start-up do just that. Next thing is to get the lights working. Now we can turn the light circuits on and off with the laptop but we can't seem to get the switches on the wall to work. . Now the really nice thing about this setup is that it's easy to trouble shoot. We know that the light part of the circuit works because we can turn it on and off with the laptop so the issue has to be in the Digital Switch side. It's only a software change to switch it to another circuit and check to see if that works, which it does. Now the switch circuits are pretty simple, just 2 or 4 wires and one or two switches so in theory it impossible to mess them up but in the words of Eric Morecambe "I have all the right wires, but not necessarily in the right order" and it's just typical that the fault is on the first circuit we try. Still by the end of the afternoon we've got all the light circuits working properly. push for on, push for off, push and hold to dim and they even remember if they were dimmed when you turn them off. That's cool And to prove it heres a picture of a light. P.S. Summer is over. It's pissing down again
-
Been a couple of weeks since the last post. As Chris was on half term there was less opportunity to get over and work on the boat. My first job was to make a shelf to go over the calorifier to provide some storage space above it and to stiffen up the bulkhead before tiling it. I love doing little fiddly jobs like this (it sure beats real work). The little removable hatch is above the immersion heater and means that if it ever needs to be replaced it can be without having to remove the whole shelf which will make life a lot easier. With a coat of primer and undercoat on it I fit it into place and it certainly stiffens the bulkhead up but what I don’t realise at the time it also distorts the bulkhead a bit (more of this later) . Next little fiddly job is to cut and mount the main electrical panel. This is made out of 10mm Tufnol that I got off eBay. It’s really nice as it will take a thread well, is strong enough to carry all the stuff that needs to be mounted on it and is of course an insulator. It’s pretty easy to work with wood working stuff although it does take the edge off your tools quite quickly. With the bottom corner routed out it can be mounted on the engine room bulkhead with four 8mm stainless cap head screws. I’ve spaced it off the bulkhead by 20mm using some nylon spacers (eBay again). This allows me to fix some 18mm ply battens behind it so that I have something to fix the cupboard to. Jobs done Next job is to fix the 300mm cupboard in place now that the fridge is in and then I can get on with the last corner cupboard. I’ve only just got enough of the white faced ply to do a back and a bottom so it’s not a freestanding unit but it will work when the worktop’s fitted. With all the cupboards in place I can fix some rosewood capping to cover the raw plywood edges and all of a sudden it looks a whole lot better. Right let me make it clear right from the start I hate tiling. I never seem to be able to get that perfect look however hard I try and I’m really not looking forward to tiling the shower at all. I’ve done a lot of research and it seems that the adhesive to use is BAL Rapidflex as it will a: work on plywood (with a Unibond coat) and b: handle vibrations and flexing. The main downside is that it is bloody expensive at 30quid for 5Kg and that only does 2 sq m. By the time I’ve got 10Kg of adhesive, a bag of grout, a tube of silicon and the special trowel for putting the adhesive on it’s cost more than the tiles Pressure is increased when I note that the adhesive has a very short pot life so you’ve got to be quick. The stuff is also evil. It sticks like S.T.A.B. is a grubby black which seems to get everywhere and generally seems to be difficult to work. On top of this I find out later that it’s the devil of a job if it squeezes out through the joints to get them clean so the adhesive doesn’t show through the grout.. However notwithstanding that the first side goes on not to badly and although it’s got me sweating a bit it doesn’t seem to be too bad at all. Could it be that I’m actually getting better at this? The short answer is no remember that shelf and the twisting of the bulkhead? Well that rears it’s ugly head when I start the second wall and all of a sudden it all goes to pot as the corner joint is not straight and because I’ve set the tiles off the corner I’m now faced with unequal gaps etc. etc. and whatever I do doesn’t fix the issue. Added to the fact that doing horizontal mosaic is OK but vertical mosaic is another matter all together adds up to a pretty torrid afternoon and a very unhappy bunny come going home time. The following morning and I’ve decided that it doesn’t look too bad providing I stand on the T stud, squint and close the front doors . I’m actually just about ready to rip it all off but decide that the cost is too prohibitive so it’s got to stay. When it’s grouted up it doesn’t look as bad but if I could afford it it would go. What did I learn from this 1: get somebody who can do it properly is by far the best way forward , 2: don’t start with a full tile in the corner, this will allow you to adjust any out of square issues, 3: mix up very small batches of adhesive so if push comes to shove you can stop and regroup, 4: use small pins to hold any mosaic in place till the adhesive goes off, 5: get somebody who can do it properly Davids over on Friday again. He’s concentrated on getting all the equipment on the main electrical panel mounted and I’m fitting the shower enclosure. We’ve managed to squeeze all of the electrical gear onto the panel below the gunwale which is great and as there is very little necessity to get to it after it’s fitted it’s ok being low down. Friday passes with very little drama and at the end of the day Davids got the panel mounted and has made a good start on the 240v wiring. I can get onto the 24v stuff next week and hopefully wrap it up. I’ve got the shower enclosure up and all that needs doing is running the final silicon beads around but that can wait for a bit. It’s starting to look like a bathroom now.
-
Short week this week. Only managed 3 days on the boat. Still that’s better than none at all. Spent the first day and a half plugging and sorting out the screw holes in the panelling. Blimey its almost as bad as doing the washers on the hull sides. There’s well over 200 screw holes to be sorted and of course there all different shades so I need to cut plugs from a lot of offcuts so I can try and match the colour as best I can. By the time I’ve done this, glued the plugs into the holes (matching the grain direction of course ) cut them down with my little Japanese flush cutting saw ( a magic bit of kit) and then sanded them all flat a day and a half has just gone. Surprising how time flies when you’re enjoying yourself . However I think that the end result is worth the effort as the finished job looks great. I can’t wait until I’ve got some varnish on so I can see the finished job. As you all know the weather has been rather hot over the last couple of weeks. When I was working on the panelling I happened to glance up at the ceiling and the effect of the warm weather is there for all to see as despite the fact that when it was put up the ceiling was as tight as Andy and I could get it the expansion of the steelwork has left gaps in the boards. Not a lot I can do about it although I might try some Sikaflex in and see if that will work. i know that when the weather gets colder they will close back up but it really does offend the eye . Next job is to make a start on the shower and get the mixer mounted. All the servicing is done from the front of the mixer so the cut out in the bulkhead is a little bit more complex that just a couple of holes for the taps. Still it’s one of those fiddly jobs that at the end of you feel that you’ve done something decent although I can assure you the tile cutout will not be that intricate. Friday and Davids back over to finish off the hot and cold water services including the shower. While he’s doing that I get on with some bits of wood butchery to finish off all the worktop supports in the galley where there are no cupboard tops for it to sit on. and build the little (100mm) unit for the towel rail. All that’s left to do now is to fit the fridge and then sort out the corner cupboard and I can sort out the work tops. Of course after that there’s all the doors to build so we’re a long way away from completion. When Davids finished all the pipework it’s time to pressurise the system and check for leaks. Only one and it’s on an elbow that I fitted on the water-pump. Bugger . Last thing for the day is to try and decide how to lay out the electrical cupboard in the engine room. I had originally thought that it would need to cover the whole of one side of the back bulkhead but it looks as if we can fit all the gear in below the gunwale line so I’ve got room above for the engine control panel and hopefully some place to store the pipe. Result
-
Andy’s over for a few days this week to give me a hand panelling the cabin sides. It really is a two man job as I’ve got to prepare all the timber from sawn planks. We meet over at the boat on Monday morning and measure up what we need and mock up a corner piece so we can see what width we want to make the panelling. The styles over the sheet joints are fixed at 4″ so that we can set them at the same distance from the front bulkhead (the joints in the sheets are in different places because that’s where the battens were) and we reckon that the rails and end styles look better at 3″. Armed with the dimensions we head back to the workshop and dig out some timber. All of the panelling is coming out of 4 no. 12″ x 2″ planks of Rosewood so we spend the rest of Monday and the whole of Tuesday sawing, planing, routing the edges, sanding and finally varnishing the back of the panelling. This is really pleasant work as the cut Rosewood smells amazing and is so easy to work with. By the end of tuesday we have two large bags of sawdust (and I do mean large), twelve styles and 15 rails. There’s quite a bit of faffing as some of the rosewood has been nibbled by critters in the past. Now these are not your normal wood worms leaving a hole the sizes of a pin prick but something that leaves a hole you could poke your finger into (and I have fat fingers ) so it’s a case of working round them. The good thing about this however is that it has the effect of spalting the timber and leave the wonderful rich red colouration that I love. Wednesday morning and its bright and warm (again) and we head off to the boat armed with the machined timber, router table and mortiser for counter-boring the holes for the fixing screws. We set up a little workshop between Siskin and Diesel and Dust the boat next-door. Its great being able to have plenty of space to work in especially with the long rails. We get the top two rails up on the stbd. side really quickly and I’m starting to think that we’ll have this done in a day (stupid boy). Now I’ve decided to scribe the ends of the styles rather than let them into the rails. It’s a bit of a gamble but I think it will work and it should be a bit easier to do once we’ve set up the router. A little bit of work and the test joint looks really good. Now this works well on the joints that are square but the front two are not as the top rail sweeps up. The angle that it’s out of square is only 1.7° but we musty spend at least 2 hours in getting and acceptable fit. Oh well. While Andy is working on preparing the ends of the styles I sort out some rosewood faced ply to go on the bulkheads between the galley and the bathroom. I have JUST and I do mean JUST enough to do it but there are no more big bits left so if I do end up needing any more I’m shot. I reckon that the best way of fixing it is some small pins round the out side and impact adhesive as I can’t really clamp anything. Now you can buy impact adhesive in 500ml or 2.5l tins. One is too small (as I subsequently found out) and the other is far too large. End result is that I only get three out of the four panels fixed before I run out of glue. . Andy and I soldier on (it’s to bloody hot ) and by the end of Thursday we’ve got all but one panel in the bathroom completed. All that’s left now is to plug the holes, sand it down and varnish it but the job looks great already. Davids over on Friday and it’s a big day as we’re hoping to get the range up and running. First job is to go round all the pipe work and make certain that it’s tight, Davids brought his pressure tester over so we plug it in, pressurise the system up to 1 bar and have a cup of tea . After tea the pressure’s has dropped a bit so we spend a half and hour trying to find the leak only to discover that it’s one of the bleed valves which does not seal properly . With that fixed I mix up some antifreeze and get the system filled while David fixes the chimney collar in place. We’re then ready to go or as the case may be not. We spend the next couple of hours trying to get the burner to fire up. It’s clear that it’s simply not pulling the fuel through. We try all sorts of things and in the end resort to 1: me sucking the diesel thought the pipe (uuuug ) and 2: priming the lift pump with some airline oil which finally gets it going. As there’s only a small amount of water in the pipes it heats up incredibly quickly so we can’t run the burner for long but I thinks it’s sorted. With that working we sort out the washing machine water feed so it doesn’t get in the way and we can get the machine pushed back and as an added bonus get the controls back onto the engine. A great week, loads of progress
-
Well it actually feels as if I've got something done this week (at last). And as a bonus it hasn't rained (as much) First job of the week was to sort out a little pocket behind the central heating pump as it fouled the plywood. A couple of Min's with the little router and the jobs done. Even better still I connected the dust extractor to it and I don't even have to clean up afterwards. then it's time to get all of the central heating controls wired up. Now I'll be the first to admit (and have in the past) that I have no enthusiasm for plumbing and thus have no experience of sorting out the electrics associated with heating control. Now to say that the instructions are not quite consistent with reality is a bit of an understatement which is also not helped by the fact I've got a different diverter valve to the one in the instructions so none of the colours on the wires seem to match. In the end I decide not to connect up the valve as I'm changing the actuator for a Sunvic one so I'll tackle that problem when I get to it. Talking of actuators if you buy a Sunvic actuator as a spare it is 70 quid. If you but a complete valve and actuator it is 57 quid. Wheres the logic in that then? With all the heating wiring done and the fresh water pump connected the midships service cupboard is finished With impeccable timing the washing machine arrives and Mike gives me a hand to get it into the boat. It doesn't quite fit as it fouls on the water feed pipe but its nothing that can't be sorted pretty quickly. It's surprising what a difference it makes as the galley looks as if it's nearly done (I wish). Note the universal law of horizontal surfaces that as soon as one appears it get filled with junk The next exciting activity is to fit all the 240v sockets on the stbd side. With this done it actually means that I can power up that circuit (with the help of a plug on the end of the wire that will go to the breaker) and all of a sudden I can get rid of the extension leads and cable reels in the forward cabin as I can use the wall sockets. Absolute bliss. No more tripping over leads. Enough sockets to plug in everything I need at one time and even the ability to set up a "proper" galley although I'm not too keen on the work-surfaces so I think I might change them . Fired up by this new found neatness I embark on a blitz on the inside of Siskin. It takes a while but at the end of it there is a sort of perverse satisfaction at a job well done. Of course the reality of the situation is that I should not have let the boat get into such a pig tip Next task it to tackle the little wiring center under the tug deck. It's got the switch interface in for the saloon light, tug deck lights (up and down) and the tank level interface for the fresh water tank. While I'm looking at it I suddenly think why the hell did I put this here, why didn't I put it in the midships service cupboard which would have made a lot more sense? The answer is that I don't know the answer . I'm certain it made sense at the time but it doesn't now. Still it doesn't stop anything from working it's just a bit more work. And no the picture is not upside down. All the cables enter the box at the top so I need to mount the interfaces upside down Now its back to a bit of wood butchery and cut the hole in the floor for the shower waste. Damn cutting this Jarrah is hard work and you'd better make certain that it's right first time because making any changes is a nightmare. After this its a more relaxing activity and time to glue up the larder unit. It goes together pretty well and is pretty rigid considering it's open backed. I manage to get it up on the tug deck and into the boat on my own but it doesn't bloody well fit in fact as my old dad would say "it fits where it touches boy, and it don't touch nowhere". Now I simply don't understand this at all. It was actually cut from the same template as the bulkhead so it should be exact. Puzzling to say the least. So it's out with the Fein and a happy hour or so is spent making loads of sawdust as I slowly get it to be a decent fit. Some more time spent putting the last (300mm) unit together and at last I can get a proper idea of how the galley layout works. I'm pretty pleased with it as again there seems to be more room than the drawings would have you believe. Result. Nick pops over on Thursday to get a final coat of paint on the engine room. As I'm forbidden to make any dust at all I call it quits early on in the day and head home via Costa for a relaxing cup of coffee . Davids over Friday morning and makes a start on fitting the in line filter for the range while I head off to the Dentist to have an extraction (money from my wallet that is, not a tooth). Blimey I'm in the wrong trade. I reckon that the 5 min exam works out to just under 500 quid an hour . By the time I get back David's finished the fuel filter and started on the shower waste. and has hit a problem in that the 1½" BSP hose tail he has got doesn't fit the waste trap so it's back in the car for a troll round the plumbers merchants in Harborough to see what I can find to do the job. In the end the only solution I can actually get is to run a short piece of 40mm waste from the trap to a 40mm to 1½" BSP stub and screw the hose tail onto that. In the end when we come to fit it this works really well . I use the shower tray as a square to set the bulkhead up which is just pocket hole screwed to the floor, ceiling and back bulkhead. I've got some flexible up-stand to go round the shower tray to seal the bottom tiles which looks as if it will work really well so that is stuck to the sides of the try before we silicon the bottom and pop it into place. It's then a simple job to reach under the floor from the floor hatch which is right next to it and connect the waste up. Pour some water down it to check for leaks (none) and the jobs a good 'un . Next job is exciting in more ways than one as we tackle getting the flue pipe for the range through the roof. We measure and re measure and re re measure to make certain we've got the centre of the hole in the right place before we drill it. We then pop a pilot hole through making certain it's upright. Then the really exciting part starts as we cut a 95mm hole in the steel with a hand held drill and even more so when we cut a 115 hole out of the ceiling with the drill held upside down. Great for getting covered in sawdust and breaking your wrist if the saw jambs. Still with the hole cut we can pop the collar in and set the flue. Much to our relief it's dead plumb looking forwards to the door side and backwards to the bulkhead between the galley and bathroom. PHEW . All that needs to be done now is to drill and tap the holes for the screws to hold down the collar and mark the collar so it can be welded (the tube to the collar ring is only tack welded into place so you can adjust it to get it set correctly for the roof angle) and the end of a most satisfactory week has arrived.
-
I seem to be getting less and less time on Siskin at the moment and although I am pretty pleased with progress I can’t help thinking where I would be if I had managed to get full time working on her. Monday of course was a holiday so Chris and I decided to do what everybody else seems to do on a bank holiday and go to the shops. Now normally this would rank high on my list of things NOT to do on a bank holiday but as the object of the exercise was to pick out a fridge and washing machine for Siskin I reluctantly agreed to go . Now heres an interesting story, I’d had a look on the web and sorted out a shortlist of stuff to look at in Currys so off we trot to the Mega store (sic) in Leicester. First problem of course is that they don’t have all the stuff we want to look at although we do manage to choose a washing machine. Second problem is that on the web they are offering a 10% discount on bank holiday Monday and when I ask about a discount in the store there is a lot of shaking of heads until somebody finally finds (and I kid you not) a notice in about 8 point text buried at the bottom of one of their A4 printed sheets that they are also offering this in the shop, but nobody seems to know how to process it. When I ask about the fridge we want to see the guy says “oh you’re better off ordering that from the on line store”. End point of the story is that we don’t buy anything from the store, retire for a cup off coffee and head back home and order it off the web. What a palaver Tuesdays a great day, for once the sun is shining and the weather is nice and warm, so its actually a real pleasure to be working on the boat. One of the first little jobs is to fit a couple of the light switches. I have to say that using the cord ends is a far better way of terminating the cables than the crimp on lugs I originally bought. The look so much better as you don’t see the crimp, work well on both single and double wires and take up a lot less room. Oh and as a further bonus are about half the price . Do use them. With a little bit of trimming so that the mounting nuts clear the wood work their on and look splendid. Next task is to finish off the loo as I had not bolted it down because I wanted to put some little boxes over the chocolate block connectors I’d used so with those in place I could bolt the loo down and it’s ready to go. Another job finished Next on the list is to make a start on connecting up the cooker. With the panel off I can see where the mains in has to go but the issue is how to connect the other end. The problem is that I’m using the standard wiring panel for a central heating system which is just in reality a load of chocolate blocks in a box. Now in total the neutral and earth will have five wires going into them Just about possible if you are using bare wires but not possible if you are using cord ends which you have to to comply with RCD so a little bit of lateral thinking sees the range and the pump fed into a remote connector which is in turn connected to the wiring panel getting the number of connections down to four which is managable. That prblem solved but I still can’t finish the job because I need some 5 core heat resistant cable which David is going to bring over on Friday. Oh well another day of steady working gone and only two light switches to show for it. Wednesday and Thursday I spent messing around fixing the brakes on the car so high hopes that when David gets over on Friday we can see some progress again. Friday and things are starting to come together at last. The heatshrink has arrived so I can finish off the wiring and I’ve just been told the shower tray has finally arrived. David makes a start on plumbing the waste for the sink and I get on with the wiring. Its actually quite therapeutic as for once I’ve got organised properly with a sensible cable numbering system and all the right bits and bobs so a couple hours work see all the 24v cables fitted and network cables shortened / made. The end result looks nice and neat I just hope it works. It’s pretty amazing that this little lot (plus two more of the smaller units under the tug deck) controls all the electrics ahead of the engine room including lights, pumps, tank level interface etc. and even lets me plug my laptop into the sytem to set it up. I like it (and promise I’ll try to get a bit more of a life) David in the meantime has been working away on the sink getting the waste all fitted and the seacock on the skin fitting but then we find that the bit of 40mm waste pipe we’ve got is push fitting not solvent weld so I decide to trip into town and pick up some pipe and the shower tray. Yahoo (exclamation of joy not a well known search engine). Now we need approx 175mm of pipe and the shortest length I can buy is 3m. Anybody need 2.8m of 40mm white solvent weld waste pipe . With all the bits to hand we can eventually get the sink waste finished and tested and its fine. A few more minutes gets the hot and cold pipework up and the job is sorted. Isn’t it just sods law however that the pipes come out directly under the waste so they need to jiggle around it. Our next job is to mark up for the range flue which is definitely a two man job. With me on the level and David eyeballing it against the bulkheads (given some of my recent attempts at lining things up the is the safest way believe me) we can get the right distance across the boat. To get the right position along the boat we work off a couple of the board joints above the gunwales which I know are pretty accurate and true and a plywood straight edge which will follow the curve of the roof. Pretty soon we have an X marks the spot but decide that we don’t have the correct hole saws so that’s as far as we can go on that one. Over a cup of tea we discuss what we need to do for the electrics in the engine room and especially the 240v stuff and soon have a plan. David will get that stuff sourced and I can make a start on that soon as well. Final play of the day is to unpack the shower tray and get it into position so that we can figure out how we are going to sort out the waste. It’s really nice to get it in as it finally shows how much room we have in the bathroom (and it proves it all fits in). I’ve got a whole heap of stuff I can get on with now. Hopefully I can get a good run at it next week and make some real progress.